Condition Monitoring Expert Tip #1 by Mobius Institute
This tip is sponsored by IMVAC (International Machine Vibration Analysis Conference)
How do you decide which condition monitoring technologies to use?
There are many condition monitoring technologies that we could employ. And within each technology there are sub-technologies. For example, within vibration analysis, we can use high-frequency analysis, spectrum analysis, time waveform analysis, and phase analysis. Within each sub-technology, there are settings we must select. For example, we must set the frequency range when collecting spectra. But which technologies should we use? Which settings are correct? The best way to make those decisions is by understanding the failure modes of the equipment.
If you understand what leads to failure, and what is likely to fail, you can select the most appropriate technologies and settings. You may argue that that is an obvious statement to make. You are probably not using vibration analysis on your steam traps… But after 30 years of experience in vibration analysis, it is common to see that fault conditions a totally missed because of the misapplication of the technology.
It is not necessary to perform a full RCM (reliability-centered maintenance) or FMEA (failure modes effects analysis) to make this determination. A so-called “accelerated RCM” is sufficient to ensure that you make the right decisions.
Special thanks to Mobius Institute for allowing us to share this condition monitoring expert tip with you!
by Ana Maria Delgado, CRL
There are two commonly used testing methods to determine a vertical pump’s natural frequency. The first method is called a startup or coast down. In order to perform this method, a tach signal is required for the speed to be tracked. The pump is started and the amplitude and phase are recorded during start-up and coast down, however, when a pump is started across the line (connected directly to a power source without a drive or soft-start circuit) it is very difficult to use this method. The problem is that when a pump is started across the line it goes from zero rpm to full speed so quickly that there is not enough time to obtain valid data. The coast down method is not normally successful in these cases. When the stop is initiated the pump comes to a complete stop in a very short period of time as the liquid inside the pump column falls back to the wet well acting as a brake. However, start-up and coast-down testing can be performed successfully if a pump is being operated using a VFD (Variable Frequency Drive) as the rate of speed can be controlled.
The other method of determining structural natural frequencies on a vertical pump is to conduct an impact test. This test is more commonly known as a bump test. This test requires that the pump be stopped and impacted using a block of wood or a large hammer that has a soft tip (modal hammer). The bump test provides a response curve that will identify the natural frequency and/or frequencies of the pump. It is recommended that the testing be performed in two separate directions. One direction would be in-line with the pump’s discharge pipe and the other direction should be 90 degrees from the discharge pipe. The two different directions will usually result in two different natural frequencies as the pump’s discharge pipe tends to stiffen the structure. This vibration data can be shown as a higher natural frequency from that direction. The other direction which is 90 degrees from the pump discharge will usually have a lower natural frequency. This is due to the fact that the pump manufacturers typically cut out part of the structure. This allows access to the coupling or seal which also dampens the structure in that direction.
Both of the mentioned methods can assist with discovering the natural frequencies of a pump. Once the frequencies have been identified on the pump; the proper corrections can be made to make certain that the pump is not operating on a resonance frequency.
Learn more about our Condition Monitoring tools
by Dave Leach CRL CMRT CMRP
When monitoring your bearing lubrication with ultrasound, it is important to watch for very high values in your condition indicators (total RMS and Peak values). After applying grease, both values should decrease proportionately. This is a sign the bearing was under-lubricated. If the total RMS value lowers and the peak value stays relatively the same, then the bearing has a mechanical condition that is generating impacts.
by Allan Rienstra - SDT Ultrasound Solutions
Comments that I have heard in all types of industry are “We always have the time or money to do the repair over, but never time or money to do it right”. Many times when equipment fails there is an incredible rush to get the machine back online due to some production requirement. This usually leads to repairs that are inadequate or incomplete. It is important to remember that as long as your lock is on the machine it is not going to go back into service until you remove that lock. It could take as little as an additional 30 minutes to allow the machine to be repaired completely, but instead, the job is rushed and a few weeks or a couple of months later the same machine is being repaired for the same reasons again.
