In Are Harmonics Real? Part 1, I noted that a sine wave, perhaps created by a mass on a spring bouncing up and down, results in a single peak in the spectrum. If the spring gets more rigid as it gets compressed, the mass will move less in one direction than the other. We can describe the form of the wave this makes as distorted or clipped. When we pass this clipped wave through the FFT, we get harmonics or multiples of the fundamental frequency.

For example, if the mass bounced up and down 30 times per second, we would see a peak in the spectrum at 30 Hz. If it was clipped, we would also see peaks at 60, 90, 120 and 150 Hz etc. These are called harmonics. The question I posed is: Are the harmonics real? In other words, although the mass is still only bouncing up and down 30 times per second, is there actually real vibration occurring at 60, 90 and 120 Hz Etc? OR are these just artifacts of the FFT?
I posted this question to LinkedIn. Here are the responses:

Apparently, 65% of the respondents believe that harmonics are NOT real, but just a product of the FFT. Only 21% think harmonics are real. Perhaps popular opinion is not a good gauge of truth?
Natural Frequencies and Resonance
I am going to go off on a little tangent to talk about natural frequencies and resonance. In this tangent, I will propose an experiment that people can try themselves to prove if harmonics are real or not.
A single mass spring system has a single natural frequency. If you pull the mass down and let it go, it will vibrate at this frequency. A tuning fork is the same. It has one primary frequency it likes to vibrate at. A bell has numerous natural frequencies, but they also won’t ring if they are not excited by the same frequency.
A natural frequency is a property of the structure, related to its mass, stiffness and damping. Resonance is a condition where the natural frequency is excited by a forcing frequency. In the case of a tuning fork, it has a natural frequency, BUT if it is just sitting on a table, that natural frequency is not excited (it is not in resonance) and the tuning fork does not make a sound. If you shake it back and forth in your hand – Eg. vibrate it at a frequency other than its natural frequency, it also doesn’t make a sound. It only makes a sound when the natural frequency is excited.

This concept is very straight forward in vibration. I am not sure why the LinkedIn community got this wrong. If the natural frequency is NOT excited, the bell WILL NOT ring. On a positive note, I know where people can get some great vibration training! Y’all need it! 😉
A Single Impact
In Are Harmonics Real? Part 1, I noted that a single impact in time creates broadband noise in the spectrum. The FFT basically says: “Give me a wave and I’ll give you a bunch of sine waves. If you add these sine waves together, they will look like the original wave.” People who don’t think harmonics are “real” might say that they just come from the FFT trying to define the shape of the wave by adding sine waves together.
If you have a single impact in time, it looks nothing like a sine wave at all and the FFT spits out sine waves at lots of frequencies to try to define it. We call this broadband noise. People who believe that harmonics are not real will also believe the broadband noise is not real for the same reasons.
A single hit creates noise in the spectrum
Looking at the animation above. I am only tapping the structure once, but you see vibration all the way across the spectrum. There’s a hump just above 100 Hz, but I am not tapping anything 100 times per second. Therefore, this vibration must not be real. Right? I am also not tapping it 300 times per second and yet the spectrum shows vibration at that frequency (and all the frequencies between) as well.
I am asking the same question here. Is the broadband noise “real” or just an artifact of the FFT?
An Easy Experiment
I am using the example of broadband noise to make the case for harmonics being real because this one is more intuitive and easier to test. If you think harmonics are NOT real, you will also think broadband noise is NOT real for the same reasons. I am clearly only tapping the object once, not 100 times per second or 300 times per second or anywhere in between, so these frequencies must not be real… That’s how the thinking would go.
So, let’s say a bell or a tuning fork has a natural frequency of 1000 Hz. If you hit it once, does it ring at that frequency? Yes it does! That means that there really is vibration at 1000 Hz being input into the bell. That single tap does include real vibration at 1000 Hz. It is NOT just the FFT trying to come up with a bunch of sine waves that when added together will look like our input.
You could also prove that different “taps” include different frequencies, even if the tap itself only happens once. A drum head has a lot of natural frequencies – none of which will make a sound if it is not excited by the same frequency. If you hit a drum with a soft mallet, it makes a different sound than if you hit is with a wooden drum stick. Why is this? It is because the soft mallet only injects (or contains) lower frequencies and therefore only excites the lower modes or natural frequencies of the drum head. It makes a lower sound. A wooden drum stick injects lower and higher frequencies, so in addition to the low tones, you also get higher ones.
An Easy Experiment for Harmonics
With the last experiment in mind, we can prove the existence of harmonics in the same way. Let’s say we have the mass and spring bouncing up and down 30 times per second (30 Hz) but the wave is clipped due to the spring getting more rigid as it compresses. The FFT will contain 30 Hz and harmonics at 60, 90, 120 Hz etc.
To prove that the harmonics are “real,” we could attach another spring with a natural frequency of 60 Hz to the first spring. If the spring tuned to 60 Hz vibrates, it means there is in fact really vibration at 60 Hz, it is not an artifact or output of the FFT.
In the case of a machine, if it rotates at 1800 RPM (30 Hz) you could mount a spring on it with natural frequency of 60 Hz. If the spring vibrates, then there really is vibration occurring at this frequency.
Back in the old days (before my time) they had mechanical vibration sensors that were just a series of little masses on springs tuned to different frequencies. You placed it on a machine and looked to see which springs vibrated. This is how you knew which frequencies were present.
Non Linearity
Why are there frequencies in the output that do not exist in the input? If I bounce the mass on the spring up and down at 30 Hz, why do I also get frequencies at 60, 90, 120 Hz Etc? The answer is non-linearity. In a non linear system you get things in the output that were not present in the input. You can read more about that in my article below, Linear and Non-linear Vibrations.
Another Example of Harmonics that Real in a Different Way
In article 3, I’ll offer up a couple of cases where natural frequencies are also harmonics. Keep an eye out for it!
WANT TO LEARN MORE?
