With training funds being difficult to obtain these days it is critical that we do everything possible to have a satisfactory and productive training experience. This includes evaluating whether it would be more cost-effective to attend a training class off-site (such as at a vendor’s facility) or have the course conducted at your facility.
There are advantages and disadvantages to both. Typically, if multiple personnel from your facility will be attending it could be more cost-effective to have the course presented in-house at your facility. This would eliminate travel costs, per diems, etc. for your personnel. If only one or two individuals are attending, then it might be more cost-effective to attend the course off-site at the vendor’s training center. Also, attending a course off-site may remove you from the internal distractions and interruptions that occur from being in the plant environment during the training course. When you decide to attend a training course you have the right to expect that the course will be presented in a professional manner by an instructor who knows the material and subject matter.
by Gary James CRL
When you or your supervisor are planning attendance at a training course there is an important consideration to keep in mind. Have you met the prerequisites for the course you have selected? These prerequisites are dictated by the company presenting the course and take into account basic knowledge about the subject as well as exposure to the subject. If you do not have the prerequisites this can make the learning objective difficult at best. Across most industries, timelines for taking most courses are determined by how attendees do based on their knowledge level.
In the vibration world, it helps if the student understands the terms of the subject and has had at least some exposure to the subject. When attending a vibration hardware course it is good to have had some hands-on experience, as those students tend to ask more questions and therefore get more out of the class.
If attending a software course, having at least basic computer skills is helpful. Remember, if you’re a novice there may be attendees far more advanced than yourself in the class, but if you’re more of an advanced user you may have attendees with far less experience than yourself. Courses are seldom taught for either the novice or advanced user. The material presented is in the middle of the class average. That does not mean that you should not attend the training class. Only that you make sure the course instructor knows your experience level. A good instructor should at the start of the course have an introductory period where you’re allowed to introduce yourself and convey your experience level.
Remember that everyone in a class started at some point with no experience or knowledge.
Maximizing Opportunities to Improve Equipment Reliability. Education vs. Training.
by Gary James CRL
At the onset of any program we should be more interested in education than in training. Training involves learning how to perform a task, while education means understanding the why or importance of the task. While both are necessary for a successful program, education will yield a stronger, more involved team. Unfortunately, many companies focus too much on the initial “button pushing” aspects when introducing a new technology.
Education encourages workers to become more invested in the tasks and success of the reliability program. It can transform the group into game changers in the area of reliability and cause them to question what is currently occurring within the program, to recognize opportunities and strive to improve.
While education is vital, it comes with great responsibility. Leaders of reliability programs should expect their employees to return from a reliability course with a better idea of how condition monitoring can effectively increase equipment reliability and be willing to provide the required support to take full advantage of the education gained.
Is there a difference between education and training? You bet!
How quickly the reliability programs succeed is highly dependent on the initial foundations that are set for it.
Take your Alignment, Condition Monitoring and Ultrasound programs to the next level!
Let LUDECA field experienced instructors and Certified Reliability Leaders (CRL) coach and train you in the fundamentals and skills you need to utilize your tools to the fullest and implement the benefits of precision maintenance in your facility.
by Ana Maria Delgado, CRL
Reposted from People and Processes, written by Jeff Shiver CMRP, CPMM, CRL
Do you find yourself wondering why your employees haven’t taken the initiative and approached you for additional training? Well, they must not want the extra training, right? Wrong! Sometimes, employees do want training, but they just don’t ask. Here’s why:
1. THEY HAVE FEAR OF REJECTION
People don’t like to be told no! The majority of employees don’t understand the organization’s vision, goals, brand promise, or key initiatives.
2. THEY FEEL UNSUPPORTED
Employees get worn out from a culture of mediocrity being tolerated, commitments not honored, and requests being ignored.
3. THEY DON’T KNOW HOW TO ASK
Operators, Mechanics, Planners, and even Managers may not understand how to equate the returns of training.
4. THEY DON’T KNOW WHEN TO ASK
Many employees don’t know when there is flexibility within the budget.
5. THEY ARE AFRAID OF BEING NEEDY
If no one else is asking for training, then why should they expect to be treated differently?
6. THEY FEEL AWKWARD OR UNCOMFORTABLE
There must be a commitment for development and the line of communication should be open.
7. THEY DON’T FEEL CHALLENGED
They may be topped out and let with nowhere to go from a promotional perspective.
8. THEY DON’T KNOW WHAT THEY DON’T KNOW
When people have never been exposed to anything else, they don’t know what else is possible.
