Soft Foot has often been noted as the most inexact science part of the shaft alignment job. Historically, when people think of Soft Foot, they often want to neglect, ignore, or otherwise do everything possible to not deal with it. This is one of the traps that leads down the path of bad habits, bad alignments, and more problems down the line.
Shaft alignment can be thought of as two things:
- Aligning the shaft centerlines of rotation
- Checking for and correcting Soft Foot
Soft Foot, in fact, plays so much of a role in shaft alignment, that if one were to analyze the 5-Step Alignment Procedure below, one can see that Soft Foot appears in 2 out of the 5 steps. Therefore, Soft Foot can be thought of as almost half the alignment job.
5-step Alignment Procedure:
- Pre-alignment checks – including inspection and cleaning of machine supports
- Rough alignment – “eyeball clean” (with bolts loose) and Rough soft foot Loosen all bolts and “fill any obvious gaps”.
- Initial alignment – Get to within 5 to 15 mils at coupling or less than 20 mils at feet.
- Final soft foot – All feet less than 2.0
- Final alignment to tolerances and documentation
What is Soft Foot? Soft Foot is Machine Frame Distortion.
How does it happen? Soft Foot can happen from several things, including:
- Bent Feet
- Bad Bases (warped, uneven, flimsy)
- Dirt, rust, corrosion under feet
- Excessive or missing shims under the feet
- Pipe stress
- And any combination of the above…
What should be done about it?
A full and extensive diagnosis should be done on every machine foot to determine whether or not the tightening of that particular bolt is causing machine frame distortion, and thereby causing shaft misalignment or machine frame strain.
A few helpful tips to remember are:
- Minimize total number of shims under each machine foot to no more than 4 shims per foot.
- Make sure the area is clean, including machine feet, bases, shim packs, etc.
- Jack bolts should be backed off, so they don’t interfere with the soft foot check.
- When checking for soft foot, only one machine foot should be loosened at a time, and the deflection or movement at the shaft noted.
In conclusion, soft foot plays a big role in machine reliability and therefore should not be ignored. Laser alignment systems such as the Easy Laser XT series can help diagnose and correct soft foot.
Read: Common Causes of Machine Failure: #2 Soft Foot
by Diana Pereda
Before going on a trip, we typically plan ahead. What we are going to do, what we are going to pack, where we are going to go, and places to visit each day of the trip. When starting an alignment job, it is not that different. We must plan ahead. This means being ready to thoroughly clean the mounting base, having the right tools for the job at hand, and allocating the necessary number of hours to get the job done right.
Proper preparation for success can go a long way. Cleaning underneath the feet of the machinery will greatly decrease the chances of having a soft foot, thereby increasing the machine’s ability to respond accurately to corrections. Also, check under the entire machine for loose debris. Foreign objects under the machine can cause soft foot as the machine is lowered during alignment corrections even though the feet of the machine and shim packs are spotless. Another thing that should be considered during pre-alignment is having the right set of shims. These must be the right size for your application, corrosion-proof, and made from high-strength material. They should also be free of burrs, bumps, nicks, and dents of any kind. But first and foremost is planning for safety. Locking out/tagging out the machines is the VERY first step before starting the alignment process. Getting the right training to operate your laser alignment system and understanding misalignment will also save time and ensure success.
Let’s summarize a few of these important planning and execution steps:
- Lock-out and tag-out
- Thoroughly clean the mounting base and feet
- Visually inspect for foundation, grout, and baseplate defects, and wear and tear
- Make sure to have the right tools for the job
- Make sure to have the right shims
- Inspect and replace damaged shims
- Allocate the right amount of hours
- Have the right training
- Make sure your high-quality laser alignment system, such as an Easy-Laser XT770, is charged and all components and needed accessories like specialty brackets are there.
Download our 5-Step Shaft Alignment Procedure for a simple and effective procedure for shaft alignment of rotating equipment!
Related Blog: Pre-Alignment Checks plus Essential Clean-up and Preparation Tasks
by Diana Pereda
March 2021 – Pumps & systems
In olden times, when hard work beyond the ability of a few humans was needed, a horse or a team of oxen was the solution. Even greater power requirements were fulfilled by wind or watermills. This form of driving machinery lasted for centuries and the mechanical components involved required little in the way of alignment, beyond rudimentary good fits. When self-powered machinery was invented in the early 19th century in the form of James Watt’s steam engine, the pace of industrialization began to quicken. With this revolutionary power source, the volume of manufacturing increased rapidly and a greater demand for water and other fluids in industrial processes was created.
While early machinery often transmitted power via gear drives and flat leather belt drives, it did not take long for engineers to realize that directly coupling the driver to the driven machine would result in improved efficiency of power transmission with all the savings entailed therein. It is only with the invention of modern multiple V-belt drives with negligible stretching and slippage that the efficiency of belt-driven systems again rose to compete effectively with direct-drive systems.
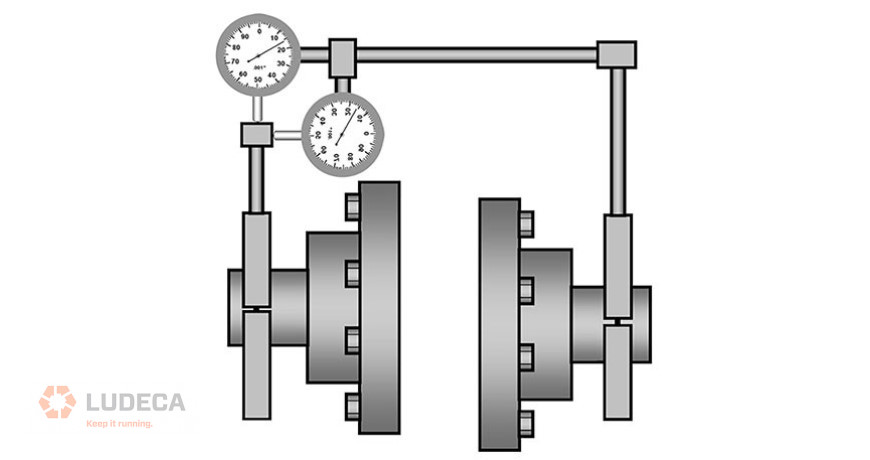
In early days, speeds of rotation were slow and alignment of both belt-driven and directly coupled machines was traditionally accomplished by eyeing it, using a straightedge and feeler gauges. Good machining of surfaces and great care was usually all that was needed to obtain a satisfactory result. This modus operandi persisted through the 1940s. By the end of World War II, the United States was in a commercial position that favored industrial production: almost all of the world wanted manufactured goods, and the U.S. was a principal source for them. If someone wanted a car, a TV, or a sheet of stainless steel, it was likely made in the U.S. Global competition did not exist to nearly the extent that it does today, so cost-consciousness was not what it is today. Resources were plentiful, environmental regulation minimal, and craftsmanship excellent. Plants could afford to install standby machines for all critical processes and concrete foundations were poured a little deeper. People designed machines using slide rules. Today, computers trained to shave away every unnecessary ounce of metal do the designing.
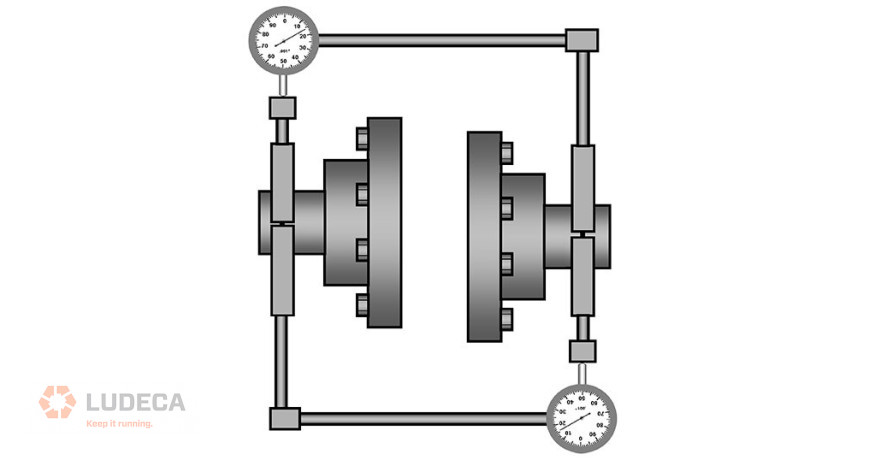
In the 1930s, the average speed of rotation of an electric motor was 900 or 1,200 rotations per minute (rpm). Back then, the straightedge was king. Pumps had stuffing boxes, and when they sprang a leak, the mechanic simply tightened the packing glands to compress the braided cotton and asbestos packing rope until the leak went away. Often, the shaft was later found to be scored from the pressure of overtightening. As industrial production flourished and a wide range of new products were introduced, harsh chemicals demanded different containment approaches and mechanical seals became more prevalent. This demanded precision alignment. As technology improved, and Europe came online again with significant industrial production, the 1950s saw speeds of rotation increase to an average of 1,800 rpm. It was quickly discovered that as speeds of rotation increased, the need for good alignment also increased—not just in linear proportion, but exponentially.