Alan Friedman dba Zenco offers machinery vibration analysis courses and certification in accordance with ISO 18436-2. Click here to check out his course schedule, you can also connect with him on Linkedin. In addition to public classroom training and public virtual courses, Alan is also available for private courses virtually or on-site in addition to informal training and mentoring. Category I and II vibration are also available in Spanish.
Alan, aka the Vibe Guru, has over 30 years of vibration analysis experience, He has trained thousands of students around the world up to Category IV. One of the things that makes Alan a great teacher is his ability to teach people where they are at. Whether you are a math-challenged millwright, an engineer, or a PhD, Alan will challenge you without overwhelming you. If you are interested in condition monitoring you can also check out his book: Audit It. Improve It! Getting the Most from your Vibration Monitoring Program or hire him for an on-site program audit.
by Diana Pereda
Are harmonics real or just an artifact or result of processing the waveform through the FFT? This is a question that comes up a lot among vibration analysts, or anyone working with signals and signal processing.
What Are Harmonics?
A sine wave has a single amplitude and frequency. Let’s say our sine wave has a frequency of 25 Hz and a peak amplitude of 10. If you use the FFT algorithm to convert a sine wave to a spectrum, you will see a single peak at 25 Hz with a peak amplitude of 10. You can see this at the beginning of the animation above. At the starting point there is a sine wave at the top and the spectrum below with a single peak at 25 Hz.
A wave that repeats itself but is not a sine wave results in harmonics in the spectrum. You can also see this in the animation above. As I clip or flatten the top of the wave, you can see the harmonics appearing in the spectrum. Harmonics are multiples of the base frequency. In this case they are 25 Hz x 2, 25 x 3, 25 x 4 etc. giving us peaks at 25 Hz, 50 Hz, 75 Hz, 100 Hz etc.
The Fast Fourier Transform (FFT)
The FFT is a tool that reveals the frequency components present in a signal. It breaks the signal down into a series of sine waves.
Another way of phrasing this is: The FFT essentially says “give me a wave and I will give you a bunch of sine waves. If you add all these sine waves together, it will look like the initial wave.” This is my layman’s way of understanding it anyway.
Each peak in the spectrum represents a sine wave. If I were to add the sine waves represented by the peaks at 25, 50, 75 and 100 Hz etc. at the end of the animation above, the resulting wave would look just like the clipped wave.
But Are Harmonics Real?
One view of this is that the wave I used for this explanation is not “real” in that it is something I generated in software. I also clipped it in software, so the peaks at 50, 75 and 100 Hz don’t correspond to anything real in the physical world, so they must just be artifacts or things stemming from running the data through the FFT. Right?
A Physical Representation of Clipping
Let’s say I move a mass and spring back and forth 30 times per second (30 Hz) with a sinusoidal force (a sine wave) but as the spring compresses, it gets more rigid and eventually stops compressing. This will create a clipped wave as in the image below. When I pull the mass out, it looks like a sine wave, when I push it in, compressing the spring, it gets flattened.
As we noted before, the clipped wave is repetitive but not a sine wave and therefore we will get harmonics. As you can see from the image above, we have peaks at 30, 60, 90 and 120 Hz.
One might look at this physical example of a clipped wave and they might say: “I see the mass moving back and forth 30 times / second. I do not see anything happening at 60 times per second or at 90 times per second, so harmonics can’t be real. They must just come out of the FFT algorithm.”
Repetitive Impacting
Another example of a wave that is repetitive but not a sine wave is repetitive impacts. If I take a drumstick and I hit a drum 5 times per second (as in the time waveform image below) I would see peaks in the spectrum at 5, 10, 15, 20 Hz etc. In other words, harmonics. Intuitively you know that you are only hitting the drum 5 times per second, so why would there be frequencies at 10, 15 and 20 Hz etc. in the spectrum? They must just come out of the FFT right?
The pattern above is common in machinery vibration analysis. This could be a bearing with a defect on the race and the impacts are the balls or rollers slamming into that defect one after the other. This could also a be a broken gear tooth that causes a big impact every time it comes into contact with the other gear. In both cases, the analyst would expect to see harmonics of the defect frequency in the spectrum.
A Single Impulse or Impact?
A common test in vibration analysis is to strike an object with a calibrated hammer. The calibrated hammer has a force sensor in its tip, so it measures the actual hit. If we look at this in the time waveform, we see a single sharp, short duration pulse. When we convert this pulse to a spectrum, we get vibration at many frequencies or what is referred to as “broadband” noise.
One might say: “The FFT has a really hard time describing that single impact by adding sine waves together. The only way to do it is to add sine waves together at every frequency as shown in the image above.” These frequencies don’t exist in the real world though. (Or do they?)
I will ask again, using this example, are the frequencies shown in the spectrum for this single impact “real?” Do they really exist? Or are they just a result of passing that data through the FFT and the FFT trying to describe it by adding sine waves together?
Conclusion to Part 1
I want to leave this as an open question for now. Take some time, think about it, and decide for yourself if you think harmonics (and broadband noise) are real or not. In upcoming articles, I will lay out a case for what I think. I will also admit that my thinking about this has changed over the years. I used to take one side of this issue, now I lean towards the other. But you can decide for yourself.
WANT TO LEARN MORE?
Alan Friedman dba Zenco offers machinery vibration analysis courses and certification in accordance with ISO 18436-2. Click here to check out his course schedule, you can also connect with him on Linkedin. In addition to public classroom training and public virtual courses, Alan is also available for private courses virtually or on-site in addition to informal training and mentoring. Category I and II vibration are also available in Spanish.
