In the field of vibration analysis, there is an abundance of technical terms. We provide definitions for some of these terms that you might hear from an engineer or technician as well as read in reports and might need further clarification. We welcome you to check out our glossary of terms relating to vibration analysis, and hope you find it valuable!
- Average – In vibration analysis, an average usually refers to the process whereby the vibration software will, after converting waveforms into spectrums via FFT, add the resultant spectrums together and then divide by the number of spectrums added together. The result is an “averaged spectrum”.
- Band – A band is simply a range of frequencies e.g. A band from 0 Hz, to and including 5 Hz, is a band that is 5 Hz wide.
- Band Pass Filter – A filter that blocks all data above and below its defined band.
- Condition Monitoring – The use of specialized equipment to deduce the actual condition of the equipment as pertains to its fitness for continued use. Condition monitoring is the foundation of Predictive Maintenance and the two terms are sometimes used interchangeably.
- Cycles per minute (CPM) – In vibration analysis, cycles per minute refer to the number of vibratory cycles that occur in one minute of time. Cycles per minute is a quantity of frequency.
- Cycles per second (CPS) – In vibration analysis, cycles per second refer to the number of vibratory cycles that occur in one second of time. Cycles per second is a quantity of frequency.
- Enveloping – Enveloping, also known as envelope de-modulation, is a data processing technique whereby a spectrum is created from a demodulated or filtered waveform.
- FFT – Fast Fourier Transform (FFT) is a mathematical process that transforms a waveform into the components of its frequency spectrum.
- Fmax – Fmax stands for “maximum frequency”. It is the high-frequency boundary for a set of data.
- Fmin – Fmin stands for “minimum frequency”. It is the low-frequency boundary for a set of data.
- Frequency Markers – These are visible marks that can be overlaid on a spectrum at specific frequencies to help identify likely machinery problems.
- Hertz (Hz) – The same as “cycles per second”.
- High Pass Filter (HP) – This filter blocks all data below it and only allows the data that is higher to “pass” and be recorded. It determines the “low-frequency cutoff” or Fmin.
- LOR – LOR stands for “Lines of Resolution”. It is the number of digital bins of amplitude information a spectrum will be constructed from.
- Low Pass Filter (LP) – This filter blocks all data above it and only allows the data that is lower to “pass” and be recorded. It determines the “high-frequency cutoff” or Fmax.
- Negative Averaging – A procedure whereby, having previously taken a reading, a second reading is taken and all data in the first reading that matches data in the second reading is subtracted.
- % Overlap – % overlap is the amount several otherwise sequential waveforms, being sampled and averaged into a spectrum, will “overlap one upon the other” as they are being sampled.
- Peak-to-Peak – The measure of vibration amplitude in a waveform, from the negative peak to the positive peak.
- Unbalance – A measure that quantifies how much the rotor mass centerline is displaced from the centerline of rotation.
- Waveform – In vibration analysis, a waveform is a display of vibratory energy over time.
by Trent Phillips
In the world of vibration analysis frequency is everything. Frequencies are generated by many sources within a machine. The running speed of the machine is one example frequency; this is the velocity of the rotating element which in many cases is a drive shaft connected to an application (like a fan or a pump). Each frequency will have a magnitude associated with it; this is the total amount of energy of that specific frequency. The amount of energy of any given frequency can tell us a lot about what is going on within a machine. When we use a vibration sensor to measure a machine, this is what we are detecting, frequencies, and magnitudes of those frequencies.
The maximum frequency that a sensor can measure is called the Fmax. This value lets the user know what type of faults they can detect on a machine. It is typically listed in hertz (Hz). The higher the Fmax value, the greater number of faults that a sensor will detect, but it will also allow for earlier indication of potential faults, like a bearing failure. Some ISO standards will reference a Fmax of 1kHz – whilst taking a reading up to 1kHz is suitable for most acceptance testing, it will not highlight even the most basic of bearing faults. A minimum of 2.5kHz Fmax is recommended for good coverage.
Recently, a new sensor has entered the market that boasts a Fmax up to 10kHz. This Fmax gives great coverage for a wide variety of faults, and will accurately inform users of issues on complex equipment like gearboxes that have many higher fault frequencies. In addition, a higher frequency will give an earlier indication of bearing faults. Bearing failures will typically start within the subsurface of the metal with a very small amount of energy being emitted to the sensing element, thus having a sensitive measurement device with the right Fmax is critical to understanding the health of your machine early, prior to failure impacting any processes or causing downtime.
Thank you David Procter with Sensoteq for sharing this educational article with us!
by Diana Pereda
Some vibration software allows for the end user to build a database quickly and easily. For instance, preconfigured machine templates that cover ninety percent of the equipment found in a typical plant is a highly desirable feature.