Production controls the purse strings that is a given, but generally, product quality and maintenance cost can be better controlled by allowing for a complete repair, not a partial fix. A couple of examples that come to mind are belt-driven machines. Many repair techs simply roll V-belts on and off for removal or installation. Have you ever noticed a V-belt running upside down? In most cases, it is due to the cords in the backing of the belt being broken. This is usually caused by rolling the belts on or off the sheave. If “power band belts” are used the cost of those belts is usually higher than the sheaves that the belts are running on. It is a paradox that brand new belts will be installed on worn-out sheaves.
When the sheaves are replaced most of the sheaves are affixed to the shaft with a taper lock hub. How many people use an indicator to ensure that the sheaves are square to the shaft and not just tighten the hub with an impact wrench? There are others examples, but hopefully, this drives the point home. Repairs need to be done in a timely fashion in cooperation with production to minimize downtime and reduce any effects on quality.
by Gary James CRL
- Most electrical cabinets are not hermetically sealed. Scan your ultrasound detector around the panel sides and ventholes to detect discharges like arcing, tracking, and corona.
- Not all electrical discharge faults produce heat. Use ultrasound solutions to hear what your infrared camera cannot see.
- Electrical discharge activity is amplified by high humidity. When performing ultrasonic scans at substations make note of the date and weather conditions.
- Ultrasound travels directionally through air compared with an audible sound. When scanning from a distance, therefore, it is important to inspect electrical systems from all sides.
- Corona discharge produces no heat on electrical systems below 240 kV so don’t rely entirely on infrared to find problems.
by Allan Rienstra - SDT Ultrasound Solutions
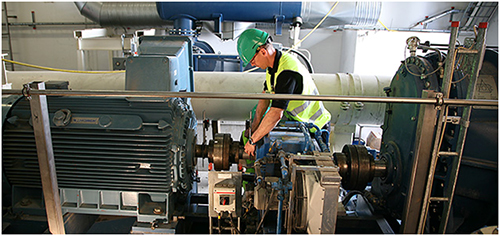
Reposted from EASY-LASER® blog
- FAST AND ACCURATE
Laser alignment can be done ten times faster and much more accurately compared with dial gauges or straight edge methods (depending on the user’s skill). A dial setup will not measure down to 0.001 mm – but a laser can! - QUICK TO SET UP, EASY TO USE, AND HIGHLY RELIABLE
A laser alignment system is quick to set up, easy to use, and much more reliable than old technology. The latter often requires extensive experience and sometimes complicated calculations to be used. For example, fixtures for dial gauges always sag a little, which affects the accuracy of the gauge’s displayed value. This does not occur with laser alignment. - POSSIBILITY TO GENERATE REPORTS WITH RESULTS
With a laser alignment system, it is possible to generate PDF reports directly from the instrument. The computer handles targets and tolerances and makes it easy to interpret the results. The possibility of documenting the results gives better control over the machines and greater assurance. Reports can be generated for “before” and “after” alignment. - A TRUE REPRESENTATION OF MACHINE FRAME DISTORTION
For soft foot issues, regardless of what is going on at the feet, you get a true representation of the movement between the rotating axes of the shafts you are aligning. Dial readings only tell you what’s happening at the feet—not a true representation of soft foot! - THE SPEED AND PRECISION SAVE YOU MONEY
The speed of use and the precision in alignment mean that investing in a laser-based shaft alignment system usually pays for itself within 3-6 months. - A DISCIPLINED AND REPEATABLE PROCESS
Laser alignment systems make the process of measurement and correction much more disciplined and repeatable. Straightedges and dial gauges are not sufficiently accurate for today’s modern machines. Using laser alignment always gives the same results regardless of who takes the measurements. - EASY TO LEARN AND TO USE
You don’t have to be a specialist to get the correct result. With a wireless display unit, you can follow the machine movement with live values at the points where you adjust the machine, not just where the dial gauges are mounted. - EXPAND ALIGNMENTS AND MEASUREMENTS
