Many end users have taken laser alignment equipment and “checked” alignments on equipment that has been running satisfactorily, and very often with vibration data that falls well within alarm thresholds, only to find the alignment out of normal alignment tolerances. In this instance, the vibration data should be the determining factor. If the equipment is running well, leave it alone. It would however be a very good practice to keep this alignment data and use it in the future for the intentional misalignment of this particular machine. It is quite possible that the machine had in fact been deliberately misaligned when cold and stopped to compensate for positional changes that occur due to thermal growth or dynamic load shifts.
by Ana Maria Delgado, CRL
Laser shaft alignment has become ubiquitous these days. And for the most part, alignments are very similar from one machine train to another. The user enters the RPM for tolerance evaluation, enters the dimensions of the driver, measures misalignment, and makes corrections. But what happens when an unusual physical configuration exists, as when the foot of the machine is between the flex planes of the coupling? Or the receiver cannot be mounted outboard of the flex planes of such coupling?
Entering a dimension correctly as a negative value can take care of that problem. This will ensure that the corrections at the feet are precise, and the alignment is done properly.
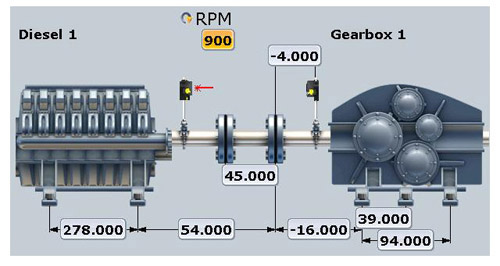
Does your laser alignment system have this crucial capability? Our ROTALIGN® ULTRA laser alignment system does!
by Adam Stredel CRL
Do your analysts use consistent phrases or statements when creating condition monitoring (CM) work orders? It is very important to convey concise and accurate information with each CM work order. Often times misspelled words, inaccurate information, or incomplete maintenance steps are included in work orders. A best practice is to determine the most common findings for a specific CM technology and determine what actions should be taken as a result. For example, if vibration analysis identifies unbalance in a fan, a recommendation should be made to clean the fan prior to attempting to balance it. If a CM technology identifies a failure that requires the machine to be removed, then re-alignment may be necessary before the machine is placed back into service. All of these steps and perhaps additional steps should be conveyed by the CM analyst creating the work order.
Creating consistent and detailed steps for common CM problems will avoid forgetting to convey important information to those doing the work. This will help ensure that best practice maintenance is completed on your equipment, things are not forgotten, misspelled words entered, or other common mistakes made.
by Trent Phillips
When dealing with a gearbox that has 3 feet, there are two possibilities:
a) If the feet are located under the shaft and bearing housings, view the gearbox as a normal 4-foot machine. This will give you inboard and outboard corrections for the feet. The end that has the 2 feet should be corrected evenly, and the 3rd foot should be corrected as per the screen.
b) If the feet are on the sides of the gearbox, or NOT under that shaft or bearing housings, then configure the gearbox as a 6-foot machine. This will give you corrections for the inboard, middle and outboard feet. Correct accordingly at each foot.
by Ana Maria Delgado, CRL
In any alignment situation, one of the most basic principles is rise over run. Think of it as a change in offset over a distance. It is also a way to quantify angles without using degrees. When the laser system measures “angularity”, it expresses it as rise over run, or a change in offset over a distance. This information, along with the dimensions that the user enters is what the system uses to calculate corrections at the feet. That is why it is very important that laser measurements are repeatable and that all dimensions should be accurate to within 1/8 inch. The sensor to coupling dimension is the most critical of these. If the laser measurements are good but the dimensions for the feet are not, any corrections the computer calculates will not work due to the fact that they are “applied” to a different location, not at the actual foot location. If you are making the corrections that the computer says to and your alignment is still off, double check your dimensions.
by Ana Maria Delgado, CRL
In my spare time, I enjoy the hobbies of building bicycles and metalworking. There is something about making things from scratch that satisfies both the kid and engineer in me.