Below is an example of a motor and pump configuration. The ease and flow of the template allows for quick setup. The option to copy any built template allows for duplicate configurations to be quickly added to the database.
Once the template has all the necessary information and is saved, it builds all the points in three axes (H, V, and A), and automatically assigns a measurement pack to the points of that newly saved template. This saves a lot of time and effort. T measurement pack can be changed after data is collected and reprocessed using new parameters without needing to recollect data on the machine.
Learn more about vibration software capabilities with our BETAVIB Vibworks. Collect, analyze, and report your data plus perform reliable diagnosis & condition monitoring on rotating machines!
Related Blog: The Devil is in the details when it comes to equipment setup in a vibration database
by Diana Pereda
Do you use accurate alarm values for your vibration analysis program or other Condition Monitoring technologies?
Setting accurate alarm values will help you identify equipment, however, the benefits go beyond this. Missing alarms or inaccurate alarms may force your analyst to review every machine each time data is collected, which wastes a lot of time that could be used more productively for other reliability efforts. Setting accurate vibration alarms ensures that data for each machine does not have to be reviewed each time it is collected. The vibration analysis software, vibration data collector or other CM technology can alert your analyst of those machines that actually need to be reviewed. This will increase the analysis accuracy and save you time and money. There are many tools available with our VibWorks vibration analyzer and data collector to assist the analyst in setting alarms, foremost of which is the SAM, or “Smart Alarm Module”, where alarms can be set or adjusted utilizing Linear, Standard Deviation, or manual entry.
Related Blog: Setting Alarm Values for your Vibration Measurements
by Diana Pereda
Disclaimer: The author is not trying to present himself as an authority on all available CM standards. This blog post is simply an attempt to help those who may be unaware that such guidance exists or of the extent of such standards.
We previously introduced a series of international standards pertaining to condition monitoring of industrial equipment with vibration analysis in,
This series ends with the numeric sequence of xx816-x. The original standards from 1974 (ISO 2372) and 1985 (ISO 3945) were replaced or superseded by ISO 10816-1 in 1995. 10816-1 was amended in 2009 and then replaced by ISO 20816-1 in 2016. Next (numerically) is the standard we also mentioned in our previous blog, 20816-2. The dash 2 standard covers the measurement and evaluation of vibration on large land-based gas or steam turbines and generators.The subsequent standard in the series, the “dash 3” standard is the focus of this blog. This standard is titled:
INTERNATIONAL STANDARD ISO 10816-3
Mechanical vibration — Evaluation of machine vibration by measurements on non-rotating parts
Part 3: Industrial machines with nominal power above 15 kW and nominal speeds between 120 r/min and 15 000 r/min when measured in situ
ISO 10816-3 is the current standard in the series that covers a general range of equipment types and sizes. When first created it was the “catch-all” standard used for many types of machines (such as centrifugal pumps which are now covered by the dash 7 standard) that have since come to be covered by their own specific part of the series. The “10816” issuance of the dash 3 standard is still in force, but to be current it must be joined by a 2017 amendment, “Amendment 1”. This amendment actually modifies the scope of the standard, so it is critical to its being considered current.
The scope of this standard is quoted below from the ISO.org preview page (quotation in bold).
Important Note: The scope shown in the preview cannot be considered current because it is modified by Amendment 1.
Scope:
This part of ISO 10816 gives criteria for assessing vibration levels when measurements are made in situ. The criteria specified apply to machine sets having power above 15 kW and operating speeds between 120 r/min and 15 000 r/min.
The machine sets covered by this part of ISO 10816 include:
- steam turbines with power up to 50 MW
- steam turbine sets with power greater than 50 MW and speeds below 1 500 r/min or above 3 600 r/min (not included in ISO 10816-2)
- rotary compressors
- industrial gas turbines with power up to 3 MW
- generators
- electrical motors of any type
- blowers or fans
NOTE: However, the vibration criteria presented in this part of ISO 10816 are generally only applicable to fans with power ratings greater than 300 kW or fans that are not flexibly supported. As and when circumstances permit, recommendations for other types of fans, including those with lightweight sheet metal construction, will be prepared. Until such time, classifications can be agreed upon between the manufacturer and the customer, using results of previous operational experience, see also ISO 14694[4].