Alan, aka the Vibe Guru, has over 30 years of vibration analysis experience, He has trained thousands of students around the world up to Category IV. One of the things that makes Alan a great teacher is his ability to teach people where they are at. Whether you are a math-challenged millwright, an engineer, or a PhD, Alan will challenge you without overwhelming you. If you are interested in condition monitoring you can also check out his book: Audit It. Improve It! Getting the Most from your Vibration Monitoring Program or hire him for an on-site program audit.
by Diana Pereda
Recently, while visiting a customer’s facility to provide onsite training for the vibration analysis tool they had purchased, we spent time building the database hierarchy (areas, machines and trending templates) before we started collecting data. The first room we entered had two large belt-driven overhung fans and even without collecting any data it was obvious that one of the fans was running extremely rough. After collecting data off both of the fans we stopped to review the data. As some of you with experience might already have guessed, the fan that was vibrating excessively had an extremely high turning speed (1×) amplitude.
Immediately the comment was made by the technician that his diagnosis was that the fan needed to be balanced, and if you simply looked at the vibration data that was the correct diagnosis; however, if you looked around the room and at the fans themselves, they were screaming clues about the root cause of the unbalance.
This facility was involved in the manufacture and processing of wood products which results in large amounts of wood dust being produced. These fans were designed to ventilate a high dust area and everything inside the room was covered in wood dust. It only makes sense that if everything inside the room was covered in wood dust, how much had also accumulated on the inside of the fan?
Before we walked back to the maintenance shop and informed the maintenance manager that we had a fan that needed balancing, I asked the technician if the fan could be stopped for a short period so that the inspection door could be opened. Once the fan was stopped and properly locked out, we opened the inspection door and found the fan blades heaped with accumulated stuck-on wood particles. After we had cleaned the fan blades, we had pile of wood chips which probably weighed somewhere around 5 lbs. We closed the inspection door and removed the lockout and asked operations to start the fan. Once the fan had been operating for a few minutes, we recollected data and the 1× fan amplitude had dropped significantly to a level that the fan no longer required balancing.
While it’s true that sometimes fans require balancing, often the cause is much simpler. Foreign material can build up on the fan blades and then suddenly a large piece comes off one of the blades causing the imbalance. This situation is more common than you might think, so before conducting any balance job perform a close inspection.
Watch our Balancing Know-How: Diagnosing Unbalance video for a quick introduction to diagnosing machinery unbalance with vibration analysis!
by Diana Pereda
There is a very simple, but crucial step in the machine installation process that oftentimes gets missed. When this step is missed, it leads to a world of problems, from excessive vibration to premature failure of bearings, seals, and especially couplings.
Let me establish the problem first, then I will explain how it negatively impacts the machine.
The problem
If some types of couplings are tightened before alignment, they ultimately end up in a bind. This bound condition can also be referred to as a “preloaded” condition. When this happens, an undesirable axial and radial load is introduced into the machines even though the shafts are aligned within tolerances.
Be aware of this potential problem and remember that some couplings should not be tightened until the shaft alignment is completed.
What types of couplings are susceptible to this issue?
This issue only affects coupling that have elements that bolt the two hubs together. These couplings typically have pieces that bolt to the outer or radial face of each hub. Although there are certainly others, the main types of couplings that are extremely susceptible to this are Omegas, Raptors (New Omega), and Rubber Tire couplings.
Some couplings are less or not affected by this problem, depending on how bad the initial misalignment is when the couplings are tightened. These might include gear couplings, grid couplings, and insert-type couplings. Shim pack type couplings are flexible couplings that are particularly rigid and can be affected by preload. Leave the final torque for the end!
Summary
Omega, Raptor, Rubber Tire, and other types of couplings that bolt up, easily bind up if you move the machine after they are tightened.
Gears, grids and inserts move more freely when they are aligned. One main reason for this is that these couplings have the ability for the connecting component to freely move axially.
What does coupling preload look like?
Let’s say you are a technician that is called out to troubleshoot a major vibration issue on a brand-new fan that you did not install. Let’s also assume that the millwright that did the install, tightened an Omega coupling and then aligned the motor to the fan.
If vibration data is collected it is likely to indicate misalignment with elevated 1×, 2×, and sometimes 3× in the spectrum. When the time waveform is analyzed, it will likely indicate binding that looks like misalignment.
Sometimes this preload condition can produce only an elevated 1× which would seem to indicate unbalance. The problem with preloaded coupling issues is that a laser alignment may look completely fine, and a balance will be unsuccessful and unnecessary. The only solution is to remove the preload condition of the coupling.
How to remove coupling Preload
Here’s the easy part. This problem is extremely easy to correct and even easier to avoid. To correct, simply loosen the coupling and retighten. This should relieve the preloaded condition. It is always a good idea to collect vibration data before and after, to document the improvement.
To avoid the issue, when dealing with preload-prone couplings, bolt the pieces of the coupling together but leave them loose. We need the hubs to rotate together in most cases for laser alignment. Align the shafts to tolerances, then tighten the coupling. When this happens in the proper sequence, everything is happy.
Conclusion
Be aware of the potential for coupling preload to affect vibration readings and machine health and strive to avoid this conditions from occurring in the first place, using the guidelines described above.
Download our Misalignment & Vibration infographic a reference guide to misalignment condition.
by Diana Pereda
There are different ways to understand machinery vibration analysis that people often confuse. Is vibration the cause of the problem, the result of the problem, or both? If you confuse these, you might make some big mistakes when analyzing data! So, let’s clarify…
Vibration as the Cause
When things vibrate a lot or “too much,” it can cause a lot of problems. Excessive vibration causes fatigue failures. Shafts, couplings, bearings, seals, pipes, foundations, and any structure, can actually be damaged by excessive vibration.
Excessive vibration can also cause quality problems in our products. Imagine an HVAC fan vibrating next to a computer chip printing machine. The vibration can travel through the floor from the fan to the machine and screw up our chips. Vibration can harm humans as well and even when it doesn’t harm us, it can annoy us – just think of that unbalanced ceiling fan going “whop whop whop” while you are trying to sleep.
A metaphor I like to use is: Imagine you are driving your car really fast on a really bumpy road. If you keep driving like that, the vibration will damage your car.