With the best laser alignment systems you can expand the types of alignments and measurements you can do. You will then be able to take care of all important steps of machine setup, for example, base flatness and twist, and also measure straightness. - POSSIBILITY TO MEASURE WITH A SMALL SHAFT ROTATION
With laser alignment, it is possible to measure even with a small shaft rotation, for example only 70 degrees. This solves the problem when piping and machine parts are in the way preventing a greater rotation. - REDUCED ENERGY CONSUMPTION
Laser alignment allows precise measurements that reduce your energy consumption in the long term. Poorly aligned machines require more energy to achieve the same results than well-aligned ones. Reduced energy consumption is not only good for your electricity bill, but of course also for the environment. - ERROR-FREE AND HIGH-RESOLUTION TECHNOLOGY
Old technology may have too low a resolution to measure accurately enough and may be subject to reading errors or sticking dial hands. Laser alignment systems are based on high-resolution non-contact technology and are free from such errors. - ELIMINATION OF HARDWARE SAG AND SETUP MISTAKES
With laser alignment, you eliminate errors associated with old technologies such as bar sag, substandard dial bar, and mistakes when installing up the indicator clamps.
by Ana Maria Delgado, CRL
First and foremost vibration data setups must be properly configured to allow the correct results to be collected thus allowing the analyst to interpret the vibration data for defects. The defect findings should be presented in a manner that the personnel that is responsible for the repair of the equipment now have the necessary information to perform their intended function. The vibration data alone will not fix anything. A vibration database must have the proper setups, the vibration data must be collected correctly using the appropriate instrument, and analyzed by a properly trained and confident analyst. This allows for the root cause of the problem to be found as opposed to only replacing parts. It is very critical that the correct person becomes the vibration analyst. This person should have the desire and drive to become the best that they can become at that position. The analyst should also have support from upper management to allow them to focus on one job.
With the right people, right tools, and support you will have the meaningful data to drive and sustain valuable results and continuous improvement.
by Gary James CRL
Reposted from EASY-LASER® blog
Are you the type of person who, going by the principle of “We’ve always done it this way, and it’s worked well”, continues to use a ruler or a piece of string to align your sheaves/pulleys? If so, you can definitely save some money, by reading this.
It is a common misconception that it doesn’t matter whether you align your pulleys or not. The belt is flexible, and can handle it, right? And if a belt or sheave becomes worn, it is easy to just replace it. But what you might not be considering is that the cost of energy is greater than the cost of buying new spare parts such as bearings, belts and pulleys. Studies have shown that with correct alignment it is possible to improve the efficiency of your belt drive saving you from 5 to 20% of your energy costs. This can quickly add up to significant amounts, particularly if your enterprise has tens or even hundreds of belt-driven machines.
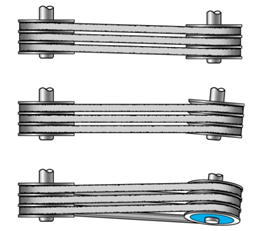
CONSEQUENCES OF GOOD AND POOR BELT ALIGNMENT
Poor alignment or incorrect installation are the most common causes of abnormal wear of sheaves and pulleys. On the other hand, increased productivity, fewer unplanned operational stoppages and reduced energy consumption are the result of well-aligned machines. In the long run, this is also positive for the environment. By aligning your belt-driven machines, you also reduce vibration that harms the machine and adversely affects the working environment.
One consequence of poorly aligned belt drives that is often overlooked is that incorrectly aligned or improperly tensioned belts can result in abnormal temperatures, caused by the belt’s friction against the pulley. Excessively high temperatures will cause the belts to harden, resulting in cracking. A toothed belt can lose teeth, leading to slipping and efficiency loss. Strong heat sources in the vicinity also affect belts negatively. A thermal camera can help to indicate potential abnormal temperatures.
