Water/Waste Processing Magazine • February 2011
A southeastern US water company has been developing a condition monitoring program with LUDECA as their partner, to monitor their on-surface equipment with VIBSCANNER® and VIBCODE® systems. The current program has provided significant benefits and cost savings by preventing expensive pump and motor failures, as well as optimizing their current maintenance planning and procedures. However, sometimes not all equipment can be monitored using a portable device, either for safety reasons or location. A recent problem arose at the wastewater treatment plant. The facility experiences high flows and because of the small relative space available, they use chemical and aeration treatment processes to meet code and final water approval levels. The flow works by deep tunnels that run beneath the city terminating at a deep pump well 121 feet in depth (37 meters). It is pumped by four submersible pumps to the plant’s inlet. These pumps have caused extreme revenue and capital cost in both repairs and operations.
Download the entire article “Online Condition Monitoring – Monitoring Waste the Easy Way”
by Alex Nino CRL
I recently used an audible recording of a time domain waveform acquired with the VibXpert to help demonstrate the value of the actual “audible” sound of a bearing fault during a recent condition monitoring survey (baseline measurements) of a multistage circulation pump. As we know, the time domain waveform signal is truly the “raw” data of vibration measurements. In this particular case, the frequency domain (FFT plot) measurements showed very low vibration amplitude levels and the determining factor for the early detection of the bearing fault was primarily the use of time domain waveform signals. Frequency domain (spectra plots) along with time domain (waveform plots) was presented to the customer for their review. Also, an “audible” recording of the time domain waveform signal was presented to the customer for review with very favorable results. The customer conveyed that the “actual” bearing impacting sound represented by the time waveform recording was easier to comprehend then reviewing the time signal plot. The customer stated that he felt like he was getting a combination of “ultra sound” technology along with vibration analysis and was very satisfied with the results.The VibXpert® data collectors allow you to listen to the raw data collected on equipment. The OMNITREND® software allows time domain waveform data to be played back in the comfort of your office. In certain situations these capabilities can be a great analysis tool. I have successfully used these capabilities in the past to capture “random” impacting events of ultra-slow operating equipment such as gear reducers on conveyor drives and building structure movement in connection with sensitive types of hospital equipment. Bottom line, I am planning on utilizing these capabilities much more in the future for illustrating time domain waveform signals to my customers. —Ray Wonderly with ADVANCED MAINTENANCE TECHNOLOGIES – http://www.amt-vibration.com/
by Ana Maria Delgado, CRL
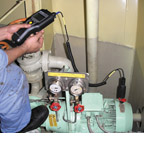
by Ana Maria Delgado, CRL
- Functionality: Do the Predictive Maintenance (PdM) tools you are considering have the ability to make all the measurements required by your physical asset management strategy? Are displays easy to see and interpret? Are the tools easy to learn and easy to use? Learn about our PdM tools. For Software, can it interface with your CMMS system? Can you import data from other systems such as oil data? Learn about our OMNITREND software.
- Durability: Will the tools hold up to your plant’s environment? Are they rugged enough for multiple users? IP ratings such as water–, dust– and shockproof are very important when dealing with industrial tools.
- Service: Will your vendor be available to answer questions or address problems should they arise? What is the vendor’s reputation for customer service? If you have a problem with a tool how soon can you expect a “loaner” until yours is repaired? Are the tools repaired and/or calibrated locally? Learn about LUDECA Repair and Calibration.
- Training: What are the training costs associated with learning how to use the tools? Is training included with the purchase? What training resources are available? Learn about LUDECA Training.
- Support: What level of support do you need? Does the vendor have a call-in tech support center, is it free or paid? Will the yearly costs of maintenance agreements make the tools considerably more expensive than competitors’ tools having similar capabilities? Do they offer free updates? Learn about LUDECA Technical Support.
by Bill Hillman CMRP
The LUDECA Condition Monitoring team just completed a seminar on Modal and ODS techniques with Tony DeMatteo of 4X Diagnostics LLC. The seminar was highly successful and participants came from as far as England to attend. Everyone involved in vibration analysis can benefit from phase analysis. Operational Deflection Shape (ODS) is a software-based enhancement of phase analysis and can be used to analyze the vibratory motion of rotating equipment and structures. ODS is a non-intrusive test that can be completed during the normal operation of a machine. A computer-generated model of a machine, structure, etc is animated with the collected data. This process can be used to prove or disprove theories about failure modes in equipment.