The straightedge could do a fine job with offset misalignment if used with care on coupling surfaces of well-bored couplings; but who could consistently guarantee such conditions? Yet, it was not good enough with regard to the angularity between the shafts. This was due to the limited measurement resolution afforded by eyesight over the short span of the straightedge across the coupling hubs. As apprenticeships and general craftsmanship declined, the assurance that coupling was machined concentric to the mechanical centerline of rotation, and that its faces were perpendicular to said centerline, or even that it was entirely round, waned. Also, foundations became weaker and not as flat as they ought to have been. Put simply, the alignment of surfaces via a straightedge or a dial indicator rotated around a shaft (not with the shaft) was no longer good enough. New ways to align the actual rotating centerlines of machines needed to be devised, and now the dial indicator (formerly strictly a machinist’s tool) came into its own. Its use by millwrights in machinery shaft alignment did not really take off until after WWII. Now the so-called “rim and face” method became king.
Click here to continue reading the entire article: Reduce Errors From Poorly Designed Machinery by Alan Luedeking
by Diana Pereda
When you are bolt-bound or base-bound on a critical machine train—usually one that is very difficult to move—it is not enough to just fix (make stationary) individual pairs of feet to obtain alternative shimming or moving solutions. You need even more flexibility, such as the ability to minimize moves across all the feet. The concept of stationary and movable machines is obsolete: all machine feet are movable under given circumstances, so it is essential to be able to find the minimum corrections necessary to align to any conceivable centerline, including fully optimized centerlines or centerlines optimized for any desired number and combination of fixed and movable feet. Such flexibility is imperative when working with machinery on the critical path. Therefore, look for this capability when selecting your next laser shaft alignment system.
For example, while trying to make the horizontal corrections on the misalignment below, one may run into a bolt-bound situation on the far-right machine. Moving the back feet of the motor over 100 thousandths may not be possible.
However, by making all machines movable and letting the laser alignment system optimize the alignment moves, we now have achievable corrections at each pair of feet:
Notice that the back foot move of the motor on the far right dropped from an impossible 108.8 mils to a readily doable 11.9 mils.
Watch our Shaft Alignment Know-How: Bolt-Bound video to learn about the options of achieving alignment when in a bolt-bound or base-bound condition.
by Diana Pereda
When performing shaft alignment, the alignment is typically measured by rotating both shafts at the same time. Why is this? The reason is that the coupling is already installed, so it is convenient to do. The other reason is that rotating both shafts is the only way to measure the true rotating centerline of the shaft. Not doing so results in measuring only the surface alignment, which is subject to surface finish imperfections, shaft straightness, and hub concentricity issues.
When should you remove the coupling for an alignment? For starters, you typically need to rough-align a machine before installing a coupling. This can be carried out with a laser alignment system. Another situation is for machines that are difficult to turn with the coupling in place, which requires removing the coupling in order to take a measurement. Finally, some machines have shafts that are coupled through fluid drives, so rotating both shafts simultaneously could prove very difficult.
Uncoupled measurements are very similar to coupled measurements. The goal is to make sure the shafts are at the same rotational angle when a measurement is taken. To make this task easy, Easy-Laser implemented a digital readout of the angle on each sensor in all XT series shaft alignment systems. I have found this invaluable for performing an uncoupled alignment. One simply needs to rotate one shaft to a determined degree and simply look at the sensor to match both shafts to the same rotational angle; once this is carried out, a measurement can be taken.
Some uncoupled alignments are made difficult with a shaft that is hard to turn or requires a turning gear that does not allow manually matching the shafts’ rotational angles together. To greatly simplify this task, Easy-Laser has included an “uncoupled sweep” measurement mode. This mode allows the user to turn one shaft so the laser beam will sweep by the first sensor, and then turn the other shaft so that the sensor will sweep past the laser again. This sweeping motion causes a point to be automatically taken for each time the sensors sweep past each other.
Related Blog: Uncoupled Misalignment Measurement Made Easy
by Diana Pereda
The Problem:
The customer complained of excessive vibration on a wastewater pump driven by a diesel engine. Upon performing an alignment check, the machine shafts were found to be grossly misaligned. Furthermore, proper alignment was found to be impeded by a base-bound condition of the engine combined with external horizontal forces caused by the exhaust stack.
The Solution:
A base-bound situation means a machine must be lowered to bring it into alignment but insufficient shims are present under the feet that must be lowered to permit removing them in order to achieve the alignment correction. Using an Easy-Laser XT770 laser shaft alignment system, it was easy to determine alternative possible corrections to overcome the base-bound condition. Horizontal alignment was also achieved using the graphical display of machine shafts and the live-move mode of the alignment system.
Savings:
Easy-Laser XT770 made it possible to find positive (instead of negative) shim corrections to immediately achieve alignment to within tolerance. This meant that enormous time and expense were saved by not having to disconnect and remove the engine, as well as hire a machinist and portable milling machine to mill down the base-plate of the engine.
Watch our Shaft Alignment Know-How: Bolt-Bound motion graphic video to learn about the options of achieving alignment when in a bolt-bound or base-bound condition.
by Diana Pereda
The following tips are ideas to consider for when “the going gets tough”, meaning that problems like residual soft foot, “bad geometry”, or becoming bolt-bound impede your ability to easily obtain an excellent alignment. But first, a few definitions:
- Residual soft foot: More soft foot than you are comfortable with, but can’t do anything about. Can be caused by problems like slightly angled feet or a bit of pipe strain.
- Bad geometry: Equipment where the distance from the coupling center to the front feet is equal to or greater than the distance from the front feet to the back feet.
- Becoming bolt-bound or base-bound: When alignment corrections can’t be made because you have run out of room in the anchor bolt holes in the feet, or have to come down but have no shims left under the feet to remove.
Final Vertical Misalignment Correction (Horizontal Misalignment already close)
1. Position front feet close to offset tolerance. Finish the alignment by moving the rear feet only.
2. Final foot positioning should make offset at the coupling center decrease. To achieve this, position feet as shown in the below example:
3. One must avoid leaving feet positioned with opposite signs, even if the values are very small. Below is an example:
4. One must also avoid allowing the position value of the front feet to be higher than the back feet value, even if they have the same sign. Shown below.
Notes:
- The above rules apply to horizontal corrections as well.
- Remember to torque the anchor bolts on small equipment in steps.
Watch our Shaft Alignment Know-How: What’s Misalignment video to learn the causes and effects of having misalignment in your rotating equipment.
by Diana Pereda
I’m a potential failure! I am the result of improper equipment design, procurement, installation, maintenance, and operation. I exist under extreme conditions for which I was never designed. I haven’t hidden or been silent, but most have ignored me and all have allowed me to grow. I’ll become a risk of severe damage and injury.
One day I will reach my full potential and show everyone what a failure I have become. At that moment, everyone will wish I had been given the early attention and mitigation I deserved.
Don’t feel sorry for me, because I am not alone, and will most likely return. I have created many other potential failures like myself. Some of those failures will cause even more harm and damage. Most likely, I will be reborn on the same equipment again and again due to improper maintenance practices.
If this does not concern you, then do nothing and let me show you what an equipment failure can really cost you when you least expect it and didn’t prepare for it. If you don’t like having me around, then what can you do? Here are some activities your maintenance and engineering departments can perform to prevent me from happening and ensure your equipment is operational upon demand, meaning reliable:
- Design for reliability
- Design for maintainability
- Design for operability
- Manage maintenance backlog
- Plan work, then schedule it and finally ensure it is properly executed
- Focus on PdM activities like vibration monitoring, IR thermography, lubrication analysis, and many more as a routine exercise
- Ensure precision maintenance is routinely done
- Perform operator checks
- Maintain properly written and continually optimized preventative maintenance activities that return value
- Provide training for operators, mechanics, and engineers to help ensure precision maintenance, proper operation, and reliable design
- Perform root cause analysis
- Ensure failure modes and effects analysis is a routine part of your maintenance and reliability efforts
- Ensure that you have identified all critical assets
- Ensure you have mitigation plans in place to deal with critical equipment failures
- Ensure that critical spare parts are available, properly stored, and easily accessible when needed
Visit our Knowledge Center for resources and tools to help you succeed when implementing and using our maintenance technologies! Watch our video tutorials, download infographics, plus explore other helpful information to reduce equipment failures and downtime.
by Diana Pereda
In general, laser shaft alignment systems have increased the ability to eliminate misalignment defects. There are many systems on the market, with varying capabilities, but the core benefit has been that the computer and laser work together to create an alignment report that can be used to assess and determine corrective action.