Keep these things in mind the next time you offer training, or feel that your employees should ask you if they want it. A better approach may be discussing this with your employees individually.
Check out LUDECA training offering for alignment, geometric measurements, vibration analysis, balancing and ultrasound.
by Ana Maria Delgado, CRL
Reposted from People and Processes, written by Jeff Shiver CMRP, CPMM, CRL
The CMRT exam is the leading credentialing program by the Society for Maintenance & Reliability Professionals (SMRP) for the knowledge, skills, and abilities of maintenance and reliability technicians.
The CMRT exam tests competency and knowledge of specific tasks within 4 domains: Maintenance Practices, Preventative and Predictive Maintenance, Troubleshooting and Analysis, and Corrective Maintenance.
And that’s all well and good! But, why should you have your technicians certified? What are the benefits of having them pass the CMRT?
Here are 5 reasons why you should have your technicians certified:
- Validates the individual’s knowledge of maintenance and reliability best practices within the 4 domains.
- Confirms your commitment to advancing your team’s professional development.
- A globally recognized certification provides a personal level of satisfaction and pride in accomplishment.
- Encourages people to move beyond the status quo and achieve more for the organization.
- Determines strengths and opportunities by subject area to provide a development plan roadmap.
Get certified today! Click here to learn more about the CMRT certification.
Learn about People and Processes’ Maintenance and Reliability Technician Core Concepts Course
by Yolanda Lopez
Guest Post by Bob Dunn from I&E Central, Inc.
I had the opportunity to use the Easy-Laser XT440 to assist a customer in aligning a machine that had perpetually given them problems, with bearings always running hot. They had recently aligned the machine with dial indicators, but when we checked, it was off by .007, and this was on a 3600 RPM motor. We removed their old shims and did a soft foot check indicating .032 under one of the feet. Further inspection showed an angular gap under one foot. It turns out that when new, someone had ground down the feet on the motor to better align to the pump – obviously not a precision job. We step-shimmed to fill the angular gap, then aligned the machine in a single move. Several of the techniques we used were unfamiliar to these mechanics.
Takeaways:
- Do your pre-alignment homework to detect and correct foundation issues.
- Be sure mechanics are really trained in alignment – not just how to push the buttons. By the way, Ludeca Inc. and I&E Central provide excellent training.
- The Easy-Laser XT-Series is a fast, accurate, and incredibly easy-to-use tool for coupling alignment and more. If you use something else, you should see what you are missing!
by Ana Maria Delgado, CRL
There are many tools considered “accurate”. Dial test indicator can measure to the ten-thousandths and gauge blocks can be certified for even tighter tolerances. Even CNC machines can reach ten-thousandth’s accuracy given the right conditions. However, they are tools and they can’t perform to their maximum potential if not used properly or in the right application.
Laser shaft alignment tools follow the same rules. The sensors by themselves have varying degrees of accuracy but how the sensors are used and what application they are used for can vary this accuracy quite a bit. When searching for a “laser alignment system”, don’t be quick to commoditize the term and think all systems are the same just because it uses a “laser”. The most capable systems will work for their intended primary application— general shaft alignment. Should a specialized application arrive, such as an uncoupled spacer shaft with limited rotation, a system that has more functionality will be able to immediately handle the job over a basic system.
LUDECA can assist you in your decision. We provide a network of local solutions providers who are your highly experienced advisors for navigating all of the choices that a quick internet search can provide. They will make sure you know you are getting the right tool for your needs whatever your budget. We also have a team of engineers that will guide you in your applications. All this is provided for free! This is something to consider when purchasing on price alone. We will be there when you need us the most.
So let’s go back to the dial indicators, gauge blocks, and the CNC machine – they are not accurate in use without a trained operator. The same principle applies to laser shaft alignment. Most of our laser shaft alignment systems currently have 1-day free training on-site at your facility by your local solutions provider. Our laser shaft alignment tool is designed to improve your reliability and thereby reduce downtime. Avoid costly mistakes and wasted time by ensuring your operators are well trained to use these tools to their maximum potential.
by Daus Studenberg CRL
Can a Reliability Engineer or Reliability Manager make a facility or organization reliable? This is a very important question that may be worth discussing within your organization to ensure proper expectations and success.
A more practical definition of reliability may be:
Equipment performs the way you want it to when you want it to”.