The VibXpert® data collector can be easily used to collect this type of data. The data is collected with the VibXpert and imported into the computer-generated model of the machine or structure for animation and analysis. The new VibXpert II data collector was used in the class to demonstrate the process and power of ODS measurements. Everyone was amazed at how fast this data can be collected with the VibXpert II versus other instruments currently available.
by Trent Phillips
Problem: In a number of real-world applications the speed of a machine cannot be held to a fixed RPM while vibration data is collected.
Solution: The order tracking capability of the VIBXPERT® allows accurate data collection on machines that experience constant speed changes during data acquisition.Applications such as a winder that spools paper coming off the end of a paper machine, by its design continuously decrease in RPM as the diameter of the paper accumulated on the winder increases. Other applications such as a pump that feeds a production process may be required to continuously change speed as the process demand dynamically changes. A spectrum collected during an RPM change will result in smeared and skewed data. During the spectrum measurement process a digitized time waveform of the vibration is collected. The time waveform is collected for enough time to gather repeated cycles of vibration. The FFT process converts the waveform into a spectrum that displays vibration amplitude versus frequency. If the speed of the machine changes during the waveform collection process the peaks generated in the waveform will not be evenly spaced. The resulting spectrum will have vibration peaks widened or smeared and frequency information from low frequency to high frequency that is frequency shifted or skewed. The resulting spectrum data taken from a machine whose speed is changing is most often unusable. In this changing speed scenario if frequency peaks are displayed in the spectrum both the frequency and amplitude will be inaccurate at best. Order Tracking Spectrums allows one to successfully collect spectrum data from a machine that is continuously changing speed. The resulting spectrum amplitudes will be accurate and the frequencies will be displayed in orders of running speed. The collection process requires a tachometer to track the machine’s speed as the time waveform data is acquired. As the equipment speed changes during the measurement process, the start of the actual measurement has to be synchronized from average to average. The number of averages is user selectable. Otherwise, the 1× on one average will not be the 1× on the next average, etc., for the measurement. This results in the same peak showing up in multiple places or being merged with other peaks. This can create analysis havoc. Order tracking results in an accurate spectrum with no data skewing or smearing.
Setting Up Order Tracking Spectrums
There are 5 preset Order Tracking Spectrum setups in OMNITREND®. To view these setups in OMNITREND simply select the menu item <Tools> then <SetupManager> from the drop-down menu. Measurement setups 260 through 264 are examples of Order Tracking Spectrums. The preset Order Tracking Spectrums are available in 5 different units of measure. Like all preset measurements in OMNITREND, these are fixed and cannot be changed. If the preset measurements are not suitable for your application, they may be modified per the following instructions:1) From the <Setup Manager> window, highlight and right mouse click on the Order Tracking Spectrum you are interested in modifying.
2) Click on <Duplicate Setup>
3) An identical measurement will be created and show up at the bottom of the setup manager list.
4) The spectrum parameters of this newly created spectrum may now be customized to better fit your needs. Once you have finalized your Order Tracking Spectrum setups we simply add them to a Measurement Location on a Machine in the equipment database or in the Template Editor. The Machine can then be downloaded to your VIBXPERT data collector as part of a route or as a machine template. At the present time, Order Tracking Spectrums are not available via the Multi-Mode area of the VIBXPERT.
Collecting Order Tracking Spectrums
When collecting Order Tracking Spectrums the appropriate accelerometer and tachometer are required per the measurement setup in OMNITREND. The tachometer must be aimed at a speed reference such as reflective tape mounted on the turning shaft. When the machine is running, the RPM may change while you are taking the measurement.