I recently sold a hobby class CNC machine that I purchased about a year ago. It was a capable machine for what it did and the price was MUCH less than the typical Vertical Machine Center (VMC) that you would see in a machine shop. Unfortunately, it didn’t do exactly what I needed. I learned through further education that my machine “should have this capability, must be able to do that, etc.” I also found out that much of the manufacturer’s verbiage such as “step resolution,” “precision,” “computer-controlled,” “complete solution,” and “high quality” was bandied about so much that one would wonder why a machine shop would pay so much more for a quality CNC VMC. Upon talking to other users, I learned more about its shortcomings and what they eventually did: they were now educated and instead invested in machines that actually did what they needed for their applications and delivered on the manufacturer’s promises. Haven’t we all experienced this same situation before when buying cars, TVs, appliances, cell phones, etc.?
Unfortunately, this situation is not isolated to CNC machines and consumer products but extends to all sorts of products – even laser shaft alignment systems. If you make an internet search for laser shaft alignment tools, terms such as “.0001 resolution, laser, high precision, easiest, 3000 points, 60-degree turn, single correction alignments, etc.” are thrown about on websites and it is unfortunate that customers must sort through this and hope they find a laser alignment tool that will truly satisfy the requirements of their reliability program.
How can you make the right decision in buying a laser alignment product? For starters, inform yourself through reliable sources. I would encourage you to talk to other users and get their experiences with the tools. These are people that use shaft alignment for their reliability program. Maybe they have purchased a variety of tools before settling on the right tool that works. Let their experience help save you time in searching for the right product.
I would also encourage you to contact your vendor and ask for a demonstration. Everyone claims to have the best product, but the real proof is that the tool actually works for your reliability program. For example, if you contact us, we have knowledgeable local representatives and an onsite dedicated engineering staff who will gladly visit your facility and answer any questions you may have. We have represented Prüftechnik (the inventors of laser shaft alignment) for 30 years and many of our reps have represented our products for over 25 years. All those years mean that we have the experience, references, and reputation to provide you with the information and resources to make an informed decision.
Buying a laser alignment tool is essential to your reliability program. Its ultimate goal is to reduce the amount of time to do alignments, do them more accurately, and document the results. Doing so will help you accomplish the main goal – improving the reliability of your plant and thereby saving time and money.
by Daus Studenberg CRL
PUMPS & SYSTEMS • August 2012
By James Laxson, Hi-Speed Industrial Services in collaboration with Mike Fitch, LUDECA, Inc.
In May 2010, an electric motor repair service provider in Little Rock, AR, began a condition monitoring program for a new customer. The customer opted for quarterly data collection.
Read the article Pump Train Component Failure, a briefcase history of a component failure in a nominal 1,800 RPM pump train.
by Ana Maria Delgado, CRL
Dial indicators can fluctuate several thousandths; no direct solution to this is available. However, with ROTALIGN® ULTRA, as with the OPTALIGN® SMART and SHAFTALIGN®, a measurement setting known as “Averaging” can be controlled (Figure 1). The averaging feature allows you to control the number of individual data points taken per reading. If there are high vibrations, or positional fluctuations being picked up by the equipment, increasing the averaging can ensure that you obtain a true measurement of the misalignment.
Further data collection analysis can be accomplished after the alignment measurements have been taken by viewing the scatter plot of all individual points/readings using the “Edit Points” feature (Figure 2). With the advanced functionality of ROTALIGN ULTRA, the points with maximum deviation can be found and analyzed (Figure 3). If, for example, one or more points were found to be random, outlying, high vibration peaks, those particular points can be disabled. By disabling the “rogue” points, the Standard Deviation (SD) of the averaged alignment measurement is decreased, thereby giving you an even more accurate representation of the misalignment (Figure 4).
by Ana Maria Delgado, CRL
Problem Overview
A customer approached LUDECA with a machine train alignment consisting of a fan coupled to a fluid drive coupled to a motor. This particular machine train had limited movement/adjustment available (See Figure 1).
Due to the nature and geometry of the machinery, the fan on the left was stationary, and both the fluid coupling and motor were movable machines. Additionally, the fan could not be rotated. With these limitations and constraints, very careful planning was needed.
