Soft Foot has often been noted as the most inexact science portion of Shaft Alignment. Historically, when people think of Soft Foot, they often want to neglect, ignore, or otherwise do everything possible to not deal with it. This is one of the traps that leads down the path of bad habits, bad alignments, and more problems down the line.
Shaft alignment can be thought of as two things: 1) Aligning the couplings and 2) Checking for and correcting Soft Foot. Soft Foot, in fact, plays so much of a role in shaft alignment, that if one were to analyze the 6-Step Alignment Procedure below, one can see that Soft Foot actually appears in 3 out of the 6 steps. Therefore, Soft Foot can be thought of as half the alignment job.
Overall Alignment Procedure
1. Pre-alignment checks
2. Rough alignment to “eyeball clean” (with bolts loose).
3. Rough soft foot: Loosen all bolts and “fill any obvious gaps”.
4. Initial alignment. Get to within 5 to 15 mils at coupling or less than 20 mils at feet.
5. Final soft foot. All feet less than 2.0
6. Final alignment within tolerances.
Note: Step # 1 includes shim inspection and cleaning of machine supports
What is Soft Foot?
Soft Foot is Machine Frame Distortion.
How does it happen?
Soft Foot can happen from a number of things, including:
• Bent Feet
• Bad Bases (warped, uneven, flimsy)
• Dirt, rust, corrosion under feet
• Excessive number of shims
• And many more…
What should be done about it?
A full and extensive diagnosis should be done on every machine foot to determine whether or not the tightening of that particular bolt is causing machine frame distortion, thereby adding coupling misalignment or machine frame strain. A few helpful tips to remember are:
• Minimize the total number of shims under each machine foot to no more than 4 shims per foot.
• Make sure the area is clean, including machine feet, bases, shim packs, etc.
• Any jacking bolts that may be causing force against the machine frame should be backed off, so as to not interfere with the soft foot check.
• When checking for soft foot, only one machine foot should be loosened at a time, and the deflection or movement at the shaft noted.
With advancements in technology, PRUEFTECHNIK laser alignment tools can help diagnose whether a machine has a soft foot. The newest addition to the PRUEFTECHNIK line of tools, the Rotalign® ULTRA, not only diagnoses the soft foot condition of the entire machine but tells the user exactly how much to shim each foot, in order to correct the soft foot condition.
So the next time someone tries to pass off a bad Soft Foot problem as not being “that bad”, be aware that it is 50% of the alignment. Your machine’s Soft Foot condition should be taken care of because if it has not, neither has your Shaft Alignment.
by Ana Maria Delgado, CRL
By Daus Studenberg – Applications Engineer
There are certain cases where it is necessary to make sure that two machines have a considerable amount of parallel radial offset. Such machines are usually coupled by a cardan shaft where more than 4-6 degrees of angle exists between the cardan coupling and the machines. Once the offset is established, it is important to ensure the machines are parallel to each other. If angular misalignment exists (i.e. the machines are not exactly parallel to each other) a rapid change in the shaft RPM will result during operation, as well as an uneven bearing loading, which could shorten the life of the machine.
A special cardan bracket was developed specifically for this application. Its main function is to directly translate the axis of rotation of one machine to the axis of rotation of the other machine.
With the bracket installed, a simple shaft alignment occurs using an uncoupled measurement mode as the laser and receiver are both turned independently of each other to take measurements. The ROTALIGN® ULTRA and the OPTALIGN® SMART both feature superior single-beam sensor technology that allows uncoupled measurements to be taken accurately. The ROTALIGN ULTRA takes it a step further with its useful “pass mode”. The “pass mode” automatically takes measurements each time the laser is rotated past the receiver, thus reducing the time to take measurements.
by Daus Studenberg CRL
There is more to proper shimming of a machine for alignment than meets the eye. There are several things you should keep in mind and look out for.