To the left is a spectrum taken as the speed constantly changed between 1775 RPM and 910 RPM. Notice the waveform time units are recorded as the number of rotations. The spectrum frequency units are orders of running speed. The lower half of the display can be changed to list the maximum 10 amplitudes in the spectrum. Toggle to the lower screen by pressing the F key and then select the peak you would like to see. In the spectrum, the cursor will jump to the corresponding frequency. In OMNITREND the data is equally simple to view and analyze.
by Ana Maria Delgado, CRL
www.facilitiesnet.com • November 2010
Many manufacturing facilities use vibration analysis to detect early signs of machine failure, allowing technicians to repair or replace machinery before a catastrophic failure occurs. All rotating equipment vibrates, but as components begin to fail or reach the end of their serviceable life, they begin to vibrate more and in unique ways. Ongoing monitoring of equipment allows technicians to identify these indicators of wear and future damage well before the damage becomes a total failure. When technicians use condition monitoring correctly, it can result in significant cost savings compared to traditional maintenance approaches. In traditional maintenance approaches using preventive maintenance, technicians would replace these faulty components on a fixed schedule. In a reactive-maintenance scenario, technicians would repair or replace these components only after they have reached total failure.
Read the entire article Vibration Analysis Avoids Equipment Failure by Dave Bertolini, People and Processes, Inc.
by Ana Maria Delgado, CRL
Defects occur at specific frequencies in relation to the running speed of the equipment. Most vibration analysis software will allow these specific frequencies (bands) to be measured and trended over time. Trending this information will help identify problems as they occur in your equipment. This results in more accurate analysis of equipment problems that will help determine the severity and repair urgency of the problems identified.
For example, if the vibration trend is increasing slowly, then the failure may not be progressing rapidly. However, a sharp increase in a specific vibration trend over time indicates that a defect may have developed and failure is more imminent.
by Trent Phillips
We often hear about the need to acquire vibration measurements at precisely the same location each time we measure a point. Why is this important? In order for vibration measurements to be trendable they must be closely repeatable, and we need to eliminate measurement error. With high-frequency measurements, the vibration attenuates rapidly as it travels away from its source. The author has seen readings vary by as much as 50% when the collection transducer was moved by as little as ¼ inch. If the transducer is not placed in the same location, the trended data will show an error that may be mistaken for a change in machine condition. When the collection point is different, the transmission path is either longer or shorter. This affects the amount of energy perceived by the transducer. Standing waves also exist in vibrating machinery. The transducer may sometimes be located at a nodal point of one of these waves; and if care isn’t taken in transducer placement, the next measurement may be at an anti-node. This is more apparent in larger machines because of the amount of surface area available for standing wave formation. There are several ways to precisely mark data points for measurement with a magnet-mounted transducer. Paint, glue-on-pads, stud-mounted pads, machined surfaces, and dimples made by a small drill bit are all used with success. Best of all are permanently mounted coded attachment studs (such as VIBCODE®) that guarantee precise re-placement of the transducer every time, at the same location, angle, and pressure. Regardless of the method employed, it is important to always precisely identify data collection points.
by Bill Hillman CMRP
Reliable Plant • October 2010
Vibration analysis is mostly a learned skill. It is based 70 percent on experience and 30 percent on classroom training and self-study. It takes years to become a confident and competent vibration analyst. When the analysis is wrong, the recommendations for repair also will be incorrect. No vibration analyst wants to make the wrong call. In this business, credibility is gained in small steps and lost in large chunks. A vibration sensor placed on a bearing housing and connected to a vibration analyzer provides time, frequency, and amplitude information in the form of a waveform and a spectrum. This data is the foundation for vibration analysis. It contains the signatures of nearly all mechanical and electrical defects present on the machine. The vibration analysis process involves determining the vibration severity, identifying frequencies and patterns, associating the peaks and patterns with mechanical or electrical components, forming conclusions, and, if necessary, making recommendations for repair. Everybody involved in vibration analysis knows that analyzing vibration is not easy or automated. Have you ever wondered why?