Solution
Upon arrival at the site, the LUDECA Field Service Engineer and site personnel began to analyze the situation and figure out the most efficient way to align the machine train. Using the advanced functionality of the Rotalign® ULTRA, uncoupled readings were taken across the fan and fluid coupling, and coupled readings were taken across the fluid coupling and motor. The “As Found” results can be seen in Figure 2.
Per the request of the customer, the alignment was to meet “Short-Flex” Tolerance requirements, even though the coupling was in fact a large gear coupling whose flex planes (points of power transmission) were 13 inches apart. Upon performing the horizontal correction of the motor it became bolt-bound, which prevented further movement in the required direction, New readings were taken and the misalignment is shown below in Figure 3.
Due to the Short-Flex tolerance requirement, the motor needed to move further on both the inboard and outboard feet than was possible. To achieve the Short-Flex tolerances would require very tedious corrections, involving additional movement of both the motor and fluid coupling, or in a more extreme case, re-machining of the bolt holes in the motor feet to allow for more movement. The LUDECA Field Service Engineer suggested that Spacer Tolerances be used. With Spacer Tolerances, the large axial distance between flex planes is taken into account in such a way that the angle at each flex plane is examined individually. This can be done by examining these angles directly in mils per inch, or as the projected offsets of the machine centerlines to each flex plane across the distance between them. With the tolerances set to the spacer-type coupling, the results were viewed once again and it was discovered that the alignment was, in fact, within proper tolerances (See Figure 4). By changing the coupling type from Short-Flex to Spacer, what would have been a tedious and time-consuming task was found to be unnecessary, and was instantly resolved by entering the appropriate coupling type, in this case, spacer coupling. The spacer-type coupling takes into consideration the distance between flex planes, whereas short flex-type ignores it.
by Ana Maria Delgado, CRL
TURBOMACHINERY INTERNATIONAL • May/June 2012
Thermal growth, as used in the field of machinery alignment means machine frame expansion resulting from heat generation. The generation of heat, of course, is caused by operational processes and forces. Materials subjected to temperature changes from heat generation will expand by precise amounts defined by their material properties.
In turbomachinery, thermal growth results from the temperature differences occurring between the at-rest and running conditions. Generally speaking, the greater the temperature difference, the greater the thermal growth.
The magnitude of the growth can be calculated from three variables:
?T (temperature difference),
C (coefficient of thermal expansion), and
L (the distance between the shaft centerline and the machine supports).
When machinery begins to generate heat, the temperature difference between the at-rest and running conditions will cause thermal expansion of the machine frame, thereby bringing about the movement of the shaft centerlines.
This can produce changes in the alignment affecting the offset and/or angularity between the two machines’ shafts.
If misalignment beyond permissible tolerances occurs in the running condition, it can be observed from both high vibration and excessive power consumption. Operating machinery that is subject to thermal growth without taking into account its effects will result in a loss of efficiency, performance, and reduction in machine or component life.
Relying on the Original Equipment Manufacturers’ data sheets may not be enough as their calculations are performed on a test unit, under specified operating conditions, loads, and field conditions which may be significantly different from operating conditions in the field. These differences can drastically affect the amount of thermal growth observed on a unit in service.
Quantifying thermal growth accurately on turbomachinery to determine the amount of positional change between the machines requires expertise and/or the employment of measurement systems.
Download our article “Thermal Growth: How to Identify, Quantify and Deal with its Effects on Turbomachinery”
by Ana Maria Delgado, CRL
A contractor from Spokane requested a bore centerline alignment of a vertical hydro turbine in northern Idaho. After receiving more detailed information and visiting the site, it was determined that this task would be possible using a combination of the CENTRALIGN® ULTRA STANDARD (a bore laser alignment system) and the LEVALIGN® laser (a laser for flatness and squareness measurement).
Download the Vertical Turbine Bearing Alignment case study.
by Ana Maria Delgado, CRL
Maintenance departments periodically schedule maintenance checks on their belt- or chain-driven equipment in order to confirm that a good alignment exists between the pulleys or sprockets, especially if evidence of premature wear on the belts or sprocket teeth is detected.
For this task a Dotline Laser, Sheavemaster or Sheavemaster Greenline laser pulley alignment tool is ideal. It indicates misalignment in all three degrees of freedom (axial offset, horizontal angularity, and twist angle) instantly.