Reliability is very easy to define, stuff but achievement of this simple goal is complex and unfortunately unattainable for many organizations. Reliability requires a holistic approach that involves the complex interaction of Maintenance, see Operations, Supply Chain, Engineering, Procurement, Management, Process, and Vendors. Consistency, focus, and strategic implementation directly correlate to the success of any effort and this is true for your reliability efforts. Therefore, a consistent and strategic top-down focus is required from management and throughout each of these groups. Organizational misalignment leads to competing groups and will make sustainable reliability within your organization extremely difficult, and maybe even impossible to achieve.
Reliability Engineers and Managers can support reliability through leadership, training, tools, etc. However, the answer to the question is that everyone within your organization is responsible for reliability. It is critical that everyone within an organization understands this and that reliability is made a goal for each of these groups with defined metrics to track understanding and achievement.
So, who owns equipment reliability in your plant? The answer is Everyone!
by Trent Phillips CRL CMRP - Novelis
The Mars Climate Orbiter was launched by NASA on Dec 11, 1998, to study the Martian climate. On its arrival at Mars on September 23, 1999, communication was lost shortly after an orbital insertion maneuver was performed.
The cause of the failure was a lower than anticipated altitude with a resulting burn-up of the orbiter. It was entirely due to human error. The error occurred because one piece of software entered the required force in pounds and a separate piece of software interpreted this as newtons. The result was a $125 million dollar lesson on the importance of consistency in units.
When performing an alignment, consistency with measurement units is the key to preventing costly errors. We recently conducted a training class for a company that worked on the metric system. Our alignment systems allow for easy conversion “on the fly” between imperial and metric units, so we simply operated everything in the metric system. We then started noticing that some students were taking much longer times on their alignments than usual. It became apparent they were misinterpreting the values of the shims, which are expressed in “thou” and thought they represented some form of a metric value. Fortunately, it was not a $125 million mistake as this can simply be a lesson to be learned in training.
When working with different units, consider all of the stakeholders involved in the project. Who will operate the tool? Who will make corrections? Who will interpret whether or not the alignment is acceptable? You will have to determine which units of measurement will be the standard for the entire project. Fortunately, if someone makes a mistake with units for corrections, they will most likely not see the alignment improving. However, if there is a mistake on units for acceptability criteria, this could be dangerous. There is a big difference between 1 mm and 1 thou! Avoid multiple conversions for the alignment process. Standardize on one set of units and remain consistent for the whole project. If there is a need to convert units during the alignment, make very sure everyone understands when this happens and why this is the case.
by Daus Studenberg CRL
The need for bore alignment applies across a wide variety of industrial sectors including the marine industry, energy, oil and gas, chemical, and service companies. It is used to determine the centerline of a series of bores and setting the centerline relative to any fixed reference, or aligning the bores to a rotating shaft, and/or determining the out-of-roundness of bores. One common example is the alignment of large gas and steam turbines.
However, one problem often encountered with performing laser alignment on large turbines is that over long distances and long measurement periods, laser stability is subject to be impacted by variations in air density, temperature, or light, the cumulative effect of which is often referred to as “laser drift”. To ensure measurement accuracy, an additional fixed sensor, called a control sensor, can be installed to monitor the amount of laser drift at the far end of the turbine. When used with the CENTRALIGN® ULTRA EXPERT application, the laser drift data from the control sensor is automatically applied to the bore measurements taken by the measurement sensor to provide true bore center measurements under any conditions over longer periods of time.
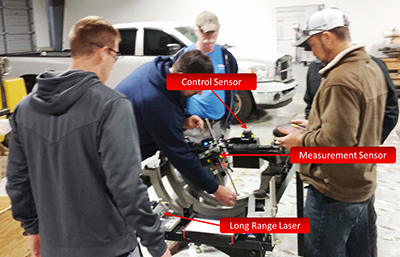
by Tim Rogers CRL
LUDECA Inc. has been recognized by the Society for Maintenance and Reliability Professionals (SMRP) as an approved provider of continuing education and training aligned with key subject areas related to reliability and physical asset management.” said Ron Leonard, SMRP CMRP Chair of APEP Committee
As an SMRP Approved Provider, LUDECA is recognized for its best-in-class continuing education training programs for precision shaft alignment of rotating equipment and precision balancing as part of reliability and physical asset management. LUDECA is a Tier 2 Approved Provider with courses that are taught on-site, regionally, or at their own state-of-the-art training center in Doral, FL.