The following are excluded from this part of ISO 10816:
- land-based steam turbine generator sets with power greater than 50 MW and speeds of 1 500 r/min, 1 800 r/min, 3 000 r/min, or 3 600 r/min (see ISO 10816-2)
- gas turbine sets with power greater than 3 MW (see ISO 10816-4)
- machine sets in hydraulic power generating and pumping plants (see ISO 10816-5)
- machines coupled to reciprocating machines (see ISO 10816-6)
- rotodynamic pumps including integrated electric motors, i.e. where the impeller is mounted directly on the motor shaft or is rigidly attached to it (see ISO 10816-7)
- rotary positive displacement compressors (e. g. screw compressors)
- reciprocating compressors
- reciprocating pumps
- submerged motor-pumps
- wind turbines
The criteria of this part of ISO 10816 apply to in situ broad-band vibration measurements taken on the bearings, bearing pedestals, or housing of machines under steady-state operating conditions within the nominal operating speed range. They relate to both acceptance testing and operational monitoring. The evaluation criteria of this part of ISO 10816 are designed to apply to both continuous and non-continuous monitoring situations.
This part of ISO 10816 encompasses machines that may have gears or rolling element bearings but does not address the diagnostic evaluation of the condition of those gears or bearings.
The criteria are applicable only for the vibration produced by the machine set itself and not for vibration which is transmitted to the machine set from external sources.
To read the ISO’s preview of this standard, click here.
by Diana Pereda

The use of a strobe light or stroboscope is another tool in the toolbox of the analyst in the field of Reliability. This tool can be used for a variety of purposes including checking or verifying the rotational speed of a component if the shaft or coupling is accessible.
The user can inspect it without stopping or shutting down the equipment. If the model of stroboscope the user has is capable of being triggered from an external source for the flash rate the user can move the flashing strobe around the machine’s moving parts to see which one appears to stop which can indicate that this is the source for the triggering and therefore the source of vibration.
Most stroboscopes have an output that can send a signal to a vibration instrument to be used as a tachometer input to the instrument. Dynamic balancing can be performed using a stroboscope instead of a laser, optical or infrared tachometer.
A key safety consideration is that one must remember when utilizing a stroboscope that rotating structures (such as shafts or couplings) only appear to be frozen or stopped when the stroboscope flash rate is synchronized to the same frequency as the shaft’s rotational speed.
People who are not familiar with stroboscopes have reached out to touch what appears to be a stopped shaft and become seriously injured. When using a stroboscope and the machine has not been started the user can use a marker and place a horizontal mark on one side of the shaft and a vertical mark on the opposite side so when the machine is running and you adjust the internal oscillator in the stroboscope to match the rotating shaft’s frequency you will either see a vertical or a horizontal mark; if you see a plus sign then the flash frequency is either half or double the shaft frequency.
For a sample on how a strobe light is applied for Synchronous Peaks vs. Non-Synchronous Peaks, watch this video from our partner, Karl Hoffower with Failure Prevention Associates, LLC
by Diana Pereda
A balancing tool is simply anything that serves the analyst for the purpose of statically or dynamically balancing a rotating piece of machinery.
Precision balancing should include:
- An instrument capable of reading data from different types of vibration sensors, including accelerometers, velocity sensors, and proximity probes among others.
- It should also be able to display the rotational speed of the machine and the phase angle of the unbalance. The instrument should have a tachometer or a stroboscope input to measure a target on the rotating component indicating the rotational speed in CPM/RPM/Hz.
- The analyst would also need to have a way of measuring the exact amount of weight that they may need to add or remove from the rotor for the purpose of balancing and a way of attaching those weights. These could include clamping with set screws or bolts, bolts and washers, welding of plate material, and here care must be taken to ensure the metallurgy of the machine is not compromised.
- The instrument the analyst is using should include a software program that the analyst is familiar with. The time to learn a balancing program is not in the field while trying to perform a balancing job. If the analyst does not have a program for balancing he or she should be able to graphically plot out the balance solution as necessary. This approach is usually slower and more error-prone.
- The cables that connect the sensors and the tachometer to the instrument should be of adequate length to be safely installed. There should also be thought about how to attach the sensors and tachometer to the equipment so they do not become detached during the balancing process.
- The analyst should also have a way to document the balancing process.
To help you implement balancing at your facility, download our 5-Step Balancing Procedure a simple and effective procedure for doing field balancing!
by Diana Pereda
“What’s shaking?” was a commonly used question many years ago to ask someone how things were going. It was very generic and could cover a vast range of things. It is still used today but the frequency in use has declined.
When that question is asked of a person, the normal reply is “Not much.” or “Everything is good.” But beware if asking this question to a vibration person. The reply would be “Everything.”; everything is shaking, but it’s the amplitude and frequency of the shaking that is the deciding factor. The first thing that will be noticed after answering the question is the blank stare in the eyes of the person that asked the question. If at a party or gathering with non-vibration people that person will try to excuse themselves away after hearing the reply.