With advances in the interface and measurement technology, the skill required to take measurements has been reduced when compared to older methods, such as dial indicators. Thus, more users can perform the job with less training for the task of gathering the measurements. Unfortunately, this convenience has in some cases resulted in the good practices of the fundamentals of shaft alignment falling by the wayside, given the perceived ease of use. It has gone so far that some systems have marketed the idea that alignment can be done faster and in fewer and fewer steps to the point of rough alignment not even being necessary!
Is rough alignment not necessary?!?!
The claim is that if the laser can measure the misalignment without the laser going outside the detector, the alignment can be determined and the entire correction is done once. Anyone who has done at least one alignment in the field knows that this is far from the truth as you can’t escape physics in shaft alignment.
Depending on the setup, dial indicators could measure far more misalignment than a laser setup. Let’s say you had a situation where the indicators showed 300 thou misalignment. If you performed the right calculation would you expect to move the machine one time and get it within tolerance? Absolutely not! The reason is that the two shafts would be so strained as to the force required to bring the machines back together, that the coupling would be impossible to install, the shaft would deflect, and the forces would cause incorrect soft foot measurements. Again, you can’t escape physics.
The solution is to rough align the machine! It’s a best practice as per our field-proven 5-Step Shaft Alignment Procedure, which applies to all shaft alignment tools.
What about measuring severe out-of-alignment conditions with a laser alignment system?
First of all, if you are aligning an existing machine that has been running and did not experience a failure, I will give the previous alignment technician the benefit of the doubt that it was not severely out of alignment, and 99% of the time, you will not encounter the laser going out of the detector.
Second, if it is a rough alignment there is a chance it could move out of alignment for any laser shaft alignment system, single or dual beam. In rough alignment, you will typically align with a straight edge and most likely be within laser detector range to get an approximate set of readings. In one case, I checked the rough alignment of the machine with a 27-foot separation between machines (shown below.)
The lasers moved 8″ from the detector on both sides. Regardless of whether you had a single beam or a dual-beam system, there is no system on the market with a detector that is 8″ in size to handle this rough alignment, nor is it necessary, provided you have a dual laser beam type laser alignment system.
How do you rough align with a laser alignment system?
Fortunately, I used the Easy-Laser XT770 which features a dual laser configuration. Using a process called “coning” I was able to rotate both shafts from 90 to 270 degrees, move lasers to the middle of travel and then use them as a visual indicator to align the machines until both lasers hit the center of both detectors. In one vertical and horizontal movement, like magic, the axes of rotation were rough aligned. The millwrights on hand were amazed at how quick, efficient and intuitive this method was – which can only be done with a dual laser alignment system. This means the machines were roughly aligned 27 feet apart without dealing with a complicated movement of the laser during measurement as the single laser systems require. We were then able to do a full 360-degree measurement, get the values, and start the alignment corrections and finish the alignment as per the 5-Step shaft alignment procedure.
Related Blog: Benefits of Performing a Rough or Initial Soft Foot in an Overall Alignment Procedure
by Diana Pereda
We welcome you to read the previous blog in this series, “What is Machine Train Alignment and How Important Is It? Part 2”
ANALYSIS 2: THE REFERENCE MACHINE IN THE TRAIN CANNOT BE MOVED
Now we have to face the situation of the big 172 mils moves at DF2, Compressor 3 back foot. For this, we are going to make use of the XT770 Adjustment Guide to predict what will be the minimum moves needed at Compressors 1, 2, and 3 to get the misalignment to excellent tolerances.
Here is a brief description of what is the Adjustment Guide and how it works:
It is Firmware utility built into the Easy-Laser XT770 alignment system to aid the aligner to predict what will be the minimum moves or shim changes required to align all the machines in the train to get the alignment at each coupling within tolerance when there are limitations to adjustment such as when Machine 1 cannot be moved in a 3-or more machine train. Let’s explore what can be done in our alignment.
As stated in Blog1 the calculated corrections at Machines 2, 3, and 4 are to bring the whole train to alignment to Machine 1. We also spoke on how valuable this information is.
Now that we know ‘the whole picture’ of the train and we know that Machine 1 cannot be moved, we can make ‘virtual moves’ and predict the minimum required moves at each pair of machine feet to get the alignment between consecutive machines to excellent tolerances. See examples in pictures 7, 8, 9, 10, 11, 12, and 13.
When we first invoke the Adjustment Guide we see a graph pictured below.
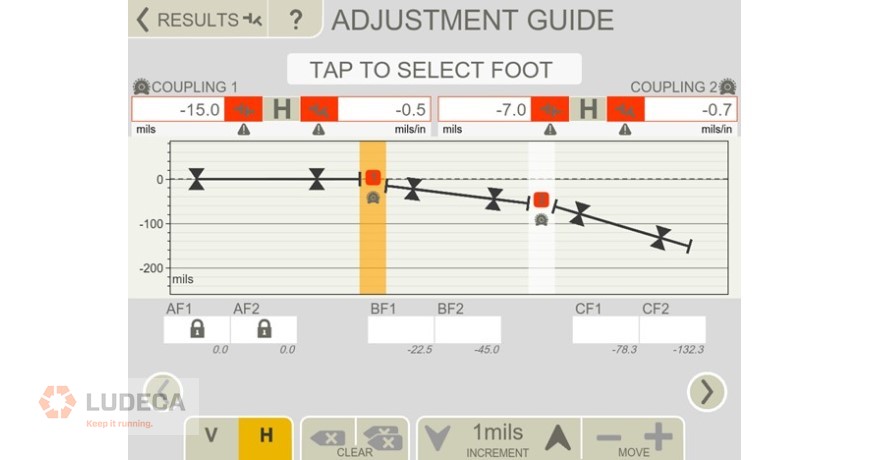
Allow me to describe what we are looking at in Picture 7. Several things:
- The actual misalignment at couplings 1 and 2.
- Machine 1 feet, AF1 and AF2 are ‘Locked’ because they cannot be moved.
- We see empty white rectangular boxes under BF1, BF2, CF1, and CF2.
- Underneath the white rectangles, we see the needed adjustments to make to bring machines 2 and 3 into alignment with Machine 1.
- We see the interval set up, set to 1 mils by default, and of course adjustable up to 125 mil increments every time you press the + or – icon. In other words, user-adjustable to save time.
- The left and right arrows allow the user to move down or up on the machine train.
Having said this, we used the arrows to ‘virtually move’ BF1 and BF2, see below.
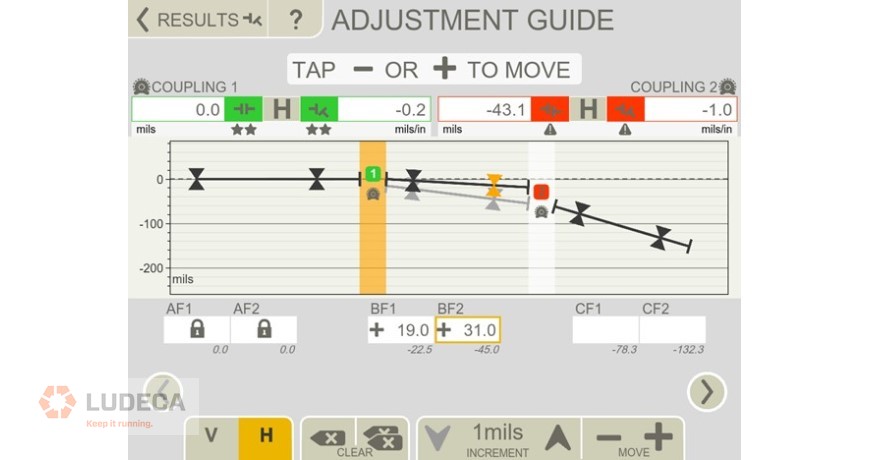
Picture 8 shows the final virtual adjustment on BF1 and BF2 to get Machine 2 to ‘Excellent’ alignment relative to Machine 1. Please note a couple of things:
- We needed to move machine 2 only 19 mils at BF1 and 31 mils at BF2 instead of 22.5 mils and 45 mils to get to excellent alignment. And more importantly…
- It allows us to leave the angularity of machine 2 with an angle such that machine 2 ‘points towards machine 3’, thus minimizing the moves at machine 3 to get it to perfect alignment with Machine 2.