When I audit people’s vibration programs and I watch how they analyze data, I often see them thinking about vibration in this way. They look at a graph, look at the highest peaks, and say to themselves “This vibration isn’t too high, the machine is OK.” Or perhaps they use ISO RMS alarm charts and compare the measured vibration to the chart. Now I will explain why this is a big mistake!
Vibration as an Effect
When we use vibration in the context of #ConditionBasedMaintenance #CBM we are frequently looking at vibration as the effect rather than the cause, going back to the car metaphor. Imagine you drive your car to work the same way every day and one day you notice a new sound. You conclude “There must be something wrong with my car!”
In this case, we are not saying that the new sound is damaging the car but rather the new noise is an EFFECT or result of the damage. It is also possible that the amplitude of that new noise might be quite low, even if the damage is serious.
In a piece of rotating equipment, consider a defect on the outer race of a rolling element bearing. The balls or rollers hit the defect as they roll over it is creating a repetitive clicking. The amplitude of the vibration caused by a ball or roller hitting this little defect on the race through a layer of grease is pretty small compared to the vibration caused by water flowing through a pump or even by the shaft rotating around – BUT – the bearing is in fact damaged – AND – if we are just looking at our vibration to see if there’s anything “High” then we might miss this important fault. This is one reason why it is NOT ok to just look at vibration in terms of absolute amplitudes.
Effect and Cause
There are some cases where the vibration is both the effect and the cause. For example, if a rotor is out of balance, the vibration amplitude will increase at the shaft rate frequency (1x). This is an indicator that the rotor is out of balance. Why do we care that the rotor is out of balance? Because the increase in vibration resulting from the unbalance can cause damage to the machine. This therefore is a case where vibration is both effect and cause.
WANT TO LEARN MORE?
Alan Friedman dba Zenco offers machinery vibration analysis courses and certification in accordance with ISO 18436-2. Click here to check out his course schedule, you can also connect with him on Linkedin. In addition to public classroom training and public virtual courses, Alan is also available for private courses virtually or on-site in addition to informal training and mentoring. Category I and II vibration are also available in Spanish.
Alan, aka the Vibe Guru, has over 30 years of vibration analysis experience, He has trained thousands of students around the world up to Category IV. One of the things that makes Alan a great teacher is his ability to teach people where they are at. Whether you are a math-challenged millwright, an engineer, or a PhD, Alan will challenge you without overwhelming you. If you are interested in condition monitoring you can also check out his book: Audit It. Improve It! Getting the Most from your Vibration Monitoring Program or hire him for an on-site program audit.
Did you know that Alan Friedman left Mobius and is now providing his own courses?
by Diana Pereda
Visual inspections of equipment should always be completed during vibration data collection or the collection of any type of condition monitoring (CM) data. This important function is often overlooked and valuable information on the condition of your equipment is lost.
Looseness and many other conditions are commonly found as a result of a vibration analysis program. The source of these conditions should be corrected to improve the equipment’s reliability. Visual inspections can easily be completed on the machine while the data collector is acquiring the data. The visual inspection may reveal the source of these equipment issues. This will save time because future efforts will not be required to determine the cause of the issue.
Visual inspections may provide a confirmation to the analyst of the problem(s) uncovered by the vibration analysis program or other CM technology. It is important to diagnose and confirm problems to ensure accuracy in your CM efforts. Visual inspections may often provide the confirmation opportunity needed.
Safety issues are often uncovered by these routine visual inspections and can be corrected before an employee is injured. This could save a life and the resulting return on the investment is priceless!
by Trent Phillips
When purchasing vibration analysis equipment, consider the following seven factors to ensure you select the most suitable and effective solution for your specific needs:
- Expandability: Choose a vibration instrument that can be upgraded with additional features and measurement capabilities as your needs grow. This ensures that your investment remains valuable and relevant over time.
- Reporting Capabilities: Look for a vibration analyzer that can generate comprehensive reports containing diagnostic results, complete with photos and notes. Detailed reporting is essential for clear communication and thorough documentation of findings.
- Advanced Diagnostics: Opt for vibration analysis systems such as the VIBWORKS LT that incorporates the latest Artificial Intelligence (AI) diagnostics technology. These advanced systems can assist in identifying machine faults more efficiently, reducing downtime and maintenance costs.
- Training and Support: Ensure the availability of training, mentoring and support from the vendor. Adequate training ensures that users can fully utilize the system’s capabilities, while reliable technical support is crucial for addressing any issues that may arise in the field.
- Accuracy and Precision: Ensure the vibration analyzer provides high measurement accuracy and precision. Reliable and repeatable results are critical for effective monitoring and analysis of machinery.
- Ease of Use: Choose a vibration analysis tool that is user-friendly and easy to operate. Intuitive interfaces, built-in help features, and straightforward operation can significantly enhance user experience and efficiency, and reduce the training burden.
- Durability and Build Quality: Assess the durability and build quality of the vibration monitoring system. It should be designed to withstand the harsh conditions of industrial environments, ensuring longevity and consistent performance. A cost-efficient upgrade path is a plus.
By carefully considering these factors, you can make an informed decision when selecting a vibration data collector that meets your specific requirements. This approach will help you find a solution that not only addresses your current needs but also adapts to future demands.
by Diana Pereda
The days of measuring vibration data directly at the machine once every couple of months are starting to disappear. There is still huge value in undertaking this activity, but it’s quickly being replaced by a wide range of IIoT sensors (Industrial Internet of Things).
Seemingly, one advantage is gathering data at a vastly improved rate. Rather than a single reading every quarter, data can now be captured multiple times every hour. The advantages are obvious: much greater visibility on developing faults and a trail to follow to track existing known issues.
But there are also some disadvantages. IIoT devices are battery-powered, so there is a balance to be achieved in data quantity, quality, and battery life. Typically, the faster you acquire data, the lower the battery life. If not, then the quality of the data might suffer.