by Tony DeMatteo
The ROTALIGN® ULTRA VIBRATION ACCEPTANCE CHECK works in combination with the VIBTOOL® vibration meter to measure vibration levels according to ISO 10816-3 international standards. The RMS velocity value is wirelessly transferred and stored back onto the ROTALIGN ULTRA computer where the result is instantly evaluated against the machine classification threshold. This fulfills the recommendation of the acceptance check after installation of rotating machinery or any alignment job, ensuring that machines run without restrictions. The VIBTOOL vibration meter can measure the following parameters: Vibration Severity, Bearing Condition, Temperature, RPM, and Pump Cavitation. More information about the new ROTALIGN ULTRA VIBRATION ACCEPTANCE CHECK
by Ana Maria Delgado, CRL
Many vibration programs fail because they become too complicated. Too much data can sometimes become more confusing than too little data. Many potential machinery problems can be eliminated with the analysis if one keeps in mind several simple concepts:
1. Vibration units such as acceleration are more sensitive to high frequencies than low frequencies.
2. Vibration units such as displacement are more sensitive to low frequencies than high frequencies.
3. Velocity units are evenly sensitive between about 60 CPM to 60, 000 CPM.
4. High-frequency vibration does not travel far and degrades rapidly through metal seams.
5. In general the closer your measurement is to the source of the vibration the higher the amplitude will be.
These differences can be used to zero in on machine faults.
Example: Take a generic 100 HP motor. If an outboard rolling element bearing begins to fail because of a lack of lubrication the first indicator is high-frequency ringing from the bearing. This is characterized by a large increase in acceleration amplitude and a small to no increase in velocity or displacement. Now you have identified that there is a high-frequency problem and not a low-frequency mechanical problem. You can eliminate low-frequency sources such as looseness, unbalance, or misalignment. What is the most likely source of high-frequency vibration on the back end of a motor? Probably a bearing or shaft or rotor rub. Now you can apply a simple test. Grease the bearing and see if the acceleration returns to normal. If it does, you have nailed the problem without knowing the bearing frequencies or even taking a spectrum. Come back the next day and see if the acceleration is back up. If it is, you either have a lubrication problem with contamination or a loss of grease, a damaged bearing, or both.
While not perfect, understanding the behavior of vibration units combined with a mechanical understanding of machinery can help you quickly identify machinery problems.
by Ana Maria Delgado, CRL
A key feature of online machine condition monitoring systems is the automatic and immediate notification of system operators or service personnel. Technicians notified by email or SMS of increases in damage are able to react without delay. Today’s Internet is basically a global communications network at our finger-Technology tips. What, then, could be more obvious than taking advantage of the Internet for the communication requirements of condition monitoring systems. Just imagine: The monitoring system automatically sends you an eMail when condition deterioration sets in — along with all of the information you require for damage analysis. Thanks to the capability of today’s wireless communication networks, the service engineer responsible will be notified immediately, regardless of where in the world he may be at that moment. PRUEFTECHNIK online condition monitoring systems like the VIBROWEB® have already been equipped with these new functions and take advantage of the new web technology.eMail – how does it work?
One of the most important Internet applications is eMail or Mail for short. The fact that Mail is not restricted to letters or texts, but can also be used to transmit files of any type is of particular significance. Unlike other Internet applications such as WWW, FTP, or Telnet, the Mail system does not require a direct connection between sender and receiver. Consequently, the receiver and sender computers do not have to be online at the same time. The Mail system is based on the concept of intermediate mail routers that receive and forward messages. Generally, the sender first directs the message to the Mail router of the Internet provider using suitable Mail software capable of the so-called SMTP protocol. SMTP stands for Simple Mail Transfer Protocol and defines the transmission of messages both by the message sender and between Mail routers. A message is passed from one Mail router to the next until it reaches the router responsible for the mailbox of the receiver. The first Mail router to accept the mail from the sender functions as the Mail gateway. The Mail router responsible for the receiver mailbox functions as the Mail Server. Once it has reached the Mail server mailbox, the message can be transported to the receiver’s target computer. For this to happen, the receiver must retrieve the Mail from the Mail server. This not only has the advantage that you can retrieve your Mail whenever you want, but you can also do so from any computer. Regardless of where you are, if you have Internet access and appropriate software you can access your mailbox at any time. The POP protocol is used for this purpose (Post Office Protocol). The user PC must have a suitable Mail program that registers with the Mail server by providing a user name and password and that queries whether there is any mail. The user PC is referred to as the Mail client. Any available Mails are listed and can be downloaded individually by the Mail client via POP.