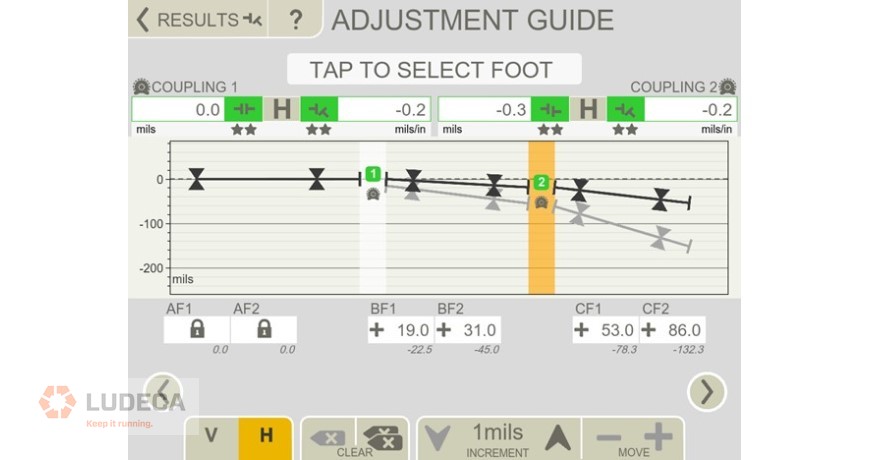
Picture 9 above shows the ‘virtual moves’ needed at CF1 and CF2 to get Machine 3 aligned to excellent tolerances with respect to Machine 2.
Please note that to achieve Excellent alignment the move at CF1 is only 53 mils instead of 78.3 mils and at CF2 it is 86 mils instead of 132.3 mils. Also note that we left Machine 3’s angularity in such a way that Machine 3 points towards Machine 4, thus minimizing the moves that will be required at Machine 4.
Picture 10 below shows the last 2 couplings and DF1 and DF2 with ‘empty’ values.
Underneath the empty rectangles that are waiting for the input of the virtual moves, we see the required move to bring Machine 4 (Compressor 3) into alignment with Machine 1, which are, DF1 150 mils and DF2 172.5 mils. However; what is needed, as pointed out before, is only to bring Machine 4 into alignment with Machine 3, not with machine 1. See Picture 10 below.
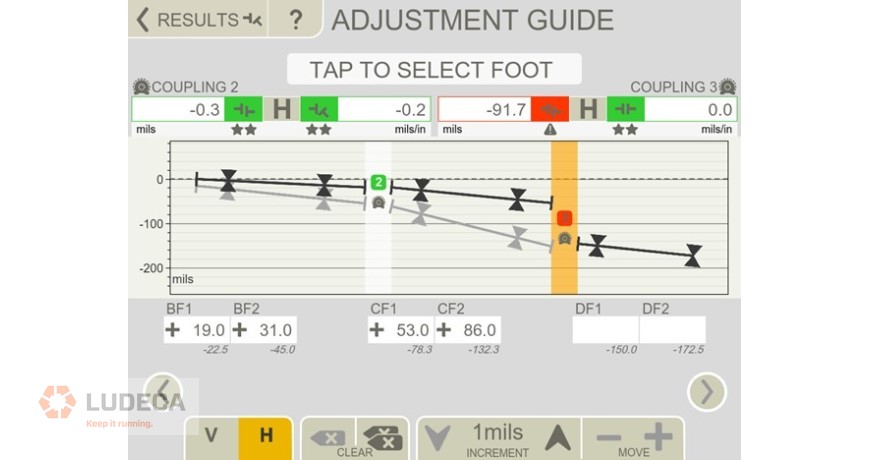
We continue the process as we did before making ‘Virtual Moves’ at DF1 and DF2 in any order until excellent alignment is achieved. See Picture 11 below.

Picture 11 shows that we have ‘Virtually Moved’ DF2 90 mils.
We will proceed to move DF1 and DF2 in any order until we reach excellent alignment. Remember the ‘increment’ is adjustable, hence when getting close to alignment it can be lowered to 1 mil to make more precise moves.
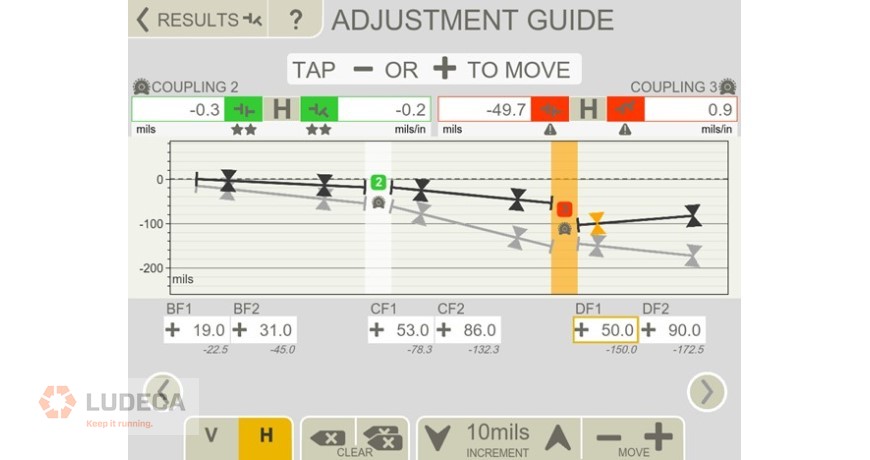
Picture 12 shows that we have moved DF1 50 mils and DF2 90 mils.
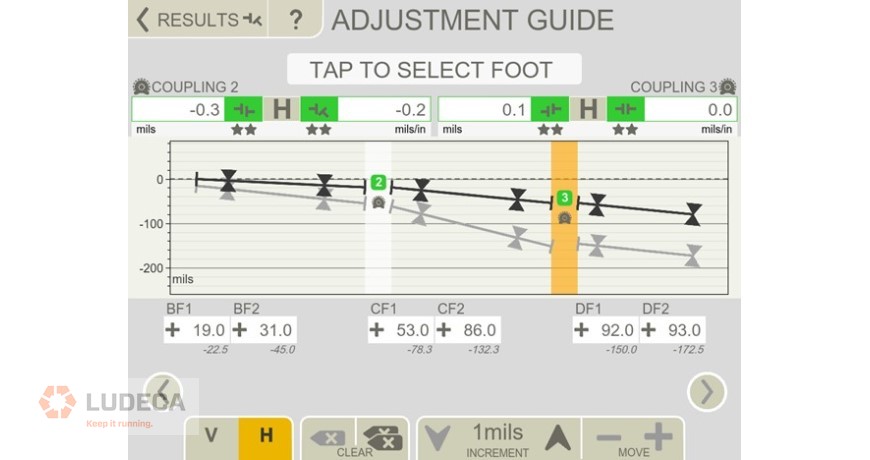
Picture 13 shows the moves required at DF1 to be only 92 mils instead of 150 mils and for DF2 only 93 mils instead of 172.5 mils to achieve alignment to tolerance.
As we can see, the Adjustment Guide utility is a tremendous aid that helps the aligner predict what is going to happen and most importantly find out if he or she will be able to obtain his or her goal.
by Diana Pereda
Shaft Alignment is a critical step in any world-class maintenance program, and when done properly, can help decrease unscheduled downtime and keep equipment running longer and more efficiently. This means machines need to be aligned within the recommended tolerances based on the RPM of the equipment. However, this is sometimes easier said than done, especially if any residual soft foot is present, or due to bad geometry in the movable piece of equipment. If you find yourself struggling to complete an alignment to tolerance, here are some tips that, when combined with Ludeca’s 5-Step Shaft Alignment Procedure, may help you complete the alignment faster and with less frustration.
- Get the position of the front feet close to the alignment offset tolerance. Once the front feet are close to or within the tolerance value, complete the alignment by correcting the rear feet only.
- Try to leave both the front and rear sets of feet with positions having the same sign, either positive or negative.
- It is not desirable to leave the position value of the front feet higher than the position value of the back feet. This means that the final position value of the rear feet should be larger in value than the position of the front feet.
The following scenario is an example of how these rules can be applied to help you complete an alignment to precision tolerance as defined by the ANSI standard (ANSI/ASA S2.75-2017/Part 1.) This standard defines three acceptance levels: Minimal, Standard, and Precision. These acceptance levels, as well as the corresponding tolerance values for 3600 RPM, are shown below in Figure 1. The scenario below was prepared utilizing an Easy-Laser® XT770 Shaft Alignment System and the Adjustment Guide feature. Our Easy-Laser XT Series is one of the few laser alignment platforms on the market today with the new ANSI alignment tolerances built-in giving the user the freedom to choose between traditional tolerances, the new ANSI standards, or custom tolerances.