Always mount your laser pulley alignment tool on the smaller pulley and the targets on the larger one, for maximum resolution. Ensure that the mounting surfaces (pulley faces) are free of dirt or rust, and don’t forget to verify the proper tension of the belts (or chains) after the alignment.
Download Belt & Chain Storage Best Practices
by Mario Rostran CRL
When setting up your laser alignment system to align machine shafts, it is very convenient to have the right brackets for the job-ready. The ROTALIGN ULTRA and OPTALIGN SMART feature fully assembled Compact Chain Brackets in the carrying case that are ready to go when you are. These can be used on a vast array of shaft or coupling diameters, from ½” to 20″ requiring no optional accessories, except for using a longer chain for the largest diameters.
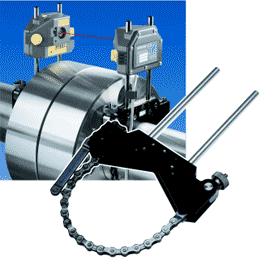
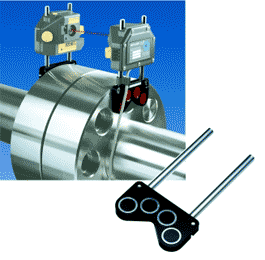
On the rare occasions when the chain brackets won’t fit on the shaft of a particular machine, (such as when there is too little axial clearance between the coupling hub and the bearing housing of the machine, or radial obstructions to rotation interfere), it is perfectly acceptable to mount the fully assembled bracket on the coupling hub, provided that the coupling hub is rigidly attached to the shaft of the machine (i.e., avoid mounting on the floating cover of a gear coupling, say.)
When a suitable radial surface on the rigid coupling hub is not available, or the hub is cone-shaped, it may be better to use the compact Magnetic Bracket System, which mounts to the axial face of the rigid coupling hub, or the Narrow Bracket System which requires only 5/16″ inch axial clearance on the shaft or hub.
For very large couplings, or where radial obstructions to rotation or to line-of-sight exist, consider using Magnetic Coupling Bolt Hole Brackets. These extremely versatile brackets are also useful for mounting to the faces of uncoupled shafts, flywheels, and gearboxes for aligning to bearing bores or stern tubes.
by Mario Rostran CRL
The Associated Builders and Contractors (ABC) announced the winners in its 2012 National Craft Championships competition, held at the association’s EdCon & Expo, April 24-27 in San Antonio.
“ABC is honored to recognize the winners of the National Craft Championships for their high-quality workmanship, technical knowledge and safe work practices,” said 2012 ABC National Chairman Eric Regelin, president of Granix, LLC, Ellicott City, Md. “These craft trainees are the best of the best and show us that there is a bright future ahead for ABC and the U.S. construction industry.”
A field of 127 craft trainees competed for top honors in 12 competitions representing 10 crafts. Competitors first took an intense, two-hour written exam and then competed in daylong hands-on practical performance tests in: residential/commercial carpentry; residential/commercial electrical; commercial/industrial electrical; fire sprinkler; HVAC; insulation; millwright/industrial maintenance mechanic; pipefitting; plumbing; sheet metal; pipe welding;and structural welding.
Congratulations to the winners of the Millwright Competition:
Gold: Kurt Dickinson
Training Sponsor: ABC Maine Chapter/Cianbro Corporation
Employer: Cianbro Corporation
Silver: Harold B. Harris III Training
Sponsor: ABC Pelican Chapter
Employer: Turner Industries Group, LLC
Bronze: Seth Norton Training
Sponsor: ABC Maine Chapter/Cianbro Corporation
Employer: Cianbro Corporation
LUDECA is proud to have sponspored and supported the event with several SHAFTALIGN laser shaft alignment tools for the Millwright competition.
We can’t thank LUDECA enough for all of your help again this year. It was a great event! —Lisa Nardone, Associated Builders and Contractors
by Ana Maria Delgado, CRL
Background
The practice of dowel pinning machinery was originally conceived within the U.S. Navy, well over a century ago.