The following are currently approved courses that map to SMRP’s Body of Knowledge Pillar #3 – Equipment Reliability:
- 3-day Advanced Shaft Alignment Course (21 hours)
- 4-day Comprehensive Shaft Alignment Course (28 hours)
- 3-day Balancing Course (21 hours)
We are thrilled to be part of this select group of training companies.” says Ana Maria Delgado, CRL, Marketing Manager for LUDECA. “Our company has always made it a priority to deliver quality hands-on training with alignment and balancing best practices to improve asset reliability. Our new SMRP Approved Provider status provides us with the opportunity to enhance our commitment to our customers and to the success of their reliability programs.”
About LUDECA
LUDECA is a leading provider of Preventive, Predictive, and Corrective Maintenance Solutions, including machinery laser alignment, vibration analysis, and balancing equipment as well as software, rentals, services, and training. For more details, visit www.ludeca.com
About SMRP
The Society for Maintenance & Reliability Professionals (SMRP) is an international, nonprofit society dedicated to promoting excellence in maintenance, reliability, and physical asset management. Its 4,000 members specialize in achieving improved efficiency and profitability across many industries by applying best practices and proactively managing operations, equipment, and people. SMRP provides ANSI-accredited professional certification to validate the critical knowledge and skills of the top practitioners in the profession. For more information, visit www.smrp.org.
by Ana Maria Delgado, CRL
One of the top priorities of any military organization is keeping soldiers fit for deployment upon demand. This usually involves exercises to maintain and increase job skills, physical abilities, overall health, and mental capabilities. Troops are encouraged and required to participate in activities that achieve these readiness goals.
Why should your organization and position be any different? What are you and your organization doing to ensure fitness for job deployment each day? Are your employees trained to function like F Troop or Seal Team Six?
Download my entire UPTIME MAGAZINE article: Is your Company Fit for Deployment?
by Trent Phillips CRL CMRP - Novelis
It has been said that if you think education is expensive, try ignorance. The high cost of ignorance can affect all aspects of life. In industry, this includes maintenance, machine reliability, safety, and lost production.
Unexploited opportunity is lost opportunity—a costly consequence of ignorance.
The financial impact suffered from unplanned/unscheduled maintenance can be huge. You should strive to make the investment to properly educate and train your group so they become empowered to drive change, improve equipment reliability, reduce costs and improve MTBF. Education can transform the group into game-changers in the area of reliability and cause them to question everything that is currently occurring within the program, recognize the opportunities and strive to improve.
by Pete Oviedo Jr
Guest post by Jessica Dieken, Director of Marketing and Sales at Pioneer Engineering
Employees are among the most important investments an organization makes. Investing in the right people for the job is crucial to the long-term profitability of a company. It costs time and money to hire and train new employees. That is why the hiring process takes time; it is important to make sure that the person being hired has the right skills, the right personality, and the desire to be with the organization in the long run.
But keeping employees is just as important as hiring the right ones. Making sure that employees are happy and productive is an ongoing process. When starting a new job, most of us have had the opportunity to undergo some kind of training – whether it is to learn how a plant works, why safety is important, or a simple welcome orientation. These types of employer-based development opportunities are important to how hard employees work and how long they want to stay with a company.
By training and developing employees, you are empowering them, helping and encouraging them to grow. Research has shown that there are many benefits an organization, both large and small, experiences when employees receive training and development opportunities, including:
- Increased productivity and improved performance
- Decreased employee turnover
- Decreased need for supervision
- Increased efficiency
That’s not all. Well-trained employees also tend to have better self-esteem, and increased self-worth, and become a valuable asset to the organization.
International corporations, like IBM and Motorola, are strong advocates for ongoing employee training. They believe that by investing in their employees, long-term financial gains will be seen. In a whitepaper published by IBM (IBM Training White Paper, 2008), the long-term benefits of employee training were explored. IBM discovered that:
- According to the American Society for Training and Development, 41% of employees at companies with inadequate training programs plan to leave within a year versus 12% of employees at companies who provide excellent training and professional development programs.
- The cost of replacing skilled employees ranges from US$75,000 to $450,000.
- The average cost to recruit a professional candidate is $18,374.
- Companies in the top quarter in training expenditure per employee per year ($1,500 or more) average 24% higher profit margins than companies that spend less per year.
- According to a Merrill Lynch study, Motorola estimated that every dollar spent on training yielded US$30 in productivity gains within three years.
- A company with 1,000 employees can save at least $240,000 per year as a result of an average productivity gain of just three minutes per day.