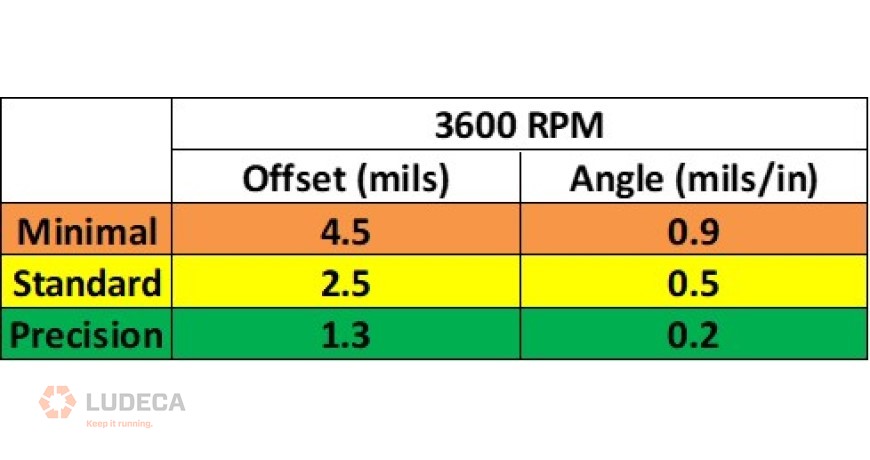
In Figure 2 we have our shaft alignment results measured on equipment running at 3600 RPM, where the position of the front feet is at +1.0 mils and the position of the rear feet is at –0.6 mils. This creates misalignment at the coupling with an offset measuring +2.6 mils, which puts us in the Minimal tolerance range. We need to make some adjustments to improve the alignment in order to reach the precision tolerance range, but how? Let’s try following the recommended tips!
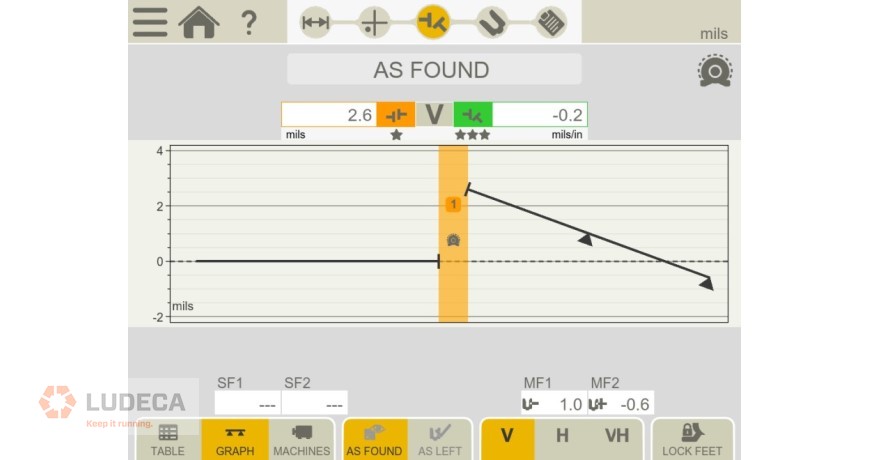
If we look at the position of the front feet in Figure 2 we see that we are at +1.0 or 1.0 mils too high. Since the position of the front foot is already less than the desired Precision Offset Tolerance Value of ±1.3 mils (shown in Figure 1), Tip 1 says we should leave the front feet where they are and complete the alignment by correcting the rear feet only. Looking at the position of the rear feet in Figure 2, we see that we are at –0.6 or low by 0.6 mils. Using the Adjustment Guide feature on the XT770, let’s see what would happen if we add 1 mil worth of shims to the rear feet.
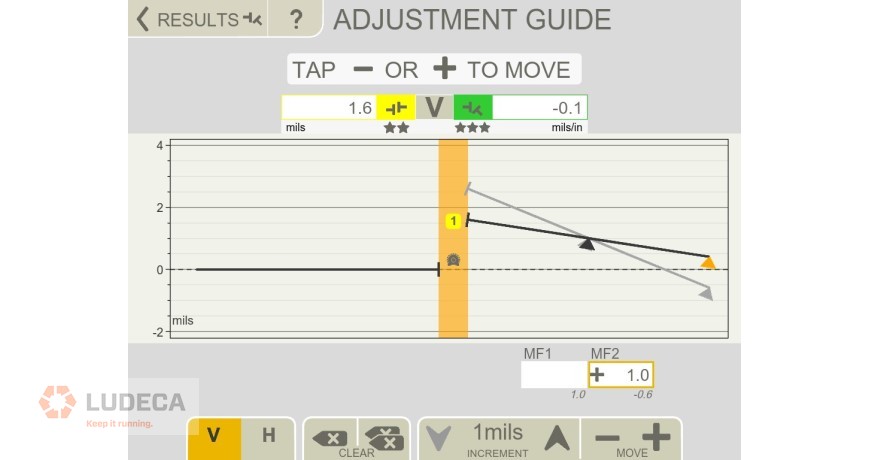
In Figure 3, we add 1 mil of shims to the rear feet of the alignment result that was shown in Figure 2 bringing the new position of the rear feet to +0.4 mils with the front feet still at +1.0 mils. Although both feet now have the same sign, satisfying Tip 2, we see that this still produces an offset measuring 1.5 mils at the coupling, putting us within the Standard alignment tolerance range. Although we did improve the alignment slightly, we still are outside of the Precision alignment tolerance that we are pursuing. What would happen if we added another 1 mil to the rear set of feet bringing the final position of the rear feet to +1.4 mils?
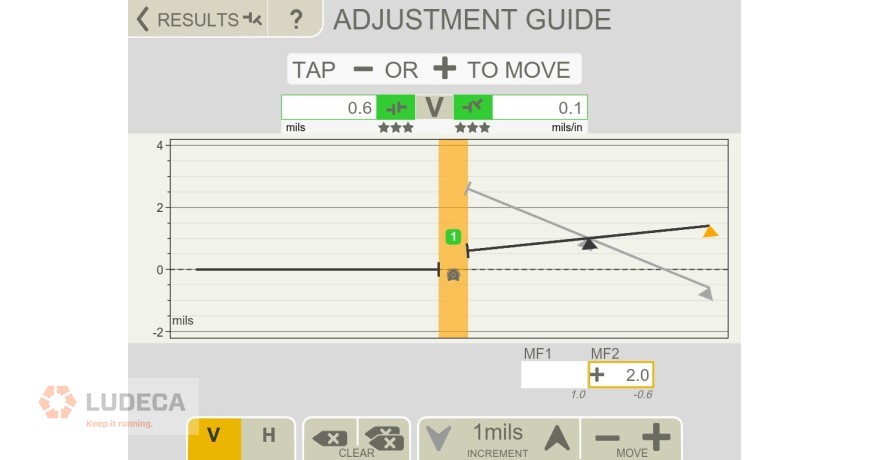
Now in Figure 4, we have added 2 mils worth of shims to the rear feet of the alignment result that was shown in Figure 2, bringing the final position of the rear feet to +1.4 mils with the front feet still at +1.0 mils. Now we see that the position of both the front and rear sets of feet are positive in value satisfying Tip 2. Additionally, the positional value of the rear feet is greater than the positional value of the front feet, thereby also satisfying Tip 3. Now if we look at the misalignment measured at the coupling, we have an offset measuring just 0.6 mils and putting us well within the desired Precision alignment tolerance. In addition, the angularity value has also decreased and is well within the precision alignment tolerance range. Note also that adding shims is always easier than removing them, especially if you do not have enough thickness of shims left under the feet to make the desired negative correction possible.
We hope these three tips will make your task of precision aligning machines much easier.
Request your complimentary copy of our Shaft Alignment Fundamentals Wall Chart which highlights the ANSI/ASA Shaft Alignment Tolerances as well as information and guidelines for the implementation of good shaft alignment of rotating machinery, best practices, soft foot, tolerances, thermal growth, and much more!
by Diana Pereda
We welcome you to read the previous blog in this series, “What is Machine Train Alignment and How Important Is It? Part 1”
ANALYSIS 1: ALL MACHINES IN THE TRAIN CAN BE MOVED
Since ALL 4 machines in the train can be moved we have many options.
Option 1:
Let’s see what the minimum moves will be for the whole train. How we do that with the Easy-Laser XT770? We simply make ALL 8 feet in the train movable. NO LOCKED FEET in the train. See Picture 3 and Picture 4 below.