First and foremost, you should be using high-quality pre-cut slotted stainless steel shims, such as Lawton Precut SS-304 Shims. If you think cutting your own shims by hand out of cheaper rolls of carbon steel or brass shim stock will save you money, you are very much mistaken. For one thing, you will only be able to cut the thinner thicknesses with scissors or shears; thicker thicknesses (over 0.004″) will require the acetylene torch or sawing, which is labor-intensive and presents safety concerns. After you have cut your shims by hand, you must take pains to debur them carefully with a ball-peen hammer and file. All of this costs you the most valuable commodity of all: time. Moreover, the end result will be fewer available shims resulting in less precise alignments. And, if you are cutting shims by hand, don’t forget to budget the time to visit the nurse for a Band-Aid.
Download Best Practices: Machinery Alignment Shimming including:
- Advantages of Precut Stainless Steel Shims
- Number of Shims
- Shimming Technique
- Unusual Circumstances: Step-Shimming
- Chart of Horsepower Ranges and Motor Frame Numbers Associated with the Different Sizes of Shims
- and more.
by Alan Luedeking CRL CMRP
On a recent alignment consultation, we were requested to verify the straightness of a stern tube on an oil tanker. It is critical that the stern tube be bored so that it matches the line of the propulsion shaft that will be passing through the center of it. The reason is that the next operation will involve the hydraulic insertion of Babbitt bearings into the stern tube. It would be a very costly operation to undo this is if it were not done correctly the first time.
Upon arrival, the customer’s engineer on site noted that the surface was just machined, but not prepped for accurate measurement by the removal of burrs and machining marks. He wondered if this would affect our measurement. We told him that it could affect any bore measurement, but some unique features of CENTRALIGN® ULTRA would let us know if it did. CENTRALIGN ULTRA offers the following to perform this job AS-IS:
- Single point bracket –The single point brackets are designed to give extremely accurate readings that are independent of the user’s skill and ability. Springs consistently position the plunger on each point around the bore – accomplishing a more accurate translation of the bore surface to the sensor. The result is a true measurement of out-of-roundness and averaged surface finish.
- Standard Deviation – It takes a minimum of three points on a bore to obtain its center position with tightwire, laser, or optical bore measurements. CENTRALIGN allows for more than three points to be taken. With this, the points can now automatically be fitted to a virtual circle that can reveal not only a center position but also the quality of the measurement. In essence, Standard Deviation lets us know, “Is what we measured round? If so, on average, how round was it?”
If the measurement had a low Standard Deviation, then we would know the bore that was measured was round. If a nick or a burr was accidentally measured or if the surface finish was rough, you would see higher Standard Deviation results. It turns out there was no need for any further surface preparation as CENTRALIGN indicated that the measurements were excellent and the single point bracket had not measured on a nick or bump. Standard Deviation was under 0.5 thousandths and repeatability averaged 0.2 thousandths per measurement. The entire measurement took under 1 hour from arrival to departure of the job location.
by Daus Studenberg CRL
Dial indicators are ubiquitous in shaft alignment; they have been used (and misused) extensively for alignment throughout the industry for many years. In the right hands, a very accurate alignment can be performed with dial indicators. However, even under the best of circumstances, it will be a time-consuming task with many traps and pitfalls for the unwary or the untrained.
Using dial indicators properly for shaft alignment is almost an art form. One key consideration is the measurement setup. What method should be used? The Rim & Face Method? Rim & Reverse Face Method? Reverse Indicator Method? Rim & Two-Face? The Face-Face Distance? Each setup may be appropriate for one situation but not for another. Extensive training is required to make this decision correctly. In addition, some proficiency with algebra and geometry will inevitably be required to make sense of the readings taken and calculate corrective moves for the machines.
Once the proper method has been chosen, initial setup preparations require the millwright to check for sag. Sag (also called bar sag) is the result of gravity acting on the overhung hardware spanning across the coupling that holds the indicator(s). It is always present, and its magnitude and repeatability must be accurately measured and known for the millwright to have any hope of measuring the misalignment accurately.
The effect of bar sag is doubled: When initially zeroed at the top, this radial (rim) indicator is already sagging; when it is rotated 180 degrees, it now sags in the opposite direction, doubling the travel of the indicator.