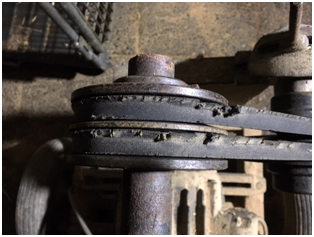
WHERE DO I START?
Many belt manufacturers advocate preventive maintenance in order to avoid unforeseen stoppages. A scheduled operational stoppage is obviously more efficient and less costly than an emergency repair on a failed drive. However, having a maintenance program for your belt drives can also be efficient. There are a number of factors that determine how often you should perform preventive maintenance. Start by classifying your machines in these ways:
- How critical the machines are for your operation.
- The rotational speed of the machine.
- The drive’s impact on the environment.
- The current status of the drive (i.e., condition/quality of the belts and pulleys.)
When you have done this, you will be in a better position to know how to prioritize your maintenance work.
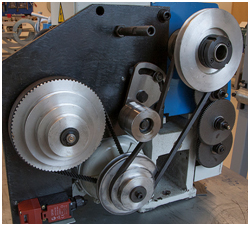
You should also think about the following:
- First and foremost, it is worth thinking about keeping the area around the machine free of dirt and debris, and ensuring that the base is in good condition.
- It is important for the person carrying out the maintenance to have the correct training and equipment to carry out the work satisfactorily. A laser pulley alignment tool is highly recommended.
- Check the machine manufacturer’s specifications regarding how to set up your machine correctly. Write this down so that it is easily accessible the next time maintenance is to be performed. This saves time.
- Check the belt manufacturer’s suggested belt tension values. A spring gauge to measure belt tension is an essential item in the aligner’s toolkit.
- Mixing different belt types or brands is not recommended.
- If the transmission has several belts abreast, all the belts should be replaced together, even if only one is found to be defective.
- Measuring energy consumption before and after alignment is a simple way of verifying that you are now saving money.
- Listen to and look at the machine. If you suspect that anything is abnormal, you should investigate this. You should look out for unusual and abnormal wear or damage.
- Inspections should be performed frequently, perhaps as often as once a month.
- In addition, preventive maintenance should be performed at 6 to 12-month intervals.
- Follow the belt manufacturer’s instructions when replacing belts. Make sure that you also store belts correctly: don’t hang them, coil them flat! (Belts are a perishable product!)
Click here for examples of how much you can save by having your belt drives correctly aligned.
If you are ready to start improving the efficiency of your belts and sheaves, find the tool that best fits your needs.
by Yolanda Lopez
Rotating equipment produces a sound (ultrasonic) signature during operation. This signature can be measured and trended over time. As the machine components begin to fail a change in the ultrasonic signature will occur.
The change in sound level can be used to alarm that could be related to lubrication or bearing damage. A key factor to using an ultrasound tool successfully to determine machine health is collecting the measurements at the same location every time. The first step is to identify a measurement test point for each bearing to be monitored.
One method for data collection is to use a magnet that should be attached to a metal pad epoxied to the measurement location. The use of a magnet and mounting pad will allow for repeatable and consistent data for accurate trending and alarming. If access to measurement locations is restricted, then a sensor can be permanently installed so that measurements can be taken remotely. Ultrasound is an extremely valuable tool that can be used to detect bearing problems with slow-speed applications.