This innovation was triggered by the need for a solution to the extreme conditions faced onboard naval surface vessels and submarines by directly-coupled rotating machinery with respect to hull and foundation deflection related to changing temperatures and storms at sea, as well as the forces generated by firing munitions (shells and depth charges.) The original concern that resulted in the use of dowel pins was positional security.
Given the fact that on Navy and commercial vessels excess mass is a major concern, the sound engineering practice of designing a base structure to weigh three to five times the mass of the machinery mounted upon it is impractical, resulting in flimsier, more flexible foundations. This is the principal justification for dowel pinning machines in the Navy, and this practice became almost universally adopted.
After World War II, the vast majority of the industrial maintenance workforce in the United States that dealt with rotating machinery was comprised of men who had served in the Navy, as this was the branch of the armed services with the bulk of such machinery and maintenance need. As a result of deeply ingrained Navy tradition and training, the practice of indiscriminately dowel-pinning all rotating machinery filtered out onto dry land installations, even though in most cases there was no longer any technical justification for this practice.
Download our article “Thoughts On Dowel Pins In Machine Feet” including Positional Security: Technical Considerations, Alternative Solutions, and Positional Repeatability.
by Alan Luedeking CRL CMRP
Soft Foot has often been noted as the most inexact science portion of Shaft Alignment. Historically, when people think of Soft Foot, they often want to neglect, ignore, or otherwise do everything possible to not deal with it. This is one of the traps that leads down the path of bad habits, bad alignments, and more problems down the line.
Shaft alignment can be thought of as two things: 1) Aligning the couplings and 2) Checking for and correcting Soft Foot. Soft Foot, in fact, plays so much of a role in shaft alignment, that if one were to analyze the 6-Step Alignment Procedure below, one can see that Soft Foot actually appears in 3 out of the 6 steps. Therefore, Soft Foot can be thought of as half the alignment job.
Overall Alignment Procedure
1. Pre-alignment checks
2. Rough alignment to “eyeball clean” (with bolts loose).
3. Rough soft foot: Loosen all bolts and “fill any obvious gaps”.
4. Initial alignment. Get to within 5 to 15 mils at coupling or less than 20 mils at feet.
5. Final soft foot. All feet less than 2.0
6. Final alignment within tolerances.
Note: Step # 1 includes shim inspection and cleaning of machine supports
What is Soft Foot?
Soft Foot is Machine Frame Distortion.
How does it happen?
Soft Foot can happen from a number of things, including:
• Bent Feet
• Bad Bases (warped, uneven, flimsy)
• Dirt, rust, corrosion under feet
• Excessive number of shims
• And many more…
What should be done about it?
A full and extensive diagnosis should be done on every machine foot to determine whether or not the tightening of that particular bolt is causing machine frame distortion, thereby adding coupling misalignment or machine frame strain. A few helpful tips to remember are:
• Minimize the total number of shims under each machine foot to no more than 4 shims per foot.
• Make sure the area is clean, including machine feet, bases, shim packs, etc.
• Any jacking bolts that may be causing force against the machine frame should be backed off, so as to not interfere with the soft foot check.
• When checking for soft foot, only one machine foot should be loosened at a time, and the deflection or movement at the shaft noted.
With advancements in technology, PRUEFTECHNIK laser alignment tools can help diagnose whether a machine has a soft foot. The newest addition to the PRUEFTECHNIK line of tools, the Rotalign® ULTRA, not only diagnoses the soft foot condition of the entire machine but tells the user exactly how much to shim each foot, in order to correct the soft foot condition.
So the next time someone tries to pass off a bad Soft Foot problem as not being “that bad”, be aware that it is 50% of the alignment. Your machine’s Soft Foot condition should be taken care of because if it has not, neither has your Shaft Alignment.
by Ana Maria Delgado, CRL
There is more to proper shimming of a machine for alignment than meets the eye. There are several things you should keep in mind and look out for.