Over longer spans (such as with spool piece couplings or jackshafts), sag can quickly become unmanageable, forcing the use of alternative compound setup methods. Sag will also affect a face (axial) indicator but to a lesser extent. When bar sag is ignored, the impact on the readings can be very significant, rendering the data obtained misleading, or at worst useless.
Besides sag, field conditions may conspire to bedevil the results. Consider the following:
Vibration and Dial Indicator:
Surrounding running machines may cause vibration to enter the machines you are aligning, making the indicators vibrate as well. Because of the overhung installation of the indicator and its supporting hardware, this vibration tends to be greatly amplified at the indicator itself, to the point where it becomes difficult to read accurately, or even impossible to read at all.
Tilted Dial Indicator:
Space constraints may force you to install the indicator at an angle to the reference surface being measured. This tilting will lead to a significant error in the readings as the movement being measured results in a significantly reduced travel of the indicator stem. The only way in which the travel of the indicator stem can accurately reflect the movement being observed is for it to be mounted perpendicular to the direction of the movement being measured.
Parallax Effect and Reading Error:
If space constraints do not allow you to view the face of your dial indicator squarely, you may misread the indicator by several thousandths of an inch. Also, if the travel of the indicator stem is not observed all the way around, a huge reading error may occur if the needle reversed direction during rotation and the millwright did not notice this. The consequences of such a mistake might be recording a reading as +40 mils when in fact it should be –60 mils! A similar error can occur when reading an indicator with a mirror in order to be able to see it at locations that are inaccessible to the naked eye, or from not noticing that the indicator stem is no longer contacting the reference surface.
Dial Indicator Resolution:
Another concern is the measurement resolution of the dial indicator. If a delicate measurement task is undertaken, such as measuring the effect of machine frame distortion by observing the angular changes at the coupling, it must be remembered that these effects dwindle through mechanical looseness and the fact that the shaft is midway between the feet laterally; thus, when one machine foot is loosened, the effect on the shaft is halved. This, coupled with an insufficient measurement resolution of the indicator may render the reading inadequate to perform a meaningful diagnosis of the distortion condition.
Dial Indicator Hysteresis:
Hysteresis of the indicator may also conspire to reduce the accuracy of your readings. Hysteresis is the friction of the internal moving parts of the indicator mechanism. The best dial indicators use precious jewels in their movements (like fine watches) to keep them from “sticking”. This makes them delicate instruments that must be handled with great care. Dropping a dial indicator or subjecting it to extremes of heat, cold or humidity may exacerbate hysteresis conditions to the point that the indicator becomes inaccurate or inoperative.
End Float (Axial Play):
End float, or shaft end play, can bedevil a face indicator. This is particularly true on machines with journal bearings or sleeve bearings that permit a certain amount of axial play to occur in the shaft as it is rotated. This will play havoc with the accuracy of a face (or axially mounted) indicator. It can only be overcome by rotating the shafts while applying significant thrust load (which is often impracticable) or by means of the Rim & Two-Face Method, whereby two face indicators are mounted on the same setup 180 degrees opposed from one another. When the shafts are turned, end float will affect both face indicators equally and therefore only the difference in their readings is observed, arriving thereby at the true gap difference between them. However, a great disadvantage of this method lies in the fact that an extra indicator is now required to be mounted, which in turn requires full rotational clearance all the way around; in addition, the extra indicator significantly increases the bar sag of the entire setup.
Obstructions to Rotation, Measurement Range, Algebra, and Geometry:
The millwright using dial indicators must be proficient in geometry to understand the meaning of the readings he is obtaining; then, he must also be proficient in algebra to perform the necessary rise over run calculations needed to obtain the corrective moves for the alignment. One alternative is a full rotation of the shafts when obstructions to rotation exist is to rotate the shafts only 180 degrees and extrapolate the fourth (or missing) reading through the mathematical circular validity rule. This requires some mathematical skills of the technician in the field. Moreover, the nature of misalignment is such that an elliptical math model is more accurate than a circular one; however, neither the resolution of the dial indicators nor the math skills of the technicians in the field are equal to the task of applying these models in the calculation of results.