Ultrasound is an important part of any reliability-based condition monitoring program and can provide early warning of mechanical failure. This early warning can lead to reduced downtime and increased plant reliability.
by Dave Leach CRL CMRT CMRP
Strobe lights are an inexpensive tool typically used to determine the operational speed of the equipment. Strobe lights should be readily available to vibration analysts and maintenance mechanics. A strobe can be used as a proactive tool for many things. For example, visual inspection of belt damage (slippage, wear, etc), coupling damage, loose components, and much more can be identified with this handy tool, while the equipment is running. Don’t overlook the value a strobe light can provide beyond just the simple determination of the operational speed of a machine. But keep two things in mind: SAFETY must be first and foremost in your mind at all times when using a strobe light. Since a strobe can appear to “stop motion” on moving components, the temptation to touch the object you are looking at can be strong at times. Avoid this temptation and always stay focused on what you are doing. Also, people prone to epileptic seizures triggered by flashing lights should avoid exposure to a strobe light.
by Trent Phillips CRL CMRP - Novelis
Proper equipment function requires a properly aligned and balanced machine. Allowing a machine to operate with an unbalance condition can result in bearing damage, cracks, loose components, and many other costly maintenance issues. Loose debris can dislodge and impact the balance quality of a machine. Debris buildup on the impellers/blades, and other rotating parts can create unbalance conditions. Before balancing the machine it is very important that the rotating surfaces (blades, etc.) are cleaned of any debris. Removing buildup will help ensure that the machine can be properly balanced and remains in a balanced condition.
by Trent Phillips CRL CMRP - Novelis
To facilitate the initial learning curve, a labeling system was implemented to help technicians collecting data identify bearings that were part of the initial survey. These descriptors were laminated to prolong their life in the unfriendly environment of a typical cement plant. Standard locations for data collection needed to be understood since labels would become difficult or impossible to read over time.
On-the-job training included an understanding that readings collected on the drive motor bearings needed to be collected from the grease fitting on the non-drive end and from the upper portion of the end bell housing on the drive end. On driven equipment bearings, where direct access was possible, the ultrasound readings were to be taken in the horizontal plane directly from the bearing housing. (Note: with ultrasound, it is not necessary to record data from multiple planes on the same bearing). Technicians were trained to take ultrasound readings as close to the bearing as physically possible while respecting personal safety.
This simple label proved important to the integrity of the pilot project to prevent greasing from well-intentioned lubricators.
by Allan Rienstra - SDT Ultrasound Solutions
Hopefully, your company has global, regional and facility resources dedicated full time to reliability initiatives.
These resources are necessary to help ensure improvements in maintenance, equipment run-time, capacity, profits, and much more.
The question you and your organization should be asking is “who is the reliability leader in your organization”?
The answer may seem simple but could be quite surprising when given serious consideration. The answer should be “everyone”. The truth is that most implementation efforts in a facility or company fail. Unfortunately, this is very true for maintenance and reliability improvements. The reason is that not “everyone” is committed to the effort. Sustainable reliability requires understanding and dedication from many different groups within an organization. Supply Side, MRO Stores, Engineering, Procurement, Maintenance, Management, Operations, and Training must all understand the strategic value in reliability efforts and cooperate with each other. Otherwise, failure and unsustainability may be guaranteed.
If the answer to the question is that the “Reliability Engineer” and/or “Global Reliability Leader” are the individuals responsible, then your journey may not be complete. Your organization should have training in place to demonstrate the value and create understanding in all of these groups about reliability. Procedures should be in place to ensure that proper reliability best practices are considered in the design, procurement, installation, operation, and maintenance. Failure to do so will result in increased life cycle costs of the equipment, reduced capacity, and reduced profits.
Remember that your maintenance department cannot overcome poor equipment design, installation, or operation.
by Trent Phillips CRL CMRP - Novelis
Compressed air represents one of the highest utility costs in industrial plants. It’s also one of the most misunderstood; which explains why leaks account for, on average, as much as 35-40% of total demand.
Leaks are often considered an unavoidable cost of business. Many of us simply don’t realize the high cost of compressed air leaks.