It’s All a Balancing Act
In the case of condition monitoring, this might be reducing the FMax, lowering the resolution or only sending the spectrum rather than the full-time waveform. This can sometimes be against the desires of Vibration Analysts, who want the cleanest, highest resolution appropriate for the application.
Another problem that exists with such large data sets; how do you quickly sift through all these data sets to find what you need to look at? Is too much data inhibiting you from viewing the pertinent data you need to analyze?
Get the Data You Deserve
If using these IIoT systems, make sure that you select one that provides a good interface to search through data sets. Data views that trend key features in the vibration information so that you can quickly detect anomalies and go straight to the corresponding data set. Focus on systems that provide a good frequent snapshot to understand a fast change in trends, but still measures high quality waveforms and spectrums suitable for analysis.
Accuracy is Still Key
One other factor to assess is the accuracy of the data you are analyzing. Ask yourself these questions; How accurate is the frequency? Is the FMax suitable for your application? Is the amplitude showing the true energy? Is the data fully processed and ready for me analyze?
There are many tools that aid in understanding your machine’s health. Choose one that works best for your needs, but never underestimate how important data quality is to achieving an accurate assessment.
Thank you Sensoteq for sharing this educational article with us!
by Diana Pereda
MYTH: “It is acceptable to use a stinger attached to the vibration sensor.”
TRUTH: Stingers can be attached and used with most vibration sensors. However, stingers are the least desirable method to mount the sensor to the equipment. Stingers reduce the frequency range that can be measured with the attached sensor. Also, it is very difficult to use the same amount of pressure to hold the sensor to the equipment each time. This may further reduce the signal response as well as the consistency and quality of data.
MYTH: “Applying generic overall amplitude values allows the correct trending and identification of equipment faults.”
TRUTH: An overall level is a single number representing the amplitude of a vibration measurement. Overall values can be derived in many different ways. You should be very cautious when assigning generic and/or the same alarm values to your equipment. Similar machines can operate at different vibration levels. The individual characteristics of each machine should be taken into consideration when setting valid alarm levels.
MYTH: “Collecting vibration data quarterly, semiannually, or annually on equipment will identify all equipment defects.”
TRUTH: The collection frequency of vibration data should be determined based on several factors. Some of these factors are equipment load, the operational speed of the equipment, operational frequency, criticality, and more. It is possible to calculate the optimal measurement frequency required to routinely identify equipment defects. Assigning some collection frequency based upon manpower or other means almost always results in equipment failures that were not detected in time or at all by the vibration program.
by Trent Phillips
Sensoteq Kappa X wireless sensors have been deployed at a petrochemical plant in the UK to monitor machine vibration and prevent facility downtime. By using the sensor system for continuous machine monitoring, concerning defects with a vacuum pump were detected. Vibration analysts identified several issues on Analytix and calculated a fixed cost saving of $84,627.27 since installation.
Machinery and Operations
The petrochemical plant processes chemicals derived from petroleum for widespread use across many industries, including fuel and manufacturing. These petrochemicals are used for fibers, solvents and thousands of other products. The site uses several vacuum pumps to remove all air and vapor particles from an enclosed space. If a pump fails, the reduced suction can increase pressure, causing fuses to overheat and burn out, leading to machine damage and costly failures.
Implementation
To monitor vibration issues and potential bearing fatigue and faults, Kappa X sensors were installed on pumps and compressors throughout the site to measure potential bearing fatigues or faults. By detecting early signs of bearing wear, misalignment, and other faults, the Kappa X sensors enable predictive maintenance, helping to prevent unexpected breakdowns and extend the lifespan of the machinery.
Thank you Sensoteq for sharing this educational article with us. Click here to continue reading!
by Diana Pereda
Tired of being a vibration analyst? Sick of getting raises? Want to move to a different place of employment or collect unemployment benefits? Here’s one of the most sure-fire ways to accomplish it: Make sure nobody in management at your current employer understands how valuable your services are.
Seriously now, it is essential to your job security that management understands the value and cost savings that you bring to the organization.
- Make sure you quantify the “avoided cost” realized by your company due to your efforts or the efforts of those who may report directly to you. But never exaggerate the numbers so that no one will take them seriously. Be honest with your savings calculations. A job well done will save so much that exaggerating it is never necessary.
- Make careful reports that communicate to management the return on investment of your hiring, deployment, or training. Do not hesitate to report work and results that make your managers look good to their managers. This will ensure your longevity and prosperity quicker than you can imagine. Managers always like looking good to their bosses.
Be diligent and honest in your work and the savings and benefits will follow of their own accord!
by Diana Pereda
Every analyst has a few things they really don’t want to hear during the course of their work. These comments often indicate that proper maintenance activities have not been performed on the equipment, or convey unrealistic expectations of the analyst’s abilities. For instance:
- “It has always run like that!”
- “It really was making a noise before you arrived.”
- “We don’t have time to change the bearings. Just balance the machine so we can run it.”
- “How long will it last?”
- “Those bearings are brand new so I know they’re good.”
- “Yeah, we just use a torch to heat bearings to install them.” Use a SURETHERM induction heater with automatic demagnetizing to properly install your bearings.
- “We don’t have a bearing heater so we use a pipe and hammer to drive the bearing on.” Use a SURETHERM induction heater with automatic demagnetizing to properly install your bearings.
- “All we collect are overall vibration values, they tell us everything we need to know.”
- “It doesn’t take us long to change belts cause we just roll them on.” Very bad practice! Use a laser tool like the SHEAVEMASTER and loosen the feet of the motor before installing the new belts.
- “We don’t use no fancy alignment tool. All we need is a straight edge.” A recipe for disaster! Get a good laser shaft alignment system like the Easy-Laser XT770 —the money this will save in lost production and unnecessary repairs will more than pay for itself, not to mention the time saved for the analyst who can now dedicate himself to finding other more complex vibration problems.
- “My screwdriver does not confirm your analysis!”
- “You found the problem. Now go fix it.”
- “I didn’t realize you needed training.” Sign-up for a LUDECA vibration analysis training class.