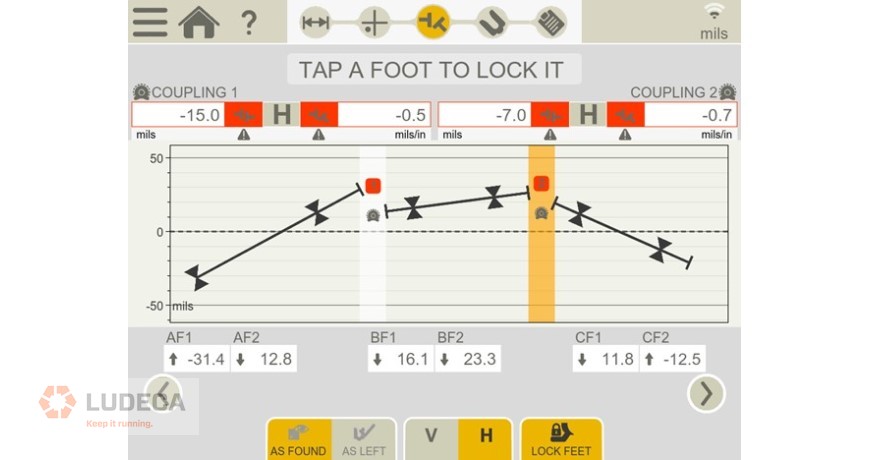
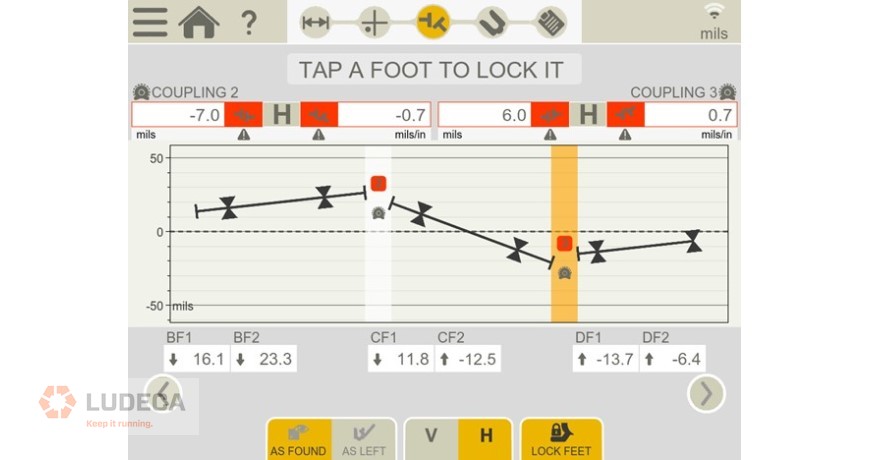
What can we conclude from those two pictures? A couple of things:
- What we see in the graphs is what we call: ‘The Optimized Alignment Line’. Simply the XT770 finds the Alignment Line that will minimize ALL MOVES. The proof that we are looking at an Optimized Line is that the SUM of the Absolute Values of the Negative and Positive corrections (moves) is the same. In those pictures, we see that the Negative Values add to 64 mils and the Positive Values add to 64 mils.
- We see that the big 172 mils move at DF2 is now only 6.4 mils.
- We also see that the biggest move in the train is at AF1 (Turbine Back Foot) only 31 mils.
Option 2:
For example, we can explore if we can minimize the Turbine move. The XT770 allows you to ‘Lock’ any feet. We Locked AF1, which was the biggest move in the Optimized view, and CF1 arbitrarily. See Pictures 5 and 6 below.
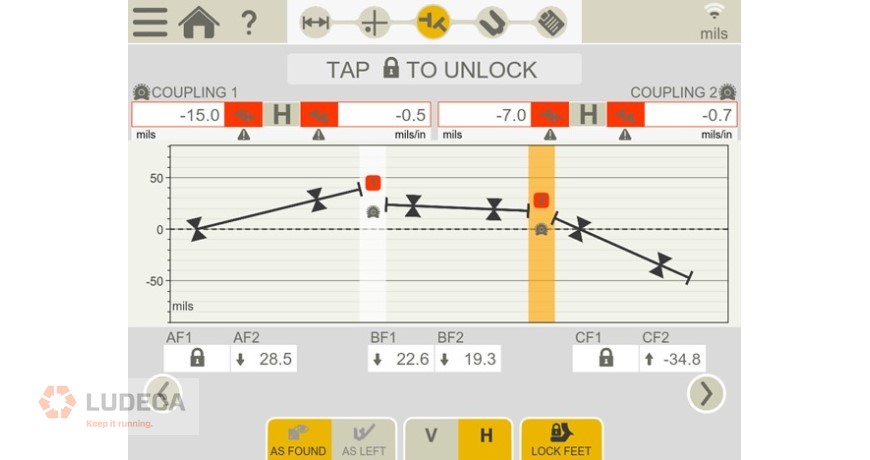
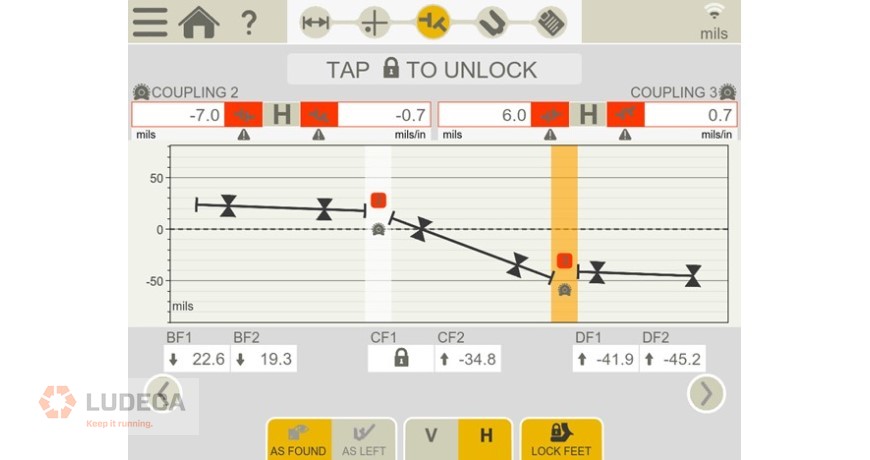
The XT770 calculates the moves for the remaining feet you are to move. As you see, not a bad option but not as good as moving both Turbine feet.
As mentioned above, in addition to moving ALL feet you can ‘Lock’ any feet to be able to analyze the best option. Going through all the possible combinations will make this blog extremely long torture for the reader.
by Diana Pereda
Saving short-term money at the cost of long-term loss could never be a good idea. Soft foot is one of the most prevalent problems in rotating machinery, and the improper use of shims is one of the bad guys. This is way too common and is the cause of countless machinery problems worldwide. But let’s not let that happen. Instead, let us guide you through the ideal shims procedure, for an easier alignment task.
1. Initial check
For safety, always remember lockout and tagout of the machine. Then you can go about inspecting the foundation, grout, and baseplate with your eyes. If there is rust, scale, paint, or dirt, remove all of this from under and around the feet. Then you replace damaged shims with new ones, that are corrosion and crush resistant.
2. The right shims and the right number!
Don’t fall for the temptation to use homemade or low-quality shims! In the long run, this will cost you more than you gain short term. Usually, you will also need more shims if you use homemade ones. Use as few shims as possible. Three pre-cut shims should always be enough; in extraordinary situations, four could be needed. The fact is that using too many shims can, in itself, cause soft foot.
The use of anything other than high-quality shims is the main factor when it comes to machines being worn out beyond salvation. Pre-cut, stainless steel shims are perfectly flat and will, as a bonus of sorts, also prevent corrosion.
3. Measure and insert shim
Use a micrometer to measure the thickness of shims 1 mm and thicker. These thicknesses are nominal and not necessarily exact. Insert the pre-cut shims under the foot of the machine until they touch the bolt. Withdraw slightly.
4. Shim size
Use a shim size that adequately supports the load zone of the foot. Whenever the contact between the underside of the machine’s feet and the surface of the base plate or frame is less than perfect, we have what’s called soft foot. Ever sat at a wobbly table? Then you know. The annoying situation where one leg fails to reach the floor is bad enough. For a machine in an industrial context, this is more than just irritating; it will lead to damage if not taken care of.
5. Sandwich
With pre-cut shims, you’ll get a safer and easier machine alignment as well as better machine performance. Burr-free edges and rounded corners prevent injuries from occurring. Sandwich thin shims between thicker ones. If you have used high-quality shims, your machine should now be almost aligned. You are ready to move on to fine adjustment, i.e., aligning your machine using all the tricks of the trade.
Download our Shimming Best Practices Infographic which outlines 7 things to consider when using shims for machine installation or machine alignment plus Step Shimming.
Thank you Roman Megela with Easy-Laser for sharing this informative article with us!
Related Blog: Machinery Alignment Shimming – Things to note about precut stainless steel shims
by Diana Pereda
Do your washers resemble cones?
If so, you could be falling victim to a common headache experienced in some shaft alignment jobs. What could mistakenly be diagnosed as soft foot or coupling strain, “dished” or “cupped” washers center themselves in the feet causing the machine you are aligning to move laterally as you tighten the hold-down bolts. Prevent this from happening by performing pre-alignment checks and replacing any washers that exhibit this defect. Also, check the surface of the machine feet for similar grooves that have been cut by washers in the past. These grooves can also cause this effect and make your alignments challenging.