When radial obstructions to rotation exist that do not allow for even a half rotation of the shafts, very few millwrights have the necessary mathematics skills to compute the misalignment conditions and corrections from shaft rotations of less than 180 degrees. Moreover, if misalignment causes the indicator stem to run out of range, it must be repositioned for a fresh range, adding complexity to the calculations, since segments of readings must be “spliced” together. If an indicator bottoms out the entire reading process must be begun again since the initial starting reference position of the indicator has been compromised.
All of this tells us that performing competent shaft alignment with dial indicators is a painstaking and time-consuming task. As we have seen, there are numerous potential pitfalls and conditions that make extensive training and experience a necessity in achieving good results with dial indicators, and an unavoidable expense in downtime in getting the job “done right the first time.”
Is there a better (and faster!) alternative to using dial indicators?
Of course, there is! Laser Shaft Alignment
by Alan Luedeking CRL CMRP
The best alternative to using dial indicators for shaft alignment is to use a good laser alignment system such as the ROTALIGN® ULTRA or OPTALIGN® SMART. All the inherent problems and disadvantages of dial indicators are immediately eliminated. Here’s why:
- Training: Far less training and expertise is required of the millwright to use a laser system proficiently than to use indicators. No algebra or geometry skills are required for the technician to perform excellent alignments since the system performs all necessary calculations automatically. The entire setup, measurement, and correction process can be accomplished in less than half the time required with indicators. This saves downtime and saves money!
- No-Sag: The bracketing and components of the ROTALIGN and OPTALIGN laser systems are carefully designed to have their center of gravity directly between the support posts that hold them. The laser beam itself is weightless and thus no-sag exists with these laser systems. This saves setup time since sag does not have to be measured nor accounted for.
- No effect from End Float: The optical measurement principles used by the ROTALIGN systems render them entirely impervious to the effects of shaft end float, since the axial distance between sensor planes in the receiver is fixed. In the OPTALIGN system end float has no effect on angularity whatsoever due to the optical principles of a roof prism; the effect on the offset is negligible because even at the worst angles typically existent between misaligned machines the impact on the projected offset from the axial play is less than the measurement tolerance, whereas a face indicator is impacted directly by end float by the full magnitude of the axial displacement.
- Vibration mitigation: Even the most severe vibration from surrounding machines presents no problem for three reasons: First, the components are not overhung and therefore do not amplify the vibration. Thus the vibration of the components cannot exceed the amplitude of the vibration itself at the points on the machines where they are mounted. Secondly, the averaging of the readings can be adjusted so that the effect of any vibration on the laser beam is totally negated. Thirdly, the artificial intelligence that is programmed into the firmware of the system fires the laser beam at random intervals so that its pulse rate can never be in phase with any vibration. Thus all of the conditions that can render a dial indicator useless in these circumstances are eliminated.
- No Reading Errors or Parallax Effects: None of these potentially great human errors is possible with the ROTALIGN or OPTALIGN laser systems because all data collection is fully automated.
- No Tilting Error: As long as the laser system components can be securely mounted on the shafts or solid coupling hubs, no error can occur since the only movement registered is that of the beam across the sensor caused by misalignment of the shafts as they are turned. This is true even if the laser, prism, or receiver components are mounted cocked, or tilted with respect to each other!
- No Hysteresis Problem: No hysteresis errors can occur because there are no moving parts in the laser system components that can be affected by environmental conditions or rough handling. In fact, ROTALIGN and OPTALIGN systems are waterproof, shockproof, and dustproof. They can therefore withstand the rigors of use in an industrial environment far better than a delicate dial indicator.
- Measurement Resolution and Obstructions to Rotation: ROTALIGN and OPTALIGN have a measurement resolution of just 1 micron (0.00004″). This together with sophisticated artificial intelligence-based elliptical math models programmed in the firmware means highly accurate shaft alignment results can be obtained with only 70 degrees of shaft rotation, starting anywhere and stopping anywhere. ROTALIGN and OPTALIGN are totally independent of the clock positions that must be arrived at when measuring with indicators. Thus, obstructions to rotation are no longer a problem. The systems’ high resolution also means they are ideally suited to the task of measuring machine frame distortion at the coupling, sparing the millwright the problems and inaccuracies associated with mounting indicators at the machine feet for soft foot measurement. This too saves time and money.
by Alan Luedeking CRL CMRP
Yes, pipe strain is soft foot!