SMS notification
Mail servers can provide services that supplement the automatic notification system by sending an SMS message to the receiver’s cell phone when an incoming Mail arrives.
eMails and condition monitoring
In condition monitoring practice, the vibration condition is evaluated using the overall vibration level or alarm masks for frequency-selective monitoring. If the PRUEFTECHNIK system detects that the limiting value has been exceeded, it can automatically send an eMail via the Internet or Intranet. The receiver obtains a clear text message containing the location, date, time, and cause of alarm. The information (time or frequency record) when the damage occurred is attached to the eMail. For additional analysis, the maintenance technician responsible logs into the Internet or Intranet and analyses the system at “local telephone rates” — without travel costs!
by Mickey Harp CRL
Thank you for attending our Webinar on Effective Defect Analysis: Maximizing your Vibration Setup by Mitch Stansloski, Ph.D., PE – Pioneer Engineering
If you missed our Webinar, you can view it on demand at any time.
We hope that you found your time with us to be informative and interesting. Here are the answers to your questions:
Q: Does the Nyquist sampling theorem come into play with your analysis?
A: The Nyquist Sampling Theorem states that there must be at least two samples per cycle in order to prevent aliasing. If less than two samples per cycle are collected, false low frequencies develop. In practice, the sampling frequency is set to 2.56 times the maximum frequency desired or higher for some devices. Some devices may sample at a higher rate to provide more detail on the data being acquired. This additional data can increase the accuracy of the measurements and calculations as a result.
Q: Does vibration help with hydraulic pump problems?
A: Yep! For the sliding vane type or gear type, the pumping frequency is the number of vanes or gear teeth multiplied by the running speed.
Q: For collecting data on shovels, that run 24/7, would you still follow the interval settings that you presented, or is there a different method to use?
A: Since these are so critical and have such massive loads, I would set the intervals closer than recommended until experience dictated otherwise.
Q: For resolution, the question is 2 Hz to 1.23 Hz acceptable for how the LUDECA signal processing works? In regards to an envelope-bearing defection, do you recommend the high pass to low pass filters to be no more of a difference of 2 to 4 kHz?
A: Not sure I understand the first part of this question. For envelope bearing detection, I would set one to find stage one bearing defects. This would put the filters at 5kHz to 40 or 50kHz. I would set another to find stage two bearing defects (bearing resonances). This would make the filters at 500 Hz to 5kHz.
Q: For resolution, in regards to delta F value to stay between 2 Hz to 1.23hz, this value is f max divided by # lines?
A: Resolution is the frequency range divided by the number of lines.
Q: Looking at a reduction gearcase, wouldn’t the slower output with fewer CPM’s need more averages in order to get a better sampling rate verse the high-speed input which is turning faster and would require fewer averages?
A: The number of averages won’t affect the sampling rate. In general, we recommend more averages for higher frequency ranges. But, you may still want a few more averages for the output of a gearbox since there are many transients that are low frequency. A faster turning shaft wouldn’t require fewer averages.
Q: How would you develop a collection interval with varying loads?
A: Choose the worst caseload, as a function of load and duty cycle.
Q: How did you calculate the belt frequency, please?
A: Belt Freq = Input Speed x pi x Sheave Diameter / Belt Length
Q: How do I determine the monitoring cycle based on load?
A: The bearing L10 life equation does show that the life is inversely proportional to the load cubed. So, as load exceeds recommend, collection intervals should dramatically shorten.
Q: How do you ensure adequate resolution on a time waveform?
A: Inadequate resolution on a time waveform will cause erroneous low amplitudes. Keep improving the resolution until the amplitudes are maximum and repeatable.