- “I didn’t realize that this CM technology would create so much work.”
- “We need you to stop using that CM technology and turn wrenches this week.”
- “We didn’t realize you had identified and created a work order to fix that problem before it failed.”
No doubt you’ve heard a few more! Feel free to share them with us.
by Gary James CRL
A vibration analyst is constantly viewing data and seeking to identify indications of sub-optimal physical properties indicated by specific vibratory behavior. Most complex systems (if vibration analysis is allowed to be called a system) can be broken down into simpler sub-systems. Some of us, this blogger included, benefit greatly from such simplification in the vibration analysis process. This blog is about one such simplification which may be a helpful addition to the reader’s set of vibratory behavioral pattern recognitions.
As an analyst progresses in the field of vibration analysis, they will come to appreciate the phase property of vibratory behavior. Phase is used most often to look for defects by comparing it across couplings, from top to bottom, or end to end of structures, machines, or machine trains, etc. Here, the author would like to offer a more simplified way to use phase than is often taught or talked about, at least by those who work mostly with anti-friction bearing machines.
Phase in a single bearing:
Let’s approach phase in its simplest form: a single shaft in a single rolling element bearing. A perfect shaft in a perfect bearing, with everything done perfectly; no unbalance, no misalignment, no defects, will have zero relative phase difference between V(ertical) and H(orizontal). In fact, it will not vibrate at all. Because perfection does not exist, we don’t need to worry about running into it.
The machines you will run into will vibrate and the vibration will have phase. The phase of vibration measured at a single bearing will be caused by the imperfections acting on that bearing/shaft assembly. Consider the most common “near perfection” you will likely encounter in the day-to-day life of a condition monitoring technician. This near perfection machine has been aligned well enough for misalignment to contribute virtually nothing to the vibration signal, no bearing defect vibration, only the slightest rotational frequency vibration presumably contributed by a miniscule amount of residual unbalance.
The phase at rotational frequency on this machine will have an almost perfectly circular orbit and show an almost perfectly predictable 90° relationship between H and V. Now consider, if the unbalance increases, without any contribution from other defects, this 90° phase relationship will become even more stark, because the amplitude will increase making the phase reading more stable.
What about misalignment?
If misalignment were introduced into our “near perfect” machine, the orbit of the shaft in the bearing would almost certainly lose its circular motion and take on a herky-jerky motion characteristic, because now the shaft is prevented from the motion that unbalance induces on the shaft, by the restraint imposed by the misaligned bearings. The fact is that the perpendicular phase will now tend toward being either 0° or 180°. Just like the 90°-phase relationship which gets more pure as unbalance severity increases, the 0° or 180° phase relationship is likely to become more pure with an increase in misalignment severity.
How can the phase relationship at two perpendicular bearing points on rotating equipment be 0?
One might wonder how the phase difference could be zero at two perpendicular points. In this case, it helps to visualize the orbit of the misalignment-restricted shaft within the bearing. In the bearing orbit shown in figure 1, the amplitude at rotational frequency recorded on the V sensor and that of the H sensor are maximum at virtually the same instant.
Cautions:
There are other less common possible causes of the vibratory behavior of the very elongated orbit, such as resonance. A simple way to rule out resonance when possible, is to change the rotational frequency by 15% and then make a new observation. A cocked bearing would be an even more unlikely suspect if shaft misalignment is ruled out.
Download our 4 Stages Bearing Failures infographic for a basic reference guide to understanding the stages of bearing failures.
by Diana Pereda
Proper location is very important when collecting vibration measurements on a belt system. If possible, one reading should be taken in line with the sheaves and one reading perpendicular to them on each bearing. Vibration data resolution should be taken into account so that proper separation between belt and driver frequencies can be obtained. Care should be taken to ensure proper belt alignment as well. A laser pulley alignment tool provides the most efficient means to properly align belts. Another issue is how the belts are installed. Was the equipment loosened and the belt put on properly? Were the belts instead rolled on by force, creating potential issues? Have you ever seen a Vee belt running upside down? This is usually caused by the cording in the back of the belt being broken often caused by rolling on the belts. Are sheave gauges being used to check the sheaves for wear? In some cases, the cost of a belt is more than the cost of a new sheave. These are just some of the things to consider for proper installation, maintenance, and identification of belt-related problems.
Don’t just assume that belts are simple and do not require best practice actions for proper operation.
Don’t Forget To Inspect Your Belts! 9 Preventive Maintenance Tips
by Gary James CRL
- Shaft speed of machine being analyzed
- Type of bearings involved (sleeve vs. rolling element)
- Rolling element bearing part number(s) and manufacturer(s)
- Internal configuration of equipment
- Machine History
- Proper data collection location
- Proper sensor to use for data collection
- Proper data collection setups to ensure correct data is collected
- Is the primary energy sub-synchronous, synchronous or non-synchronous?
- If the time waveform is collected in acceleration then what is the “g” level?
by Gary James CRL
When it comes to analyzing vibration, sensor placement is key to quality of data capture. Motors can be large, surrounded by equipment and difficult to access, so locating an area to place your vibration sensor can be harder than it looks. A poorly placed sensor can, at best, reduce the vibration getting to the sensing element, and at worst, give completely invalid results, wasting time or even missing potential failure frequencies.
Placing a vibration sensor as close to the bearing as possible is the ideal scenario, but anywhere on the solid chassis that houses the bearing is normally sufficient. This is because the high frequencies that a bearing generates during a fault dissipate quickly in metals, reducing the amplitude of the vibration signal. These signals dissipate even more so when crossing an interface boundary, such as a bearing housing to another substructure. As a rule of thumb, try to mount a sensor within 1 foot (25cm) of the bearing to get the best results.
The absolute worst place for a sensor is on partially connected machine component, like the fan housing on a motor, or the connection box. Another location that is common for sensor placement, but is generally a bad idea, is on the motor cooling fins. As these protrude unsupported from the motor, they can resonate at other frequencies, giving further false results.