Of course, as a vibration person, the blank stare means that further explanation is needed to assist with the understanding of frequency and amplitude to the questioner. This should help them understand what is really happening when things shake, or more precisely when they shake too much. The thinking is that maybe with an explanation the blank stare will vanish, leaving a glint of understanding in the person’s eyes. Nothing could be further from the truth. As the party has no whiteboard to draw on except cocktail napkins, using hand gestures to explain frequency over amplitude and how side banding can tell a lot about which component is failing on a machine, only changes the blank stare to a trapped animal expression.
After an hour of educating this person, my wife usually walks up to save the unfortunate victim. She whispers in my ear that we had an agreement. If anyone were to ask what I do for a living I would say I work with computers and not mention vibration. Of course, I did find a loophole as he asked me “What’s shaking.” not “What I did for a living.”, but that is another story.
The moral of this story is that there are a lot of people that do not know or care about vibration. Our job is really two-fold in that we have to make certain the machines we monitor run as long as they can, and that we can explain the condition of the machine to a “non-vibration layperson” in a very short summary.
I find that showing a picture of a machine spectra containing high amplitude vs. the same machine many months ago when the vibration levels were low will allow the viewer to be able to see the differences without too much vibration explanation needed. A picture is really worth a thousand words, and if you add alarms and color to the report it helps push across your point.
Remember to keep the reports simple for others to see and have a detailed report for yourself that explains everything.
The example below is from a Component Report which displays when the data was collected and what alarms were seen during the collection dates.
If you are interested in seeing all the reports that are offered in the VibWorks software please contact us to schedule an online presentation.
by Diana Pereda
Simon is a condition monitoring specialist from a local oil refinery. He contacted SDT for advice on predicting flexible coupling failures. Currently, they perform condition monitoring on their pumps and motors using vibration analysis. They identified most bearing failures in time but could not detect coupling defects; there was no safe place to mount a contact sensor. Several unexpected failures caused shaft damage and unplanned downtime.
Within the facility they identified 58 pump systems considered “A Critical”, meaning if they go down, the plant goes down. I suggested ultrasound as a fast, safe, and affordable coupling monitoring solution. The model I recommended not only provided Simon with a means to observe couplings, it also measures vibration, eliminating the need to carry two data collectors.
Vibration analysis performs poorly on flexible couplings for two reasons. First, there is no suitable contact point for an accelerometer. Second, the primary defect symptoms of a defective coupling are friction and impacting. These are best detected with ultrasound. An airborne sensor placed near the coupling quickly detects problems. If necessary, Simon can capture a dynamic measurement and trend the defect as it worsens. The SDT270DU gives Simon two choices. He can periodically check for defects (Good) or Simon can integrate all 58 couplings into his established bearing routes (Best).
I explained to Simon how several clients already trend couplings using the Flexible Wand. The SDT270 collects a STATIC ultrasound measurement that gives four indicators of the condition. The first two – Overall RMS and Max RMS – indicate the level of friction produced by the defect. When these indicators rise, maintenance may consider corrective alignment during a planned shutdown. The second two – Peak and Crest Factor – identify the emergence of impacting. Together, all four indicators establish a lifecycle trend for each coupling.
Once impacting appears, the Peak indicator increases in step with Overall RMS. Since Crest Factor (CF) is a ratio between RMS and Peak, a rising CF indicates that the window for simple maintenance has narrowed. At this stage, inspectors collect a DYNAMIC measurement. The DYNAMIC measurement gives a visual representation of friction and impacting severity using the time view. For both STATIC and DYNAMIC measurements, it’s important to define the signal acquisition time.
User-defined signal acquisition time, available exclusively on SDT instruments, is a luxury that lends ultrasound technicians the highest level of precision. Without the ability to set the sample time, inspectors must guess when to pull the measurement trigger, and then question the validity of their data. Simon explained that all 58 pumps turn at speeds above 1800 RPM. Accordingly, he should set his SDT270’s signal acquisition time to between one and three seconds. This guarantees data samples over 30-90 shaft revolutions.
Shaft couplings are guarded for safety and ultrasound inspectors working around rotating equipment must follow company safety policies. SDT designs safety considerations into their solutions. The Flexible Wand’s 10mm diameter sensor allows access to couplings without the need to remove safety guards. The 21” long sensor sports a comfortable, ergonomic grip that keeps the inspector’s hands at a safe distance.