Q: How do you find the load on a particular machine…Is there a formula?
A: Converting the current draw to horsepower is likely the easiest way.
Q: How do you set up the proper resolution? What parameters do you use to decide what resolution to use?
A: If using a Hanning window, the resolution should be set so that it is 1/3 of the smallest peak separation needed to correctly distinguish between defect frequencies.
Q: How many averages do you recommend for vibration data collection?
A: A rule of thumb is to start at 4 averages with a frequency range of 120,000 CPM and then go up or down from there.
Q: What is a good Fmin setting?
A: If collecting a velocity spectrum using an accelerometer for collection, the Fmin should eliminate the integration error found in the first frequency bin. So, the Fmin should filter at least the first bin.
Q: What’s the best way to deal with variable speed?
A: Orders based will work if the speeds are variable but don’t change constantly. In addition, multi-level alarms based on running speed could be used. For machines whose speed varies constantly, order tracking is required in order to obtain a clear spectrum.
Q: Will it not be messy to have a number of frequency range for different types of equipment is the same route of measurement?
A: The data collector doesn’t care how you’ve set up your collection specification. And, neither does your trending software, Better to have a more detailed database and valuable data than one that is simple but ineffective.
by Mitch Stansloski PhD PE
Reliable Plant, August 2010
Ah, to be able to predict the winning numbers in a lottery – who hasn’t had that dream! Life would be so easy and carefree with a crystal ball. And, would not your maintenance job be so much simpler if you could just identify machine damage in time and predict the point at which repairs really become necessary? According to DIN 31051, condition-oriented maintenance is not limited to inspection, servicing, determination of the machine condition, and maintenance schedule. It also encompasses predicting the length of service life remaining for machines and systems. This means it is not always necessary to replace a rolling bearing when an inspection measurement reveals inner raceway frequencies. This article describes how it was possible to keep a damaged bearing running for several months until the scheduled annual outage came around – naturally under close observation. Periodic measurements had shown that there had only been a slight change in the envelope spectrum. But one thing at a time …
Read the entire article Vibration analysis is like winning the lottery
by Mickey Harp CRL
Pumps & Systems, August 2010
Frequency analysis is an important method of vibration analysis. It provides information on vibration sources and helps identify those components in the vibration signal that are often small, but nevertheless important, for diagnosis. Each vibration can be attributed to a particular excitation source or machine part.
Read the entire article: Basic Rules for Measuring Frequency Spectra
by Mickey Harp CRL
The following situation occurred at a Municipal Power Plant. During a planned outage, the on-site team was utilizing a Rotalign® Pro with Boralign® to assess the position of the bearing bores after the removal of the rotor on an Allis Chalmers power generation steam turbine. The results were varying far more than normal and the customer wanted to understand why. I was called in to make sure there were no errors in the use of the Boralign system. The tool was being used properly and there were no problems with the tooling. The customer had already set the unit up on a surface plate and established that there was no appreciable drift with the tool. I suspected excessive vibration, so I used my Vibscanner® to measure overall vibration in displacement. No significant level of vibration could be detected; certainly not enough energy to cause the level of non-repeatability they had been observing in the readings. I thought if the movement of the lower shells had a very low frequency that was too slow to measure utilizing traditional vibration sensors and methods, I might be able to measure it with the Rotalign Pro Straightness program. Both the laser and receiver were mounted on standard magnetic dial stands with brackets that are part of the Straightness hardware set. A series of points were established on the lower shells to measure between, both along the rotational axis and from side to side. Setting the Rotalign Pro Straightness program to the shortest sample time and observing the X-axis values over a 2 to 4-minute period, I was actually able to see a very slow movement between various points on the lower shells. While some areas of the lower shells were reasonably stable, there was movement between some points that was as much as .024”, but at a very low CPM. While this process was somewhat like ODS, there was no real-time phase data, so I could not tell how the various points were moving relative to each other. It was still very helpful to the rotating engineer to understand how much the various areas were moving. Better yet, with a fairly simple program and only 6 hours invested in collecting the data, the rotating engineer had a good idea of the magnitude of the problem.