Soft foot means machine frame distortion. If you are missing shims under a foot and tighten the hold-down bolt until you have forced the foot down to the base, you will have distorted the machine frame. If you have severe pipe stress on a pump, and the anchor bolts are tight, chances are great you are also distorting the pump casing.
Consider that if the pump’s anchor bolts were completely loosened or removed, the pump might be hanging in the air from the piping. So if you were now to tighten the anchor bolts, you would be forcing the pump down to the base and distorting it, just as happens when you are missing shims under a foot.
Shimming the feet will rarely solve the problem completely; rather, the correct solution is to eliminate the undesirable pipe stress. “Stress” is the force acting on something, while “strain” is the deflection or distortion resulting from the stress. A soft foot condition means you have machine frame strain, and pipe stress is just one of several examples of this. When the machine casing is distorted, the internal alignment between the bearings is changed and the shaft is deflected. This produces enormous stress on the bearings and increased vibration in your machines, resulting in premature wear and tear as well as loss of efficiency. Your seals and bearings will fail much faster. If a significant soft foot condition exists, a good alignment of the centerlines of the shaft rotation is almost pointless. The machines will still fail more quickly and lose efficiency. How do we diagnose and fix this?
The trick lies in knowing how to recognize that a pipe strain problem exists. The behavior of a machine with pipe strain differs significantly from one whose soft foot condition is caused by one of the more traditional shimming problems or unevenness of the base or feet. Fortunately, there is an easy measurement solution: The Pipe Strain Wizard in the OPTALIGN® SMART. The Pipe Strain Wizard will guide you through all of the necessary steps to quickly and easily ascertain whether a pipe strain problem exists and measure its precise impact on the shaft alignment.
Essentially the process involves taking an initial reference reading of the shaft alignment condition. Thereafter the piping is completely loosened and a second reference reading is taken. The wizard then calculates the difference and yields the results.
These results can be documented in a full-color Pipe Strain report printed directly from the OPTALIGN SMART to a USB memory stick as a PDF file.
Any impact on the alignment of more than about 2 mils indicates a pipe strain problem that should be dealt with. Correcting pipe strain is a task for an experienced pipefitter who must see to it that connecting and torquing the piping should not move the machine from its rough aligned condition, nor distort its casing in any way. Proper pipe hanging techniques and a good knowledge of calculating and designing “Dutchman” spacers are essential.
by Alan Luedeking CRL CMRP
Being bolt-bound means you have to move the machine sideways to get it aligned and you can’t: you’ve run out of room. The anchor bolt is up against the side of the hole in the foot.
Being base-bound means you need to bring the machine down to get it aligned, but you can’t: the machine feet are down against the base and there are no more shims left to remove from under them.
Are you in a quandary with either of these situations? No problem! You have five possible solutions:
- Open up the holes in the feet.
- Turn down the anchor bolts.
- Redrill and tap new holes in the base.
- Make an “Optimal Move”.
- Make a “Rolling Move”.
Let’s take the last one first. Making a rolling move of a bolt-bound machine simply means shimming up one side of the machine but not the other (or lowering one side but not the other.) This displaces the horizontal centerline of rotation of the shaft. But this is a big no-no! Do not do this! It will create angled soft feet and distort the machine frame when you tighten them because the feet are no longer evenly supported. Moreover, with gearboxes, you may change the gear mesh pattern and destroy the machine. Many machines must be carefully leveled in addition to being aligned, so rolling moves are out!
Download entire article including making an “Optimal Move” with ROTALIGN ULTRA.
by Alan Luedeking CRL CMRP
ENERGY-TECH • January 2012
At a power generating station in Florida, a severe electrical fault caused such extensive damage to a 40 MW gas turbine-driven generator that a complete replacement of the generator stator was required. An on-site spare generator core was available but needed the faulted generator’s bearing support brackets to be installed to make it complete. As this combination of bearing support brackets and generator frame would be considered a “mismatch”, it was decided that the position of the bearing supports should be verified to ensure proper centralization of the generator’s field (rotor) relative to the generator core.