First and foremost, you should be using high-quality pre-cut slotted stainless steel shims, such as Lawton Precut SS-304 Shims. If you think cutting your own shims by hand out of cheaper rolls of carbon steel or brass shim stock will save you money, you are very much mistaken. For one thing, you will only be able to cut the thinner thicknesses with scissors or shears; thicker thicknesses (over 0.004″) will require the acetylene torch or sawing, which is labor-intensive and presents safety concerns. After you have cut your shims by hand, you must take pains to debur them carefully with a ball-peen hammer and file. All of this costs you the most valuable commodity of all: time. Moreover, the end result will be fewer available shims resulting in less precise alignments. And, if you are cutting shims by hand, don’t forget to budget the time to visit the nurse for a Band-Aid.
Download Best Practices: Machinery Alignment Shimming including:
- Advantages of Precut Stainless Steel Shims
- Number of Shims
- Shimming Technique
- Unusual Circumstances: Step-Shimming
- Chart of Horsepower Ranges and Motor Frame Numbers Associated with the Different Sizes of Shims
- and more.
by Alan Luedeking CRL CMRP
On a recent alignment consultation, we were requested to verify the straightness of a stern tube on an oil tanker. It is critical that the stern tube be bored so that it matches the line of the propulsion shaft that will be passing through the center of it. The reason is that the next operation will involve the hydraulic insertion of Babbitt bearings into the stern tube. It would be a very costly operation to undo this is if it were not done correctly the first time.
Upon arrival, the customer’s engineer on site noted that the surface was just machined, but not prepped for accurate measurement by the removal of burrs and machining marks. He wondered if this would affect our measurement. We told him that it could affect any bore measurement, but some unique features of CENTRALIGN® ULTRA would let us know if it did. CENTRALIGN ULTRA offers the following to perform this job AS-IS:
- Single point bracket –The single point brackets are designed to give extremely accurate readings that are independent of the user’s skill and ability. Springs consistently position the plunger on each point around the bore – accomplishing a more accurate translation of the bore surface to the sensor. The result is a true measurement of out-of-roundness and averaged surface finish.
- Standard Deviation – It takes a minimum of three points on a bore to obtain its center position with tightwire, laser, or optical bore measurements. CENTRALIGN allows for more than three points to be taken. With this, the points can now automatically be fitted to a virtual circle that can reveal not only a center position but also the quality of the measurement. In essence, Standard Deviation lets us know, “Is what we measured round? If so, on average, how round was it?”
If the measurement had a low Standard Deviation, then we would know the bore that was measured was round. If a nick or a burr was accidentally measured or if the surface finish was rough, you would see higher Standard Deviation results. It turns out there was no need for any further surface preparation as CENTRALIGN indicated that the measurements were excellent and the single point bracket had not measured on a nick or bump. Standard Deviation was under 0.5 thousandths and repeatability averaged 0.2 thousandths per measurement. The entire measurement took under 1 hour from arrival to departure of the job location.
by Daus Studenberg CRL
Dial indicators are ubiquitous in shaft alignment; they have been used (and misused) extensively for alignment throughout the industry for many years. In the right hands, a very accurate alignment can be performed with dial indicators. However, even under the best of circumstances, it will be a time-consuming task with many traps and pitfalls for the unwary or the untrained.
Using dial indicators properly for shaft alignment is almost an art form. One key consideration is the measurement setup. What method should be used? The Rim & Face Method? Rim & Reverse Face Method? Reverse Indicator Method? Rim & Two-Face? The Face-Face Distance? Each setup may be appropriate for one situation but not for another. Extensive training is required to make this decision correctly. In addition, some proficiency with algebra and geometry will inevitably be required to make sense of the readings taken and calculate corrective moves for the machines.
Once the proper method has been chosen, initial setup preparations require the millwright to check for sag. Sag (also called bar sag) is the result of gravity acting on the overhung hardware spanning across the coupling that holds the indicator(s). It is always present, and its magnitude and repeatability must be accurately measured and known for the millwright to have any hope of measuring the misalignment accurately.
The effect of bar sag is doubled: When initially zeroed at the top, this radial (rim) indicator is already sagging; when it is rotated 180 degrees, it now sags in the opposite direction, doubling the travel of the indicator.
Over longer spans (such as with spool piece couplings or jackshafts), sag can quickly become unmanageable, forcing the use of alternative compound setup methods. Sag will also affect a face (axial) indicator but to a lesser extent. When bar sag is ignored, the impact on the readings can be very significant, rendering the data obtained misleading, or at worst useless.