Simon seemed convinced but wanted to #HearMore. Since this solution was already working well at a nearby paper mill, I introduced Simon to the plant manager, Sunil, and invited them both to lunch. Sunil and Simon connected on many common reliability issues that afternoon. He confirmed the affordability of this solution based on coupling failures alone but went on to explain how their mill was rolling out ultrasound for acoustic lubrication, steam trap monitoring, electrical inspection, and air leak management. Simon and Sunil continued their conversation well into the afternoon. They agreed that ultrasound, with its 8 application pillars for reliability, represented a fast, safe, and affordable technology with the potential to revolutionize reliability culture. I sat back, happily watching two passionate specialists strategize about reliability culture. I love my job.
Related Blog: Ultrasound for Coupling Inspection? Yes!
by Diana Pereda
Many shafts have keyways cut into them to hold the coupling. “Keys” are pieces of square metal stock inserted to hold the hub in place.
If there are two (2) keys, one on each side of the coupling, you should not “align” the keys across the coupling. Instead, it is very important to ensure the coupling mass is balanced during installation. The mass of a key is balanced by setting the two keys 180 degrees apart from each other. If the keys are set on the same side, the coupling will induce a mass unbalance situation.
Often a vibration report will note a misalignment condition, but precision alignment techniques will not find any issue. This can lead to friction between the vibration analyst and the millwright. Keep the keyways 180 degrees apart. You will help improve the life of the coupling and keep the vibration low.
by Diana Pereda
Every person that performs vibration analysis develops his or her own analysis process. Suggested steps at a minimum should include:
- Open the spectrum (FFT) and locate the running speed peak and reset the reference speed to that speed. Since all induction motors vary in speed based on the load, this is necessary for accurate analysis, particularly at multiples of running speed.
- What are the dominant peaks?
- Are there any other peaks of interest?
- Where is the primary energy located?
a. Is it sub-synchronous, synchronous, or non-synchronous? - Do the waveform patterns support the peaks in the spectrum (FFT)?
- Remember that defects follow patterns. Some defects happen at frequencies less than running speed (sub-synchronous) or at running speed or at multiples of running speed (synchronous), or at frequencies greater than running speed but not at whole integers (non-synchronous).
- Learn pattern recognition and don’t overlook the obvious.
- Generally, most equipment doesn’t have only one issue going on, learn to sort out the various problems and tackle the worst one or ones first.
Test Your Vibration IQ and see how much you know and maybe learn something along the way!
Related Blog: The Importance of Vibration Analysis
by Diana Pereda
A sensor generally measures 95% of what it’s capable of measuring in line with the sensor. Two common types of vibration sensors are:
-
Single axis accelerometers
-
Triaxial accelerometers
So which one is best for your application?
A single axis sensor simply measures vibration in only one axis, so the sensor can be moved to the direction or axis of interest to be measured. A triaxial sensor has three sensors built into one housing and therefore can measure three axes or directions without having to relocate the sensor, as with a single axis sensor.
Image Courtesy of Connection Technology Center, Inc. – CTC
All data systems on the market today will use a single axis sensor, however, some are also capable of utilizing a triaxial sensor but not all three channels at once. Some two-channel instruments can use a triaxial sensor but they will only process two axes at one time then take the third axis reading. To collect all three axes simultaneously you need a true three-channel (or greater) analyzer. For example, the VIBWORKS vibration instrument allows for both triax and single axis data collection. The VIBWORKS is a true four-channel instrument. Triaxial data collection can be a time saver when collecting large amounts of data, but as with all things there are pros and cons. Using single axis sensors would typically involve moving the sensor from the horizontal to vertical to axial positions at each bearing to collect the data. Using a triaxial sensor you place the sensor at the bearing and collect all three axes simultaneously. Drawbacks to triaxial sensor are the cost of the sensor and cable; the sensor alone can cost 3× or more the price of a single axis sensor. At some facilities that use a triaxial sensor they simply place the sensor at a single location on a machine and take the three axis readings and move onto the next machine. Only if a problem is detected they return to the machine and take more precision data. The user must make sure the sensor is always orientated and placed the same each time readings are collected as the sensor has three axes X,Y, and Z and if the orientation of the sensor is turned the trend of the machine data becomes skewed or void.
by Diana Pereda
First one must know what the definition of phase is in the reliability world. Phase is simply the relationship between two events. There is absolute phase that is usually measured as either “phase-led”, which is from the peak in a filtered time waveform to the tachometer, or once per revolution indicator, or “phase-lag” which is from the tachometer or once per revolution indicator to the peak in a filtered time waveform. Of the two, phase-lag is probably the most common.
