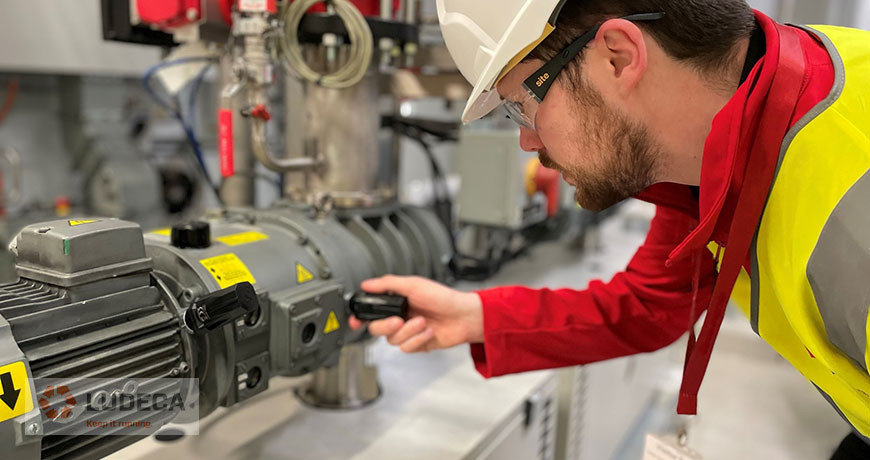
Selecting the appropriate machines for mounting wireless vibration sensors involves a thoughtful process that integrates criticality analysis and considerations of accessibility. Here’s a more detailed breakdown:
Criticality Analysis
Prioritize critical machines by identifying and prioritizing machines critical to your operational processes. These could be equipment with a significant impact on production, safety, or overall system functionality.
Evaluate the potential consequences of failure for each machine. Machines with higher risks and more severe consequences should be given priority for sensor deployment.
Accessibility
For hard-to-reach areas, where traditional wired setups may be impractical, wireless sensors such as the Kappa X offer a clear advantage. Consider places with limited physical access or spaces that pose safety challenges for personnel. Wireless sensors are also ideal for remote locations reducing the need for frequent on-site visits for vibration data collection.
Additionally, in potentially hazardous environments requiring explosion-proof measures, intrinsically safe wireless sensors provide a secure means for gathering both vibration and temperature data.
Historical Data and Maintenance Records
Examine historical data and maintenance records for each machine. If a machine has a history of recurring issues or maintenance needs, it may be a prime candidate for continuous monitoring using wireless vibration sensors.
By combining criticality analysis with considerations of accessibility, you can strategically select machines for wireless vibration sensor deployment. This approach ensures that the chosen machines align with the overall goals of predictive maintenance, providing valuable insights while maintaining operational efficiency.
Filed under:
Vibration Analysis by Alex Nino CRL