Related Blog: The Impact of Washers on Shaft Alignment
by Diana Pereda
What is Machine Train Alignment?
Machine Train Alignment is a multi-coupling alignment where two or more consecutive machines can be adjusted.
For example, a 3-coupling train (4 machines), such as a Gas Turbine driving 3 Compressors.
NOTE: A 2-coupling (3 machine) train such as a Pump–Gearbox–Motor, where the Gearbox in the middle is determined to be NON-movable, is NOT a Machine Train; it could be treated as one but that is not the best option. It is best to treat this as two separate alignments using the Gearbox as the ‘Stationary Machine’. In one alignment, align the Pump to the Gear-Box, and in the other, align the Motor to the Gear-Box.
NOTE: Normally, most laser shaft alignment tools will use the first machine on one end of the train, say the left machine, as the Reference Machine, and after collecting the data at all couplings the alignment tool will combine all the misalignment values to calculate the required moves to align ALL the machines in the train to the original reference (alignment line), in most cases machine number ONE.
Is this the goal we are trying to achieve? NO! We are trying to align two machines next to each other. Then, what is the value of the machine train program? A TREMENDOUS VALUE, as it gives the aligner “the Overall Picture” of how all the machines sit with respect to the reference line and therefore also how they sit with respect to each other. Why do we need to know this? Because we need to avoid getting ‘Bolt Bound’ or ‘Base-Bound’.
We will use an Easy-Laser XT 770 Laser Shaft Alignment tool with data collected in a 4 machine train (3 coupling) for this blog. In a four-machine train, after reading the misalignment at each of the three couplings, we found the following Horizontal Misalignment values versus the entered Misalignment Targets that were desired. See Pictures 1 and 2 below.
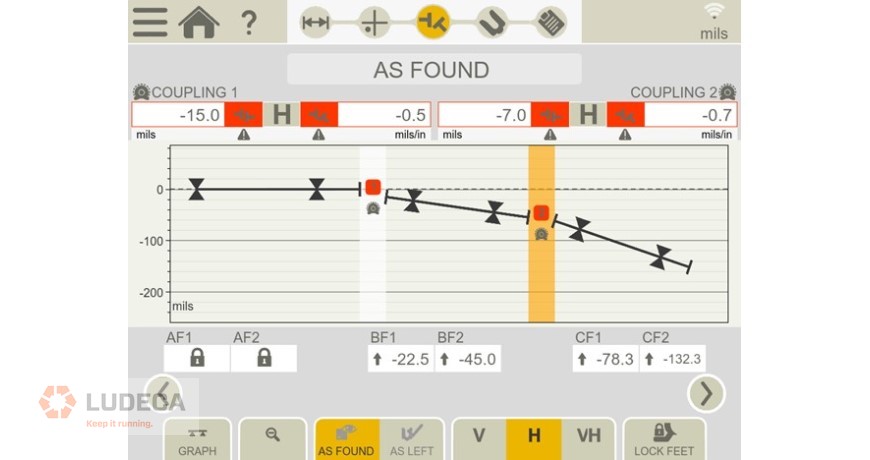
What we observe in Picture 1 is a laser alignment tool depicting the first TWO couplings (3 machines) in the THREE coupling train. We see that the first machine is the reference (Stationary Machine), we observe both the misalignment at couplings 1 and 2, and the required Horizontal Moves to align machine number TWO (BF1 and BF2 moves) and machine number 3 (CF1 and CF2 moves) to the reference machine number 1. We begin to see a big move at CF2, 132 mils (Thou). CF2 is the Compressor #2 Back Foot.

What we observe in Picture 2 is the misalignment at couplings 2 and 3 and the required corrections to bring all THREE machines to Machine ONE, the original reference (Alignment Line). See a possible problem now? Do you think we will be able to move DF2 172 mils (Thou)? DF2 is the Compressor 3 Back Foot.
In my next blog, we will then see how easily we can analyze and solve the apparent bad situation we are facing.
NOTE: Please realize that the pictures you saw are ‘GRAPHS TO SCALE’ of the misalignment. Observe the scale on the left side of the graphs.
by Diana Pereda
As stated by Daniel Keys Moran, “You can have data without information, but you cannot have information without data.” The driving factor for any reliability program is data; but how do you gather and record the right data to achieve your maintenance and reliability goals? By documenting and generating clear reports with the necessary data. This will permit statistical trends to be developed that can improve uptime and productivity as well as justify repair or replace decisions.
First, let us look at what information should be gathered and documented, followed by how and where you should store the data so that you can use this data over time to develop trends and Key Performance Indicators (KPI’s) to drive your reliability program forward. Harness the data coming out of your maintenance operations and turn it into actionable information that will make a difference in the way you work and what you accomplish.
What data should be captured?
The following list describes the equipment and information that is necessary to make informed decisions and drive the improvement process forward in a maintenance program:
- Instruments used for measurement
- Person(s) completing the task(s)
- Description of the asset
- Date and time
- Tolerance requirements
- As-Found and As-Left measurements
- Reference to the standard used
- Appropriate signatures
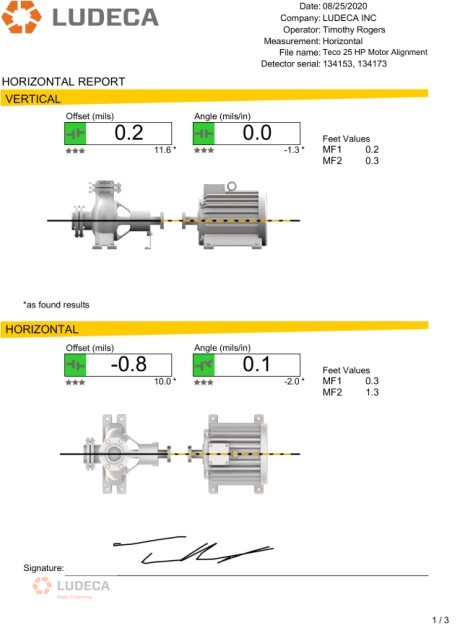
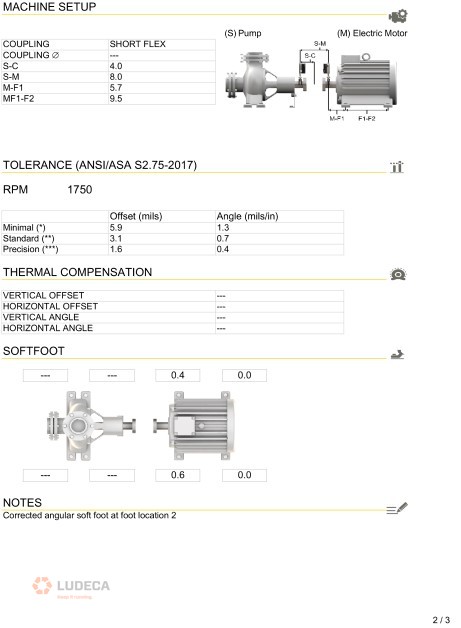
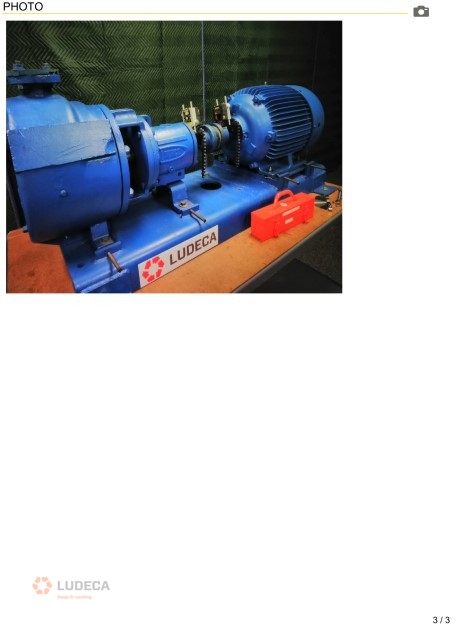
Where should my data be stored?
Now that we’ve assembled the needed information, we need to store this data in a way that we can easily access it and refer back to it to identify problems and develop solutions. The preferred storage location should be within your company’s CMMS (Computerized Maintenance Management System.) If your CMMS is configured properly, you may be able to store the As-Found and As-Left measurements directly in the work orders to trend them, thereby allowing the CMMS to automatically create work orders when an asset is out of tolerance. The next alternative is to link the report to a work order and/or asset, allowing the information to be easily accessed within your company. If you don’t have a CMMS, another option is to create a folder structure on a shared drive where the reports can be saved. Keep in mind that there should be a consistent naming structure that is followed by everyone with access to the shared drive so the reports can be ordered correctly and easily located. This will require some training.
What are the Key Benefits?