Besides sag, field conditions may conspire to bedevil the results. Consider the following:
Vibration and Dial Indicator:
Surrounding running machines may cause vibration to enter the machines you are aligning, making the indicators vibrate as well. Because of the overhung installation of the indicator and its supporting hardware, this vibration tends to be greatly amplified at the indicator itself, to the point where it becomes difficult to read accurately, or even impossible to read at all.
Tilted Dial Indicator:
Space constraints may force you to install the indicator at an angle to the reference surface being measured. This tilting will lead to a significant error in the readings as the movement being measured results in a significantly reduced travel of the indicator stem. The only way in which the travel of the indicator stem can accurately reflect the movement being observed is for it to be mounted perpendicular to the direction of the movement being measured.
Parallax Effect and Reading Error:
If space constraints do not allow you to view the face of your dial indicator squarely, you may misread the indicator by several thousandths of an inch. Also, if the travel of the indicator stem is not observed all the way around, a huge reading error may occur if the needle reversed direction during rotation and the millwright did not notice this. The consequences of such a mistake might be recording a reading as +40 mils when in fact it should be –60 mils! A similar error can occur when reading an indicator with a mirror in order to be able to see it at locations that are inaccessible to the naked eye, or from not noticing that the indicator stem is no longer contacting the reference surface.
Dial Indicator Resolution:
Another concern is the measurement resolution of the dial indicator. If a delicate measurement task is undertaken, such as measuring the effect of machine frame distortion by observing the angular changes at the coupling, it must be remembered that these effects dwindle through mechanical looseness and the fact that the shaft is midway between the feet laterally; thus, when one machine foot is loosened, the effect on the shaft is halved. This, coupled with an insufficient measurement resolution of the indicator may render the reading inadequate to perform a meaningful diagnosis of the distortion condition.
Dial Indicator Hysteresis:
Hysteresis of the indicator may also conspire to reduce the accuracy of your readings. Hysteresis is the friction of the internal moving parts of the indicator mechanism. The best dial indicators use precious jewels in their movements (like fine watches) to keep them from “sticking”. This makes them delicate instruments that must be handled with great care. Dropping a dial indicator or subjecting it to extremes of heat, cold or humidity may exacerbate hysteresis conditions to the point that the indicator becomes inaccurate or inoperative.
End Float (Axial Play):
End float, or shaft end play, can bedevil a face indicator. This is particularly true on machines with journal bearings or sleeve bearings that permit a certain amount of axial play to occur in the shaft as it is rotated. This will play havoc with the accuracy of a face (or axially mounted) indicator. It can only be overcome by rotating the shafts while applying significant thrust load (which is often impracticable) or by means of the Rim & Two-Face Method, whereby two face indicators are mounted on the same setup 180 degrees opposed from one another. When the shafts are turned, end float will affect both face indicators equally and therefore only the difference in their readings is observed, arriving thereby at the true gap difference between them. However, a great disadvantage of this method lies in the fact that an extra indicator is now required to be mounted, which in turn requires full rotational clearance all the way around; in addition, the extra indicator significantly increases the bar sag of the entire setup.
Obstructions to Rotation, Measurement Range, Algebra, and Geometry:
The millwright using dial indicators must be proficient in geometry to understand the meaning of the readings he is obtaining; then, he must also be proficient in algebra to perform the necessary rise over run calculations needed to obtain the corrective moves for the alignment. One alternative is a full rotation of the shafts when obstructions to rotation exist is to rotate the shafts only 180 degrees and extrapolate the fourth (or missing) reading through the mathematical circular validity rule. This requires some mathematical skills of the technician in the field. Moreover, the nature of misalignment is such that an elliptical math model is more accurate than a circular one; however, neither the resolution of the dial indicators nor the math skills of the technicians in the field are equal to the task of applying these models in the calculation of results.