The interface between the sensor and the mounting surface plays another role in data quality. Magnetic mounts work well for fast mounting but start to attenuate signals above ~5kHz. When using a glue make sure to use a metal-based epoxy that is suitable for vibration signals, be aware of softer epoxy glues with flexible content, as they can drastically impact the signal. Mounting with a stud is always going to provide the best results and will work well, even above 10kHz Fmax.
Acquiring vibration signals should always be completed by an ISO Cat-I vibration analyst or above, as they are trained to do this. When mounting a sensor for continuous monitoring always seek the advice of an expert if unsure.
Thank you David Procter with Sensoteq for this informative article!
Download our Wireless Vibration Monitoring with Kappa X infographic to learn with an illustration how our Kappa X wireless triax sensors collect vibration and temperature data and move it to the Cloud via gateway for remote and continuous asset health monitoring with its Analytix software.
Choosing The Right Machines for Wireless Vibration Sensor Placement
by Diana Pereda
Every person that performs vibration analysis develops their own analysis process. Suggested steps at a minimum should include:
1. Open the spectrum (FFT) and locate the running speed peak and reset the reference speed to that speed. Since all induction motors vary in speed based on the load, this is necessary for accurate analysis, particularly at multiples of running speed.
2. Are there any peaks of interest?
3. Where is the primary energy located?
a. Is it sub-synchronous, synchronous, or non-synchronous?
4. Do the waveform patterns support the peaks in the spectrum (FFT)?
5. Remember that defects follow patterns. Some defects happen at frequencies less than running speed (sub-synchronous) or at running speed or at multiples of running speed (synchronous), or at frequencies greater than running speed but not at whole integers (non-synchronous).
6. Learn pattern recognition and don’t overlook the obvious.
Learn about our vibration analyzers
by Gary James CRL
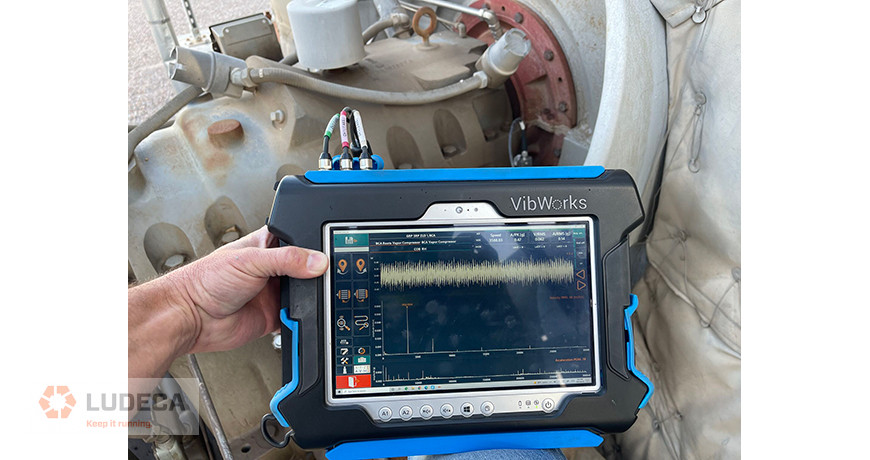
In the bustling world of industrial operations, machines are the workhorses, tirelessly powering production lines and driving progress. But just like any workhorse, they need their health monitored to ensure they’re performing at their peak. Enter vibration data—the secret weapon of predictive maintenance. Below are the top benefits of harnessing this data:
-
Early Problem Detection
Imagine your industrial machines as if they were cars. Just like a car makes certain sounds when something is wrong, industrial machines create vibrations that can tell us if something isn’t right. By collecting and analyzing these vibrations regularly, we can spot small problems before they turn into expensive repairs. This means we can fix things before they break down, saving time and money.
-
Keeping Operations Smooth and Efficient
Industrial machines are the backbone of operations, and any disruption can send ripples through the entire process. Vibration data helps us ensure that these machines are running smoothly, minimizing downtime, and maximizing efficiency. Monitoring the condition of an asset regularly, whether with a handheld vibration analyzer or a permanently mounted solution, can send warning signals when there are elevated vibration levels so that the plant can make necessary adjustments to make sure everything runs like clockwork.
-
Enhancing Safety and Preventing Accidents
Safety is paramount in any industrial setting. By monitoring vibration data, we can identify potential hazards before they escalate, preventing accidents and ensuring a secure working environment for plant employees and stopping potential environmental disasters that can affect the surrounding neighborhoods. It’s like installing Automated Emergency Braking (AEB) in a car—a proactive measure to protect the car, the driver, and its surroundings.
-
Extending Equipment Lifespan
Just as regular exercise can prolong human life, proper maintenance can extend the lifespan of industrial equipment, with emphasis on proper. Vibration data enables us to detect and address issues early, keeping machines in optimal condition. This can also reduce the need for premature replacements, which often lead to infant mortality of rotating equipment. It’s an investment in longevity.
-
Optimizing Resource Allocation and Decision-Making
Data-driven insights from vibration analysis empower informed decision-making. By pinpointing areas that require attention, organizations can allocate resources effectively, optimizing maintenance schedules and expenditures. It’s like having a GPS for maintenance—guiding us along the most efficient route.
In essence, vibration data is not merely a collection of numbers—it’s a roadmap to operational excellence, guiding organizations toward smoother operations, enhanced safety, and prolonged equipment lifespan. By harnessing its power, industries can navigate the complex terrain of maintenance with confidence and foresight.
Do you archive your historical vibration data or keep it around forever?
by Adam Stredel CRL
Setting the correct lines of resolution (LOR) can sometimes be challenging. In the example below we have a single-stage increasing gearbox. The gearbox is designed with three individual shafts (input shaft, intermediate shaft, and output shaft), all enclosed within a single gearbox housing.