The goal of any maintenance organization should be asset management with the equipment operated and maintained in a cost-effective manner. Creating detailed reports starting from when the equipment is first installed and continuing throughout the life of the asset allows you to predict when failures may occur so that you can effectively plan and correct the issue in the most efficient manner, in advance of an unplanned failure. With the right data gathered and properly stored, organizations can analyze and develop maintenance strategies to ultimately increase equipment availability, decrease production downtime and generate greater profits for the company. These detailed reports allow communication between operations and maintenance and drive continual improvement throughout the organization by identifying, mitigating, or preventing losses. Ludeca provides a wide range of reliability technologies that generate detailed reports that can be easily shared within an organization to help you “Keep it Running.”
Visit our Knowledge Center for resources and tools to help you succeed when implementing and using our maintenance technologies! Watch our video tutorials, download infographics, plus explore other helpful information to reduce equipment failures and downtime.
by Diana Pereda
Belt-driven rotating equipment is commonly found in all types of facilities. Typical applications include rolls, fans, motors, shafts, and blowers. It is important to maintain that equipment in order to increase its reliability. Maintenance is essential in today’s industrial environment to ensure assets and equipment are running as reliably as they should.
Like any part that can wear over time, belt-driven equipment should be periodically inspected. This includes the inspection of the pulleys, sheaves, and belts. Worn belts and sheaves should be replaced. Belts should be properly tensioned and the equipment aligned.
It is important to have quantitative values so that the condition of the machine can be evaluated and monitored over time. One way this can be accomplished is through ultrasound and vibration readings. Another value that can be quantified is alignment and belt tension. Belt tension is commonly quantified by force and deflection and determined during the installation of a new belt.
Pulleys and sheaves be should be properly aligned. However, the most common methods rely on pass/fail methods. This includes straight edge and visual laser guides. While they are better than not performing an alignment check, how does one quantify the degree to which the alignment is accomplished? In the same way that it is important to quantify shaft alignment, belt alignment should be quantified as well. This supplies numerical information which the reliability engineer can trend and decide the condition of, in order to plan, rather than react to a maintenance operation.
Our Easy-Laser XT190 belt alignment tool can carry out this task and supply numerical values for the current belt alignment condition. A laser transmitter and receiver are placed on the sheaves and pulleys to be aligned. The results are instantaneously projected through the iOS and Android app to supply the current alignment condition in real-time as well as the required corrections. An added benefit is that the users typically only need to access each pulley without having to pull the entire coupling guard off (provided proper lock-out and tag-out procedures are followed). With this advantage, one does not need to visually figure out the alignment as it is all displayed in the app.
The result is that alignments take less time and the reliability engineer can have quantitative data to decide the current and trending alignment condition. This one tool can help move belt-driven rotating equipment from the reactive maintenance stage to the planned and eventually to the precision domain.
Download our Pulley Alignment Guide Plus 5-Step Procedure for information on the implementation of good pulley alignment of belt-driven equipment including terminology, alignment methods, belt maintenance, storage, and tensioning as well as a 5-Step Sheave/Pulley Alignment Procedure.
by Diana Pereda
We previously discussed in our series of soft foot, Types of Soft Foot: Part 3 Squishy Foot. In this follow-up blog, we will discuss Induced Soft Foot.
What is induced soft foot?
Induced Soft Foot: Occurs when stress-induced external forces such as pipe strain, electrical connections, or severe misalignment combined with a stiff coupling pull or push on the machine creating a distortion of the frame.
The precise alignment of rotating machinery is affected by many factors and components. From the very foundation the equipment is mounted upon to the equipment itself, and extending to anything connected to the machine. Because of the tightness of the tolerances that are aimed for during these alignments, it takes little to put stress on a machine.
In rotating equipment, the internal alignment of the bearings that hold the shaft in place is very precise. As we’ve seen in this series the mating between the feet and mounting surface can stress these internal components and clearances. What else can cause internal misalignment of the bearings?
Condition 4: Induced Soft Foot
- Caused by external forces such as pipe stress, coupling strain and strain from conduits and braces.
- Correct by removing any external forces on the machine.
Download our Soft Foot Find-and-Fix Infographic which outlines the of types of Soft Foot including causes and corrections.
by Diana Pereda
When performing shaft alignment, the best way to accomplish the horizontal (side-to-side) corrections is using jack bolts. You do not want to hit your machines with a hammer in order to move them. Always remember to back off the jack bolts on the opposite side. Remember that once you are done with your side-to-side correction, we recommend that you always back off all jack bolts after the alignment is completed and the anchor bolts are tight.
Where to put the jack bolts on your machine?
Place the jack bolts in such a way that they do not interfere with the shimming and allow you to pivot the machine you are moving. See figures 1 and 2 below.
Correct positions of jack bolts

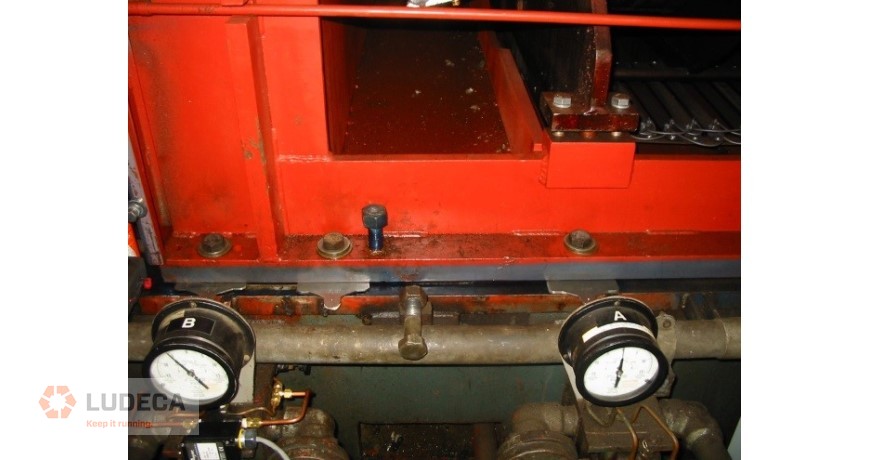
Incorrect position of jack bolts
The picture below shows the jack bolt “not in a good position”—it will interfere with the shimming.
by Diana Pereda
Belt-driven machines are the Rodney Dangerfield of the maintenance industry – “they don’t get no respect!” For example, look at the image below. Belt-driven machines do need a little bit more TLC than they currently get. I want to show you two innovations that will greatly improve your maintenance efforts on these highly efficient drives. I also want to show you why the general way in which we work with belt drives is a good example of what keeps reliability unachievable for many.
First, let me say that there are some individuals/organizations who really understand the value of doing this work right. I am reminded of a gentleman called Gary Burger who wrote a very good article on improving the efficiency of belt drives. He says that he “expects to get three to five years from a belt that is running 24/7.” And I believe he gets that, and you can too. Keep in mind that this is not a roof fan that will spin forever, this is a working machine that needs sizable horsepower to turn it over.
The reason I say these drives do not get the respect they need is experience. Like many of you, I have seen belts pried off, then a new set pried on. I have seen large sheaves installed with air guns and never checked for runout, so they vibrate in the axial plane. I have seen string used for alignment or a length of angle iron from the steel rack used as a straightedge for alignment. I have seen air guns used to tension a belt so tight that the belt would not defect, even if you walked on it. And belt dressing, which was used a can at a time to try and stop the belt from squealing. All of these are not acceptable if you had planned on doing the job right. The first time.
What is Belt Misalignment?
The number one reason why belts fail prematurely is heat. Heat dries the belt out which leads to cracking and slippage and the end is not far off after that. The heat is from friction caused by misalignment. To correct misalignment, we must correct the offset and angle errors in both the Horizontal and Vertical planes.
The first belt shows angular misalignment in the horizontal plane (toe-out and toe-in). The second belt shows parallel (offset) misalignment in the horizontal and vertical planes. The third belt shows a combination of angular and parallel (offset) misalignment in both planes. This is what we are normally trying to correct.
One of the reasons why it is difficult to correct this misalignment is because you are constantly correcting the alignment as you tension the belt. If you have ever worked with an adjustable motor base that has one central adjusting bolt allowing the motor to pivot as you tighten it, it is a challenge, to say the least. These bases are lightweight, flexible, and cheap. The inexpensiveness is why they are used but there is a hidden cost. You do a lot more maintenance work with this type of base so there is no saving. The frustration comes from the fact that you are unaware the bases are flexing until it’s too late. This is because it is not something you can see by eye when using a straightedge to align the sheaves. You still must compensate or adjust the alignment as you tension the belt.
Download our 5-Step Sheave Pulley Alignment Procedure which provides a simple and effective procedure for sheave pulley alignment of belt-driven equipment.
Thank you John Lambert with Benchmark PDM for sharing this educational article with us!
Related Blog: The Importance of Belt Alignment
by Diana Pereda