Add to that the fact that:
- Leaks don’t present a visible threat to safety
- Leaks don’t make a mess on the floor
- They are invisible
- We can’t hear them over the other noise in the plant
- We don’t need permission to open a 1/4” air line and waste thousands of dollars per year
Remove our misconceptions about the high costs of leaks and we create a huge opportunity to save money, increase environmental sustainability, and drove positive culture change.
Download the Leak Surveyors Handbook to learn more.
by Allan Rienstra - SDT Ultrasound Solutions
Reposted from EASY-LASER® blog
Engineering no doubt spends a lot of time deciding what machines should be specified and how best to set them up for optimal production. And you already know how important shaft alignment is. But there are other ways to make your machine perform even better and last longer. A careful base setup is key if you want to increase the machine’s lifespan and avoid unexpected downtime and other disturbances.
Why you should pay attention to the base setup?
Setting up the base properly is more important than many realize; it is crucial if you want to avoid unnecessary machine stress, and prevent costly problems in the long run.
First, the base has to be strong enough to support the weight of the machine. It also has to be able to withstand a large amount of torque and other loading that the machine produces. In addition, the base also needs to be flat and level.
An uneven or unleveled base can cause all kinds of issues for you: shaft misalignment, pipe strain, distorted machine frames (soft foot), etc. Even a small defect can have significant negative consequences on production.
The machine base – A great investment!
A base that’s flat and level will increase the machine’s lifespan and will save you unexpected downtime with costly repairs. You will also benefit from increased production time and greater efficiency of the machine with reduced energy consumption.
EASY-LASER E720 Alignment/GEO system
Don’t just eyeball the base to see if it’s flat. Use a laser. You might already be familiar with shaft alignment lasers. In this case, you need another kind of measuring tool, such as the Easy-Laser E720 system. The point laser will allow you to optimize both base flatness and shaft alignment. The Easy-Laser D22 (swiveling laser) will help you level the base. No other system on the market offers this type of flexibility.
by Ana Maria Delgado, CRL
As Published by Maintenance Technology Magazine August 2016 issue
Clinging to a single approach that made economic sense for your plant ‘back in the day’ could be an expensive strategy.”
Overall values are the most common measurements and calculations used in vibration analysis. What’s more, some reliability and maintenance programs rely solely on them. The goal is to remove monitored equipment from service once the overall vibration level exceeds a certain threshold. Although this approach would appear to be quite cost-effective, in reality, it frequently isn’t. In fact, overall vibration monitoring can become extremely costly for a facility.
If you are asking yourself questions such as: What should you do once an overall vibration level exceeds your target amplitude and the equipment is removed from service? Who should collect routine vibration data? What other valuable condition-monitoring data might be missing? Or how do you motivate others to take corrective actions? then this article is definitely a must-read.
by Trent Phillips CRL CMRP - Novelis
Reposted from EASY-LASER®
There are many consequences resulting from having a poorly functioning measurement and alignment system. If there is any uncertainty concerning your laser system’s functionality, the measurement and alignment process could take longer than necessary. If the system isn’t in perfect working condition you might need to double-check your results more than once. The wrong alignment of the production equipment caused by incorrect measurements can lead to problems with the machines, as well as compromised product quality. Check calibration of your laser system at the recommended intervals or sooner to guarantee good alignment, peace of mind, and ensure that you always have the latest firmware version installed.
by Ana Maria Delgado, CRL
It can be argued that lubricants are the lifeblood of equipment. It is extremely difficult to assure equipment reliability when lubrication integrity is not maintained. The key is to keep the lubrication system clean, cool, and dry.
According to the Arrhenius Rate Rule, every 18-degree (F) increase in oil temperature in operation reduces oil life by half. Excessive lubrication temperatures can lead to additive depletion, oxidation, varnishing, hazards, corrosion, increased frequency of oil changes, and more. All of this leads to reduced equipment reliability and increased costs.