The speed of the input shaft is constant at 29.93 Hz (1796 rpm) and attached to this input shaft is a pinion gear with 88 teeth. The pinion gear runs in mesh with a gear with 27 teeth which is mounted onto the intermediate shaft. This results in a gear mesh frequency of 2633.84 Hz (158,030.4 cpm). Now we need to determine the required Fmax. Therefore, we simply multiply our calculated gear mesh frequency times 3.25, which gives us an Fmax of 8559.98 Hz (513,598.8 cpm). In the software, we can’t select the value 8559 Hz, so we’ll need to select the next higher value which results in a Fmax of 10kHz. The next step in the process is to determine what the speed of the intermediate shaft is, and we can do this by using the following formula:
Intermediate shaft speed = 29.93 Hz × 88 teeth = 2633.84 Hz / 27 teeth = 97.54 Hz, or 5852.4 cpm.
We now need to decide how many lines of resolution we are going to need since in this gearbox we have two closely spaced running speeds. We have the intermediate shaft speed which is running at a constant speed of 97.54 Hz, and we have the output shaft speed which is variable. When the boiler feed water pump is operated at 100%, we have an output shaft running speed on the gearbox of 94.33 Hz or 5660 rpm. There is only 3.21 Hz or 192.6 cpm between the two shaft speeds within the gearbox so our lines of resolution setting will need to be set high enough so that we separate them while performing analysis. With a Fmax setting of 10kHz, we will need to have a minimum of 3200 lines of resolution so we would have two discrete peaks for the two shaft running speeds.
Fmax 10kHz / 3200 = 3.125 Hz, but to be on the safe side I would recommend selecting the next higher resolution setting [6400 line] which will allow a 1.56 Hz [96.3 cpm] resolution which is sufficient to easily see the two different shaft running speeds for accurate analysis.
Below are examples of the resolution, the first not being set high enough (top) and the second with the resolution set correctly (bottom).
Improper resolution settings resulting in a flat top peak for the output shaft speed:
Correct resolution setting (allowing for the separation of the two shafts turning speeds):
by Diana Pereda
Everyone needs phase analysis. A phase study should be performed on problem machines when the source of the vibration is not clear, or when it is necessary to confirm suspected sources of vibration. A phase study might include points measured only on the machine bearings or it may include points over the entire machine from the foundation up to the bearings. The following are examples of how phase can help analyze vibration.
SOFT FOOT
The term soft foot is used to describe machine frame distortion. It can be caused by a condition where the foot of a motor, pump, or other component is not flat, square, and tight to its mounting, or many other things, such as pipe stress, machining errors, bent or twisted feet, and non-flat mounting surfaces. Soft foot increases vibration and puts undue stress on bearings, seals, and couplings. Soft foot on a motor distorts the stator housing creating a non-uniform rotor to stator air gap resulting in vibration at two times line frequency. A good laser shaft alignment system should be used to verify soft foot by loosening the machine feet one at a time. Phase analysis can be used to identify soft foot while the machine is in operation. Measure the vertical phase between the foot and its mounting surface. If the joint is tight, the phase angle is the same between surfaces. If the phase angle is different by more than 20 degrees, the foot is loose or the machine frame is cracked or flimsy. Download our Soft Foot Find-and-Fix infographic which outlines types of Soft Foot including causes and corrections.
COCKED BEARINGS AND BENT SHAFTS
Phase is used to detect cocked bearings and bent shafts. Measure phase at four axial locations around the bearing housing. If the bearing is cocked or the shaft is bent through the bearing, the phase will be different at each location. If the shaft is straight and the bearing is not twisting, the phase will be the same at each location.
CONFIRM IMBALANCE
A once-per-revolution radial vibration usually means rotor unbalance. Use phase to prove imbalance is the problem. To confirm imbalance, measure the horizontal and vertical phase on a shaft or bearing housing. If the difference between the phase values is approximately 90 degrees, the problem is rotor unbalance. If the phase difference is closer to zero or 180 degrees, the vibration is caused by a reaction force. An eccentric pulley and shaft misalignment are examples of reaction forces.
LOOSENESS, BENDING, OR TWISTING
Phase is used to detect loose joints on structures and bending or twisting due to weakness or resonance. To check for looseness, measure the vertical phase at each mechanical joint. When joints are loose, there will be a phase shift of approximately 180 degrees. The phase angle will not change across a tight joint.
SHAFT MISALIGNMENT
Shaft misalignment is easily verified with phase. Measure each bearing in the horizontal, vertical, and axial directions. Record the values in a table or bubble diagram. Compare the horizontal phase from bearing to bearing on each component and across the coupling. Repeat the comparison using vertical then axial data. A good alignment will show no substantial phase shift between bearings or across the coupling.
OPERATIONAL DEFLECTION SHAPES
Instead of comparing the phase and magnitude numbers from a table or bubble diagram, operational deflection shape software (ODS) can be used to animate a machine drawing. An ODS is a measurement technique used to analyze the motion of rotating equipment and structures during normal operation. An ODS is an extension of phase analysis where a computer-generated model of the machine is animated with phase and magnitude data or simultaneously measured time waveforms. The animation is visually analyzed to diagnose problems. ODS testing is able to identify a wide variety of mechanical faults and resonance issues such as looseness, soft foot, broken welds, misalignment, unbalance, bending or twisting from resonance, structural weakness, and foundation problems.
Phase and magnitude were measured from permanently mounted X and Y displacement probes on a turbine generator. The values listed in the table were used in ODS software to animate a stick figure drawing of the high- and low-pressure turbine shafts and the generator shaft. The picture to the right of the table is a capture from the ODS animation showing the vibration pattern of each shaft and the relative motion between shafts at 3,600 cycles per minute (turning speed). Many machines vibrate due to deteriorated foundations, looseness, the resonance of the support structure, and other problems that occur below the machine bearings. A phase study might include hundreds of test points measured all over the machine and foundation. Good ODS software can make it easier to analyze phase and magnitude data from a large number of test points. Analysis of an ODS involves observation and interpretation of the machine in motion.
by Diana Pereda