There is also relative phase which takes two filtered time waveforms and compares the phase between the two. Generally your Channel One or A (as the case may be) is stationary and you can move Channel Two or B from position to position and get the indicated phase. Relative phase can be a time saver as the user can get an indicated phase without shutting down the machine to put reflective tape on the shaft for a laser or optical pick-up. This can be used to verify or diagnose unbalance, misalignment, and looseness, etc., but it cannot be used for dynamic balancing which requires absolute phase for repeatable calculations. Whichever type of phase is used, you can use it to identify and/or confirm unbalance; check the phase on each side of the coupling as well as across the coupling to determine misalignment and what type of misalignment. Note: Always remember the orientation of the sensor as motion towards an accelerometer is positive energy in the time waveform and motion away from the accelerometer is negative energy in the time waveform.
The user can place the sensor on each side of a junction where two surfaces come together and look for a phase shift which indicates the two surfaces are not tight to each other. This could be looseness between a motor foot to the base, or from the base to the sole plate, or from the sole plate to the foundation, or even from the foundation to the slab. If everything is tight then the machine will move as one.
Phase can also be used to look for cocked bearings, bent or bowed shafts and other things as well.
Our advanced vibration analyzers, along with phase analysis, can help you better diagnose fault conditions.
Featured Graphics taken from Vibration Diagnostics report by Alena Bilosova and Jan Bilos – Ostrava 2012
by Diana Pereda
Primarily, there are three types of sensors in use today:
- Velocity transducer
- Accelerometer
- Proximity probe
Each has its own sensitivity, which simply means that for a given input you get a given output.
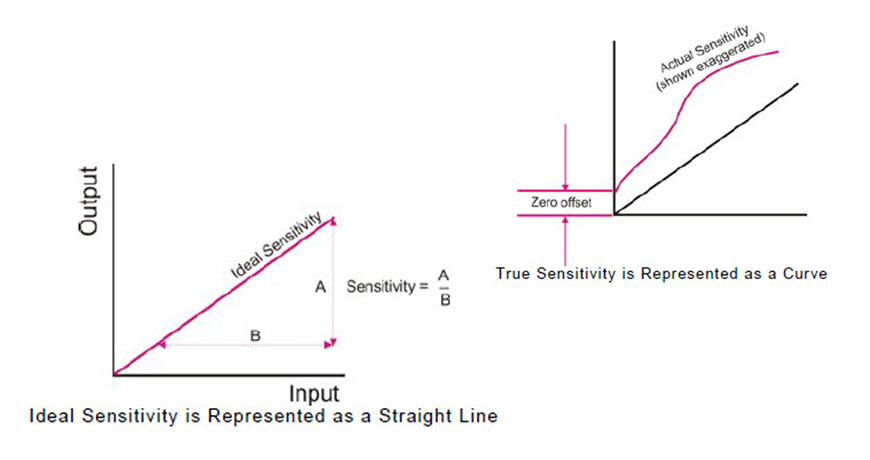
Velocity Transducer
Simply a suspended magnet inside an electrical coil. The coil is affixed to the machine housing and moves with the housing, whereas the magnet attempts to remain stationary within that coil, thereby generating voltage. This sensor generally has an output of 1.0 volts per inch per second.
Accelerometer
Usually made up of a Piezoelectric Crystal preloaded with an amplifier, and, as the sensor housing moves due to vibration, the crystal is compressed and released, creating an output that for a standard sensor is 0.100 volts/g or 100 mv/g. Most accelerometers have a total voltage output of 5 volts or 5000 mv. With this sensitivity, if you take 5000 mv divided by 100 mv/g this gives you a range of 50 g’s peak.
Proximity Probe
Commonly called a prox probe. This sensor has a probe that is mounted through a journal or babbitt bearing and measures the movement of the shaft relative to the bearing. These sensors consist of the probe which has a magnetic coil in the tip that produces an eddy current when charged; this is connected to an extension cable which is connected to the proximiter. The proximiter is what powers the probe and supplies a signal to be monitored. The length of the probe cable and the extension cable determine the sensitivity. These are powered by a DC power source which creates the magnetic field at the probe tip. The probes are calibrated for specific shaft materials such as AISI 4140 steel, a low alloy steel containing chromium, molybdenum, and manganese which is widely used for shaft construction for rotating equipment; other types of materials are also used. When purchasing proximity probe systems you need to tell the supplier what the shaft material is so the probes can be properly calibrated. When installed, the static distance between the probe tip and the shaft surface is measured by measuring the DC voltage or Gap Volts; the movement or vibration of the shaft is a measurement of the changing or modulating of the DC—think of the gap volts as a DC signal and the vibration as an AC signal riding on the DC. The most common sensitivity of proximity probes is 0.200 v/mil, so for every 0.001 in. the shaft moves the voltage would change by 200 millivolts.