by Keith Van Hentenryck
LUDECA, INC. introduces VIBXPERT® II, the latest addition to the PRUEFTECHNIK family of portable route-based vibration data collectors. VIBXPERT II is rugged and lightweight —weighing only 2-1/2 pounds! It combines the advantages of a rapid processor with a brilliant energy-efficient color VGA display. Enhanced with a Fmax of 51KHz and up to 102, 400 Lines of Resolution, all machinery problems can be captured and easily analyzed on the VIBXPERT II large color screen. The VIBXPERT II Basic platform is a 1-channel device that can be upgraded at any time to 2 individually configured channels via a special passcode —user-upgradable and does not require hardware changes. All forms of machine vibrations, bearing conditions, process data, and visual inspection information can be collected and stored on the expandable Compact Flash Card (up to 8 gigabytes) for report generation or for later transfer to the powerful OMNITREND® software for further analysis, reporting and archiving. The VIBXPERT vibration analyzer provides an easy-to-use icon-driven platform that offers comprehensive analysis functionality for the diagnosis of simple or very complex vibration problems. Capabilities include order spectrum, phase, cepstrum, cross-channel phase, orbits, run-up, and coast-down measurements, bump test, negative averaging, and more. Analysis tools, including various cursor types, machine-specific frequency markers, signal post-processing, and extensive bearing databases are included for evaluating each spectrum. Alarm notifications based on ISO standards or user-defined standards are visually identified with the aid of colored LEDs.The VIBXPERT II features modular functionality including dynamic field balancing, extended time waveform recording, transient data capture, UFF file export, Modal/ODS support, and more.
by Ana Maria Delgado, CRL
How fast is the data collection speed of your vibration data collector? You may feel that this is not an important characteristic. Does it really matter if a data collector is one or two seconds faster-acquiring data versus another? Data collection speed is very important and should be taken into consideration by your facility management and Condition Monitoring Group. For example, consider a vibration monitoring program that monitors 1000 machine trains per month with 10 measurement points per machine train. If a vibration data collector requires 8 seconds to acquire data for each measurement point, then it would necessitate 22 hours of real data collection time (this does not include time moving between each machine, reporting time or etc). Does a second really make a difference? A data collector that is one second faster acquiring the same data will result in 3 hours per month saved or almost one full man week per year. If the data collector is 3 seconds faster in acquiring the same data, then the time savings are more substantial. A savings of 3 seconds per measurement point will result in a savings of 2.5 man-weeks per year. Multiply the time savings by your labor cost per hour and the savings could be very important to your facility. The savings may surprise you!
Take a look at our new VIBXPERT II analyzer featuring a crisp color display, fast data acquisition, and powerful vibration diagnostics tools.
by Trent Phillips
Successfully persuading your management team about the importance of predictive maintenance requires a certain mindset, one that embraces the ideology that any failure in selling predictive maintenance lies within your selling techniques and not the management team. Success will simply depend on developing the proper selling methods. You are more likely to have success if you show management why they, not you, need predictive maintenance in the company. We have always heard that managers speak the language of dollars. This is true.
Attempt to avoid all technical reasons for justifying PDM and make good arguments based on savings and profitability. Reduced energy consumption, increased uptime, longer machine life, increased machine reliability, and improved products are just a few in a long list of items that will result from good PDM. However, just stating these items will not be very persuasive in your selling attempts. You must show how these benefits relate specifically to applications in your company and present dollar figures calculating the value added by the implementation of PDM technologies. Any data included with the dollar figures should be simple and easy to understand for a non-technical person. Trend plots, bar graphs, or pie charts are effective visual displays of such information. Your report should be concise but lengthy enough to convey relevant information. Brevity usually works best. If you don’t succeed on the first try, be persistent and improve your selling techniques. Remember, the fault lies in your methods and not with the management team. Luck is not a requirement for success. Only the proper arguments are required. Once the correct selling strategy is found, success is sure to follow.
by Bill Hillman CMRP