The primary objective was to accurately determine the centerline position of the generator core and position the bearing support brackets so that an equal radial air gap between the rotor body and core laminations would be obtained during generator operation.
The exact positioning of the support brackets was accomplished using specialized tooling such as the CENTRALIGN® ULTRA laser bore measurement kit and the ROTALIGN® ULTRA laser tool from LUDECA.
Read the entire article Internal component alignment of 40 MW A.C. generator by our customer Chuck Hildebrand, Dynamic Balancing Company.
by Ana Maria Delgado, CRL
When aligning a vertical flange-mounted machine, it can be helpful to tweak the flange configuration in your laser alignment system to take advantage of different shimming alternatives. For instance, if the OD of the flange is larger than the diameter of the mounting bolt circle, a good laser system will compensate for this by taking into consideration that when shimming your pivot point is not the bolt circle but the flange OD. Thus, all shimming corrections will be positive.
However, if you already have shims at all the bolt positions, you could take advantage of the opportunity to minimize the required shimming corrections by forcing the smallest correction position to be zero. Do this by entering a distance for flange OD as being equal to your bolt circle. Of course, the best laser systems already allow for all the different shimming alternatives (positive, negative, and zero-sum options) right in the software, so you don’t have to use this trick.
by Ana Maria Delgado, CRL
TransAlta from Alberta, Canada won Uptime Magazine’s Best Vibration Analysis Program. Their Vibration Journey started when due to distance and the high costs of using a contractor, they moved away from outsourcing their vibration analysis services to a full-time in-house vibration analyst.
During the implementation and mentoring period, and in spite of the business justification, they faced challenges like skepticism from the maintenance department and having to continually justify their existence. Buying and implementing new technology was easy but changing the culture was difficult. Some of it was overcome with their ability to be 100% correct on the calls they made for failures although at the beginning they did not catch all the failures. 10 years after their vibration program started, there are no more skeptics.
An important element of their success was the implementation of a training and certification program with a budget that allowed for 2 weeks of training per year per analyst. They also required that personnel take CMVA Level 1 (Canadian Machinery Vibration Association) or equivalent followed by Level 2 after 18 months and Level 3 within four years on the job.
Aside from bringing Vibration Analysis in-house, they also implemented other in-house programs such as Laser Alignment, Balancing, Ultrasound, Lubrication, and Thermography.
What did they accomplish? Savings of US$ 4,000,000 per year for their company over 1,600 pieces of equipment at 3 separate plants.
When first asked about their program, Mark Kumar told Terry O’Hanlon, publisher of Uptime Magazine, that their Best Asset was their vibration database (history) which allowed them to diagnose failures but now in retrospect, he stated that their Best Asset was the Backing of Company Management which supported their initiative for an in-house vibration program.
Congratulations to Harvey Henkel, Mark Kumar, and their team for this award and a job well done.
by Ana Maria Delgado, CRL
Domtar Espanola from Ontario, Canada won Uptime Magazine’s Best Asset Health Management Program. Their goal was “Go from Reactive Maintenance to Proactive”.
To achieve this goal, they put together a plan including several proactive actions and PdM technologies integrated with an Asset Performance Management Software which allows them to closely monitor equipment health. Kim Hunt shared some of their plan elements:
- Implement a precision lubrication program and oil analysis
- Skills training: Value your staff and empower them with training. From formal training to just watching Reliabilityweb Webinars together and afterward eating cookies and holding discussions —great for team building!
- Size your equipment properly
- Use laser alignment and balancing for precise machine rebuilds and installs
- Precise operator care
- Maintain excellence in housekeeping
- Equipment health monitoring. Use predictive tools, primarily vibration analysis to baseline your equipment.
- Root cause analysis and problem elimination
- Plan and schedule your maintenance activities with effective standard operating procedures
- Continuous improvement – you are never done!
What did they accomplish?
- 21% reduction in maintenance costs
- 30% increase in production efficiencies
- Increase MTBF (Mean Time Between Failure)
- A total average savings of US$450,000 per year without actual/potential product loss.