Take a look at our vibration analysis tools and how they interface with velocity transducers, accelerometers, and proximity probes.
by Diana Pereda
A route for vibration programs is the order in which machines that need to have vibration data collected on them have that data collected. To be able to optimize the data collection time and effort, the best practice is to have multiple routes. The machines in the route should be listed in a strategic and time saving list. If you were walking through the plant, which machines would be reached first, second, third, and so forth. The order of the routes themselves is very important as well and the time it takes to gather the data. If some machines (such as slow speed gearboxes) take a lot longer to collect data on, then perhaps a separate route might be needed just for them.
If the routes are not in a logical order then additional time is needed on the instrument to select the correct machine to start data collection. While 10 seconds might not seem that long to select the correct machine, if you have 200 machines on a route it could easily take an additional 30 minutes to finish that route if it is not logically configured. Data collection on that one route each month for the entire year could quickly turn into 6 hours of wasted time. Most plants have multiple routes and this wasted time figure could increase very quickly.
Routes are only the list and sequence of the equipment and do not hold any data themselves (within the VibWorks systems) and can therefore easily be deleted and re-created as many times as needed.
Reviewing your routes yearly could assist in eliminating wasted time.
by Diana Pereda
First off, “triax” is short for “triaxial accelerometer sensor”. A triaxial sensor has three (tri) separate sensors (that collect data in the X, Y, and Z directions) contained in one housing, compared to a single axis sensor in a normal accelerometer.
There are many pros and cons to using a triaxial sensor. A few things to consider:
- Cost
- Position
- Data frequency
- Time
The triax sensor (Fig. 1) is more expensive than the single axis sensor (Fig. 2). When using the triax sensor, it has to be mounted in the same orientation each time or the directions will not match the data that was collected before. Many places sell triax mounting pads to make certain that the sensor is locked in a certain orientation to ensure correct data collection. This represents an additional cost, and time must also be budgeted to mount the pads. Do not mix sensors when collecting data. If the same motor is having vibration data collected using a triax sensor, then do not collect data another month with a single axis sensor. A single axis sensor will need to be moved three times to the correct orientation for data collection whereas the triax was mounted in just one position. This could affect the trending of your data.
The VIBWORKS vibration instrument allows for both triax and single axis data collection. The VIBWORKS is a true four-channel instrument. This allows the instrument to collect data in all three directions at once. Normally three directions are taken per bearing on equipment. Depending on the setup and the equipment, it could take up to 20 seconds per direction to collect and save the vibration data. On a normal motor-fan machine train this means 12 directions which would take around 4 minutes to collect vibration data on, using a single axis sensor. Using a triax sensor it would only take 80 seconds to collect vibration data on the entire machine train.
When selecting a triax sensor, make certain that the vibration instrument is not multiplexing the vibration channels. For example it the instrument is only capable of two channels it will collect two channels at the same time and then collect the third channel separately. This means it would take almost three minutes to collect data as all three channels are not being collected at the same time.
by Diana Pereda
Where to place the vibration sensor depends on what data you wish to see. Certain defects show up better in the horizontal direction while other defects show up better in the vertical direction. So which location should I choose to place my vibration sensor? Most sensors in use today are single-axis sensors, so generally 95% of what they pick up or detect is in line with the sensor. Therefore, since placement of the sensor is crucial, some thought should be given as to what data shows up best in which of the three directions—vertical, horizontal, and axial. Data taken in the vertical direction will typically show looseness better than in the horizontal direction (at least on a horizontally mounted piece of equipment); however the horizontal will show unbalance better than the vertical. Axial vibration will show angular misalignment better than a radial reading will.
Also, it should be considered that in the real world there are times that the sensor cannot be placed directly on a bearing, such as with the non-drive end bearing on an electric motor due to the fan cover; on large motors this cover can extend 10 in. or more from the bearing, and considering that rolling element bearing generate high frequency data in early stages of failure and high frequency data only travels short distances, the data can and will be diminished the further from the bearing that you take your reading. In these cases you simply get as close as possible to the bearing knowing the generated signal may be diminished; in such case you should pay special attention to the frequencies present as they may be at lower levels than expected. If you are dealing with vertical equipment it’s typically stiffer in-line with the discharge than perpendicular to the discharge and that will affect your data as well.
For more information on a vibration tool to collect and analyze your sensor data, check us out!
by Diana Pereda
When using phase to determine how a machine is moving, the orientation of the sensor mounted on the machine is extremely important. In Figure 1 below one sensor is attached to the motor’s outboard (non-drive) end in one orientation, and on the other inboard (drive) end, it is mounted in the opposite direction.
Because the sensors are attached to the motor’s ends opposite one another the resulting phase angles would be 180 degrees opposed to each other. To correct for this, the user has to choose a reference location and then correct the measured phase angle for any sensor locations where the sensor position is opposite the reference.