Reduced operating temperature is one of the many benefits associated with proper machinery alignment. This in turn will help you reduce the operating temperature of the lubricants (lifeblood) within your equipment. Best practice equipment reliability includes proper equipment alignment. Your best practice lubrication efforts should include making sure your equipment is operated within proper alignment tolerances. Doing so will help you maintain the “cool” required to ensure that the lifeblood of your equipment is protected.
by Trent Phillips CRL CMRP - Novelis
Today’s more evolved ultrasound data collectors present results that take reliability practitioners beyond the single decibel. Using only an overall dB value may indicate something inside the machine has changed since the last readings were taken. But it provides no additional insight to determine what type of defect may be present.
Moreover, a single dB only provides a useful trend if the inspector has control of the acquisition time during data collection. Acquisition time needs to be adjusted in concert with the speed of the machine. More time for low-speed applications and less for high. The aim should be to capture a minimum of 2-3 full shaft rotations.
The SDT270 takes inspectors beyond the single decibel by presenting ultrasound data in terms of machine condition. We call them Condition Indicators and there are four (RMS, Max RMS, Peak, and Crest Factor (CF)) and are abbreviated as 4CI. Ultrasound identifies defects in machines when those defects produce one or more of the following phenomena: FRICTION, IMPACTING, or TURBULENCE (FIT).
Some examples:
- A bearing that requires lubrication will present higher levels of friction. Therefore, an RMS danger alarm will be triggered at 8 dB and an RMS/CF alarm when severity increases.
- A bent shaft produces higher levels of friction and therefore presents danger and alert warnings with the RMS condition indicator.
- Electrical defects such as arcing, tracking, and corona are first alarmed with the RMS condition indicator and severely alarmed with Max RMS and CF.
- A faulty steam trap is detected with an elevation in Temperature and Max RMS.
Traditional ultrasound is useful for trending decibel levels that alert us when machine condition changes. Evolved ultrasound goes beyond the single decibel to recruit Condition Indicators that help inspectors determine the type of defect that is creating the alarm. SDT’s Four Condition Indicators demonstrate how ultrasound must be used for both defect alarm and identification.
by Allan Rienstra - SDT Ultrasound Solutions
The maintenance and reliability world is filled with key performance indicators (KPIs). Properly tracking KPIs can be challenging due to difficulties in obtaining accurate data and the time required to obtain them. The key is to pick KPIs that will help you identify and drive the behavior that you need to change right now. As advances are made, additional KPIs can be added which help identify and drive additional behavior changes and improvements.
It is very important to understand that KPIs can lead to false-positive indications and never actually result in value-added or sustainable improvements within your organization. You must understand and address the true root causes behind a deficient KPI and eliminate them.
For example, mean time to repair (MTTR) can be a very good indicator leading to great improvements.
Unfortunately, this indicator can also be harmful if misunderstood or given the wrong improvement focus. What if individuals decide to take deleterious shortcuts to quickly get a machine operational again? MTTR may seem to improve on that machine, but did overall asset health and reliability really improve, in a meaningful way that provides real value back to your organization? These shortcuts may actually lead to additional machinery failures and greater downtime.
MTTR could be an indication that maintenance staff requires training on how to properly repair the machine. Too short and perhaps unwanted shortcuts are being taken. Too long may indicate that excessive time is being wasted hunting for tools or spare parts due to a lack of proper planning and/or kitting. Is a detailed and efficient work plan available, to guide your maintenance staff incorrectly repairing the equipment? MTTR, if properly used and tracked can point you toward areas of substantial improvement.
Never forget to determine and address the root causes of equipment failure. Doing so may eliminate the need to work on the equipment in the first place. Prevention is always the best way to drive sustainable improvements in uptime and capacity.
Beware of driving improvements in KPIs for the wrong reasons. This can lead to a false sense of progress that never brings about real changes and advancements in reliability to your organization. Ensure that you understand the real variables driving the KPIs you have selected. Don’t let your chosen KPIs give you a false sense of improvement!
by Trent Phillips CRL CMRP - Novelis