When radial obstructions to rotation exist that do not allow for even a half rotation of the shafts, very few millwrights have the necessary mathematics skills to compute the misalignment conditions and corrections from shaft rotations of less than 180 degrees. Moreover, if misalignment causes the indicator stem to run out of range, it must be repositioned for a fresh range, adding complexity to the calculations, since segments of readings must be “spliced” together. If an indicator bottoms out the entire reading process must be begun again since the initial starting reference position of the indicator has been compromised.
All of this tells us that performing competent shaft alignment with dial indicators is a painstaking and time-consuming task. As we have seen, there are numerous potential pitfalls and conditions that make extensive training and experience a necessity in achieving good results with dial indicators, and an unavoidable expense in downtime in getting the job “done right the first time.”
Is there a better (and faster!) alternative to using dial indicators?
Of course, there is! Laser Shaft Alignment
by Alan Luedeking CRL CMRP
The best alternative to using dial indicators for shaft alignment is to use a good laser alignment system such as the ROTALIGN® ULTRA or OPTALIGN® SMART. All the inherent problems and disadvantages of dial indicators are immediately eliminated. Here’s why:
- Training: Far less training and expertise is required of the millwright to use a laser system proficiently than to use indicators. No algebra or geometry skills are required for the technician to perform excellent alignments since the system performs all necessary calculations automatically. The entire setup, measurement, and correction process can be accomplished in less than half the time required with indicators. This saves downtime and saves money!
- No-Sag: The bracketing and components of the ROTALIGN and OPTALIGN laser systems are carefully designed to have their center of gravity directly between the support posts that hold them. The laser beam itself is weightless and thus no-sag exists with these laser systems. This saves setup time since sag does not have to be measured nor accounted for.
- No effect from End Float: The optical measurement principles used by the ROTALIGN systems render them entirely impervious to the effects of shaft end float, since the axial distance between sensor planes in the receiver is fixed. In the OPTALIGN system end float has no effect on angularity whatsoever due to the optical principles of a roof prism; the effect on the offset is negligible because even at the worst angles typically existent between misaligned machines the impact on the projected offset from the axial play is less than the measurement tolerance, whereas a face indicator is impacted directly by end float by the full magnitude of the axial displacement.
- Vibration mitigation: Even the most severe vibration from surrounding machines presents no problem for three reasons: First, the components are not overhung and therefore do not amplify the vibration. Thus the vibration of the components cannot exceed the amplitude of the vibration itself at the points on the machines where they are mounted. Secondly, the averaging of the readings can be adjusted so that the effect of any vibration on the laser beam is totally negated. Thirdly, the artificial intelligence that is programmed into the firmware of the system fires the laser beam at random intervals so that its pulse rate can never be in phase with any vibration. Thus all of the conditions that can render a dial indicator useless in these circumstances are eliminated.
- No Reading Errors or Parallax Effects: None of these potentially great human errors is possible with the ROTALIGN or OPTALIGN laser systems because all data collection is fully automated.
- No Tilting Error: As long as the laser system components can be securely mounted on the shafts or solid coupling hubs, no error can occur since the only movement registered is that of the beam across the sensor caused by misalignment of the shafts as they are turned. This is true even if the laser, prism, or receiver components are mounted cocked, or tilted with respect to each other!
- No Hysteresis Problem: No hysteresis errors can occur because there are no moving parts in the laser system components that can be affected by environmental conditions or rough handling. In fact, ROTALIGN and OPTALIGN systems are waterproof, shockproof, and dustproof. They can therefore withstand the rigors of use in an industrial environment far better than a delicate dial indicator.
- Measurement Resolution and Obstructions to Rotation: ROTALIGN and OPTALIGN have a measurement resolution of just 1 micron (0.00004″). This together with sophisticated artificial intelligence-based elliptical math models programmed in the firmware means highly accurate shaft alignment results can be obtained with only 70 degrees of shaft rotation, starting anywhere and stopping anywhere. ROTALIGN and OPTALIGN are totally independent of the clock positions that must be arrived at when measuring with indicators. Thus, obstructions to rotation are no longer a problem. The systems’ high resolution also means they are ideally suited to the task of measuring machine frame distortion at the coupling, sparing the millwright the problems and inaccuracies associated with mounting indicators at the machine feet for soft foot measurement. This too saves time and money.
by Alan Luedeking CRL CMRP