By training and developing your employees, you are taking steps to reduce employee turnover, and saving them time and money it takes to hire and train a new person. It is impressive to see how much training your employees can do for your company – while the initial cost for training and development may, at first, seem high, it is important to focus on the long-term return on this investment.
Benjamin Franklin once said, “An investment in education always pays the highest returns.” For companies big and small, the question is not how can you afford to train your employees, but rather, can you afford not to?
by Ana Maria Delgado, CRL
When you are planning on attending a training course there are a few things you as a student should do. These could include some simple things such as:
1. When making hotel arrangements, consult with the person/company providing the training and ask for a list of recommended hotels. They may negotiate special rates with certain hotels or they may know the hotels that are the most convenient to the location.
2. Always ask for and review the training agenda/syllabus.
3. Allow extra space in your luggage to carry back the training materials you will be given during class.
4. Ask questions during the course (there are no “dumb” questions). If you don’t understand something ask —there is always a first time to learn anything. Not understanding something and not asking hurts only you.
5. If possible use the software and/or instrument prior to the class as this can help you formulate productive questions and you will gain much more from the course.
6. Remember that if you’re not rested you will not get the full benefit of the course —do not let your nighttime enjoyment compromise your ability to focus on the training material each day.
7. If you’re unhappy with something in the class tell the instructor either during class or on a break. The instructor wants you to have a productive training experience. The instructor cannot help you if you do not make your questions or concerns known. Remember, courses should be targeted to the average experience in the class and not for the most advanced participant or for the novice either.
Check to see if your equipment needs any calibration or repairs prior to attending the class. Make arrangements to have these repairs or calibration completed while you are attending the training course. This is the perfect time to have these types of things completed.
by Gary James CRL
We have a strong focus on our predictive maintenance training program of which laser shaft alignment and vibration monitoring play a very important part for us and all the local manufacturing businesses that we serve. Using LUDECA’s support and more intuitive tools like the SHAFTALIGN® and the VIBXPERT® we find that we can better prepare our students in ways that we could not accomplish before. Our purpose here is to prepare our students for all of the new challenges in the predictive maintenance field and LUDECA helps us accomplish our goal.” —Bert H, Central Carolina Tech
by Ana Maria Delgado, CRL
Are others in your plant or corporation aware of the capabilities of the Condition Monitoring (CM) technology you utilize and all that you do with it? It is critical that management, maintenance employees, and production employees are aware of what you do and the value CM technologies provide. This will make them much more responsive to your needs and efforts and make your job much easier as a result.
Consider taking a maintenance or production employee along when you do data collection and show them how you use this information for analysis of equipment problems. Hold level of awareness meetings and invite plant management and employees to attend. This will allow you to expose them to the capabilities that you and the CM technologies offer. The goal is not to turn them into analysts, but to help them better understand the value of CM efforts.
by Trent Phillips
As Published by BIC Magazine May 2013 issue
A relatively small investment in training is a win-win scenario for the plant with a huge return
LUDECA has trained its customers’ maintenance personnel for more than 25 years. The incidence of mistreated laser alignment systems coming back for repair drops dramatically when a plant’s millwrights are properly trained in the use and care of the system. A relatively small investment in training is a win-win scenario for the plant with a huge return.
Many plants cognizant of the benefits of good training invest in a separate fully funded training department with highly qualified instructors. If you do not have this, do not hesitate to hire outside experts to come in and train your personnel, but ensure these experts really are qualified to train. Research credentials and follow-up on references.
Buy the best systems you can afford and really train your people to use them, or your equipment will be underutilized or mishandled. A well-equipped, dedicated training center provides a controlled environment where employees can learn undisturbed to their maximum potential. Equip it with good lighting, sanitary facilities, quality tables, comfortable chairs, a generous coffee pot, the latest SMARTboard™ technology, projectors, computers, and Internet access.
If you cannot provide a good training environment in-house, send employees away for training. Vendors who offer such services should have better facilities for this than you do. Ensure they do! We went out of our way to build and equip our own state-of-the-art training center and staff it with highly qualified people.
If you cannot afford to send away several employees at a time, send your most qualified employee or resident instructor for more in-depth training to have the knowledge brought back. We offer intensive “train the trainer” courses and in-depth courses for day-to-day users of our alignment and vibration systems. For us, it is a win-win proposition — well-trained users of our systems learn to love them, use them correctly and care for them properly. We offer an educational discount for systems purchased by training programs or educational institutions.