For measured phase readings of less than 180 degrees the user would add 180 degrees to the measured phase angle and for measured phase angles that are greater than 180 degrees the user would subtract 180 degrees from the measured reading.
In most applications this occurs most often in the axial direction of measurement; however, sometimes due to obstructions, the user cannot physically place the sensor in the same orientation as the reference sensor in the horizontal or vertical axis.
Just as with the axial direction, the user will have to determine a reference location and then correct the measurements for any locations where the sensor position doesn’t match the reference location.
Figure 2 below is what is commonly called a “Bubble Diagram”. The bubble diagram is used to record the vibration amplitude and phase angle at all machine locations in the machine train in the vertical, horizontal and axial directions.
As previously stated, the analyst must determine if any sensor measurement locations will require the sensor to be attached to the machine differently and adjust the phase readings at locations different from the reference accordingly.
The easiest way to keep track of reference directions and location is to draw a little arrow as shown below in Figures 3 and 4. If the arrow is pointing towards the machine this indicates that the phase angle was recorded directly as indicated.
When the arrow is pointing away from the machine as shown above in Figure 4, the phase angle recorded in the bubble diagram is 180 degrees opposed from what was actually measured.
Source: Practical Solutions to Machinery and Maintenance Vibration Problems by Update International
Our advanced vibration analyzers, along with phase analysis, can help you better diagnose fault conditions.
by Diana Pereda
Sometimes unbalance can be caused by a shaft key being too long. When a shaft assembly goes to the balance machine, the assembly is normally balanced with a half key installed. The coupling and key have been removed and a half key installed into the keyway on the shaft. The straight portion of the shaft keyway is filled with a piece of steel; however its height is ground down so that it closely matches the outer radius of the shaft. In other words, it doesn’t stick out!
Electrical tape is then wrapped around the half key and shaft so that the half key doesn’t come flying out during the balancing operation. After the rotating assembly has been successfully balanced to within tolerance, the rotating assembly is returned to the technician for final reassembly.
In the following example, let’s assume that the actual length of the keyway in the shaft is 8 inches long and 3/8″ deep. The length of the coupling hub keyway is 4 inches long and it is also 3/8″ deep. If the technician installed a key that measured 8″ long × ¾” × ¾” and then mounted the coupling onto the shaft it would result in an excessive key length sticking out past the back edge of the coupling hub. The extra 4 inches × 3/8″ high key stock sticking out behind the coupling could be enough mass to cause the imbalance to exceed ISO balance tolerances.
The following method should be used to calculate the proper key length:
Source: Practical Solutions to Machinery and Maintenance Vibration Problems, Chapter 5, Unbalance, Section 16, Unbalance Due to Assembly Errors – Key Length Considerations by Update International
Our advanced field balancers can help you identify, correct and avoid the unwanted consequences of equipment unbalance. For more information, visit our website.
by Ana Maria Delgado, CRL
Vibration is everywhere! Vibration is a “back and forth” movement of a structure or component. Vibration can also be referred to as a “cyclical” movement. It can be inherent in a piece of equipment or can be induced by another form of energy. The real question is whether the vibration is detrimental to the equipment and its internal components.
Vibration is typically monitored through some form of analyzer, either online or offline such as the VIBWORKS analyzer.
What causes vibration? Here are just a few causes, but there are so more which can lead to elevated vibration levels. More importantly, if caught early enough, they can be corrected and thereby maximize the life of our equipment:
- Installation of the machines
- An improperly mounted bearing can cause severe vibration. This can lead to damage of the bearing as well as other components within the machine.
- Operation of the machine
- Pushing our machine beyond its recommended maximum output. Our machines respond by vibrating more than the recommended allowable limits and will eventually fail.
Watch our video ‘What’s Misalignment’ to learn more about the causes and effects of having misalignment in your rotating equipment
Some common machine problems that generate mechanical vibration:
- Misalignment
- Misalignment is one of the most common issues that leads to high vibration and eventually failure of the machine. It can be easily detected and corrected. Take the time to laser align machines properly to the recommended tolerance.
- Unbalance
- Unbalance is another easily missed problem that causes severe damage to our equipment. It can also lead to cracks of the housing itself. If not detected and corrected soon enough it can lead to dangerous catastrophic failure. Unbalance can be easily detected and corrected extending the life of the equipment.
We never have enough time to do things right the first time but always find time to do them again.”
These few issues can be easily detected with properly set-up software. Often, the setup is incorrect and inaccurate. Invalid data is captured in the FFT. Please consult an expert to make certain you are utilizing your condition monitoring software to its fullest potential. Remember… If it’s Critical and Rotates it should be Aligned, Balanced, and Monitored.
by Ana Maria Delgado, CRL