Six students per class is ideal (eight max) to allow the instructor to devote individual attention to each student, answer all questions and ensure each student gets hands-on practice. Each pair of students is assigned their own training simulator and complete laser shaft alignment system or vibration data collector and computer and necessary peripherals. Each student gets a complete set of training materials and an operator’s handbook for the system being learned to keep.
Vibration training is regarded as complex, and it can be at the more advanced levels. Yet a solid understanding of the basics of machine vibration and its underlying causes will benefit you greatly. Maintenance employees will be more attuned to spotting potential problems than they otherwise might and become more valuable, proactive members of your overall reliability program. Understanding what causes imbalance and its consequences, and what causes a bearing to fail prematurely is valuable knowledge for your employees, saving you money in the long run.
by Alan Luedeking CRL CMRP
“If you think the cost of training is high, try calculating the cost of ignorance.”
“What if we train them and they leave?”
“What if we don’t train them and they stay?”
“Training ain’t learning.”
When we see a magician pull off his head and stick it under his arm we are amazed; but when we know how the trick is performed, it becomes unimpressive. Technologies sometimes have the same effect on us. To see someone measure vibration on a machine and then be able to state that the inner race of a bearing has a flaw can be almost as amazing as a magician’s trick. It shouldn’t be, because all the stakeholders in machine reliability should be sufficiently trained to know how these “tricks” are performed. If stakeholders understand the basics of the technologies involved in maintaining machinery, the proper maintenance strategies are more likely to be developed. Many years spent in maintenance training reveals a most important concept: Frequently trainees have expressed a desire to have their supervisors present for the training. Unfortunately, they return to the job with high expectations of improving machine reliability only to discover that their bosses aren’t as thrilled about making the needed changes learned in the recent training. The saying, “We don’t know what we don’t know” comes to mind. Without training all the stakeholders, the full importance of what was learned by some is not understood by all. Consequently, the full value of the training goes unrealized. It is imperative that all stakeholders know the basics of the technologies used if the strategy is to be implemented successfully.
On-the-job training is a wonderful way to learn most jobs and should be part of the training in all jobs. Today’s predictive maintenance technologies are more complex and require more precision in order to be competitive in a world where machine reliability is a must for plant success. This new precision requires more than OJT because there may be some basic knowledge that OJT doesn’t address. Sometimes OJT teaches us to take shortcuts that may, in the long run, be harmful to machine reliability. OJT alone is not usually adequate in teaching the philosophy required for successfully maintaining machinery. Formal classroom training is the best way to learn the principles and standards required in order to keep machines running at peak performance. Proven, researched-based training provides adequate hands-on learning, as well as basic principles that apply across all technologies. These basic principles and standards embody the philosophy of successful machine management.
The author remembers teaching an electrical class where one of the participants declared, “Microfarads, picofarads… we don’t need all that theory stuff, we just need to know how to fix it.” What the student failed to realize was that “fixing it” is simply the application of theory. The application of any technology is putting theory to use, and theory is best learned in the formal classroom. A person with OJT can eventually learn to be an electrician on a specific job; but when that person is moved to a new location, he/she must learn the new job. Whereas, a person well-trained in theory can be a good electrician regardless of where he/she is placed, once the individual learns the locations of the equipment.
Today’s training must provide a thorough understanding of the theories of technology if we are to be successful tomorrow. Technology has provided improved learning opportunities surpassing what was available in the past. Computers allow us to simulate scenarios that may be too expensive or time-consuming to develop with physical components. This provides us with a greater learning advantage than was available in the past. Computers also allow us to easily individualize training for our particular needs and situations.
The knowledge base in all predictive maintenance technologies grows daily along with the data we collect on our machines. We will continue to find new parameters to measure as we improve our ability to keep our machines running. We can expect this trend to continue in the future because we can foresee a day when small devices will let us collect and share data with huge, smart data banks, making use of the collective knowledge in all maintenance fields. The new tools and technologies will always require a solid basic knowledge, well-grounded in theory, learned in the classroom. Data becomes meaningless if we don’t have the knowledge to sort and interpret what is needed in order to keep our machines reliable. The knowledge base will continue to grow, so we must continue to learn.
“The only true competitive advantage is the ability to learn faster than the competition.”
by Bill Hillman CMRP
March 2010 · Plant Services Magazine
During these tough times, industries attempt to cut all costs deemed not absolutely necessary for the day-to-day operation of the plant. Many times training budgets are among the first costs to be curtailed. This usually happens because the true value of training may not be fully understood, and training may not be seen as critical to company growth and profits.
by Ana Maria Delgado, CRL