Congratulations to Kim Hunt and her team for this award and a job well done.
by Ana Maria Delgado, CRL
“Does misalignment waste energy?” is a question often asked. The answer, emphatically, is yes! General Motors Corporation and Ludeca performed and published a study on this issue in 1993 which showed conclusively that energy savings (Real Power savings) of 2.3 percent could be obtained on loaded machines. On unloaded machines, the savings ranged as high as 9 percent! At ICI Chemicals, a UK chemical plant in the north of England, a carefully controlled doctoral research project revealed even higher savings. Other studies suggest averaged savings of 4 to 5 percent.
In late 1993, Infraspection Institute in New Jersey demonstrated in a carefully controlled study conducted at Miller Brewing Company that misalignment generates heat and wastes energy. This was clearly demonstrated in the comparative infrared signatures obtained on the same machines when running in an aligned and misaligned condition with different types of couplings (see Figures 1 and 2.) Precise magnitudes of misalignment were very carefully set with an OPTALIGN® laser system and the results were meticulously examined with calibrated thermograms recorded for each case.
Clearly, the energy required to accommodate the increased sliding velocities from misalignment within flexible couplings must come from somewhere, and this wasted energy comes at the direct expense of the efficiency of the rotating machines. While the percentage of savings may not seem very significant, a plant that reduces energy consumption by 4 percent on an energy bill of $50,000 per month would save $24,000 in just the first year, more than enough to justify the purchase of a higher-end laser shaft alignment system.
Read the entire Shaft Alignment, Soft Foot and Energy Savings
by Alan Luedeking CRL CMRP
PLANT ENGINEERING • November 2011
Friction can cause damage, but it also can be an energy hog.
Keeping your rotating shafts in alignment is a fundamental—and often overlooked—maintenance project. Alan Luedeking, the manager of technical support for LUDECA Inc., Doral, FL, talked with Plant Engineering (PE) about some of the critical issues in shaft alignment, and how they affect safety, energy, and productivity.
by Ana Maria Delgado, CRL
If you are aligning very critical machines and your laser system does not offer you the ability to apply vector tolerances, you can still do so manually, by keeping these criteria in mind:
The standard industry norms of 2 mils offset and 0.3 mils per inch of angularity at 1800 rpm equate roughly to vectors of 1.4 mils of offset and 0.17 mils per inch of angularity. Therefore, you can apply a sliding scale when you look at your misalignment results: If you have misalignment only in one plane (either vertical or horizontal), apply the full value of the standard tolerance; if you have a roughly equal misalignment in both planes apply the more conservative values shown above to both. This way you will not exceed your vector limits in any direction.
To find the vector limits for any RPM, simply take the square root of the standard limits.
Of course, none of this would be necessary if you have one of the better laser systems that feature vector tolerances and calculates them for you automatically.
by Alan Luedeking CRL CMRP
Laser alignment is an essential component of a proactive maintenance strategy for belt-driven machines. This practical guide provides guidelines and information for the implementation of good pulley alignment of belt-driven equipment, including terminology, proper alignment methods, soft foot, and best maintenance practices.
Download your copy now!
by Ana Maria Delgado, CRL
Measuring machinery misalignment with today’s tools, particularly computerized laser alignment systems, and well-designed bracketing is no longer as difficult a task as it once was when all you had were a straight edge, feeler gauges, and maybe a set of dial indicators with some make-shift hardware.
Why then, is it that aligning the machinery to given target values is so often still so cumbersome and time-consuming? There may be several reasons, among them unnecessarily tight tolerances specified by the machinery vendor, problems with worn-out bearings, inadequate bases, lack of jackscrews, etc. But by far the greatest obstacle to expeditiously reaching your alignment goal is soft foot. ‘Soft foot’, or machine frame distortion can be measured by various means, and indeed it must be measured and corrected before proceeding with the alignment. Why? Simply because an uncorrected soft foot condition will make alignment a trial-and-error procedure where indicated corrective shimming and lateral moves no longer bring you to the expected results.
Severe soft foot may also be quite harmful to the machinery itself.
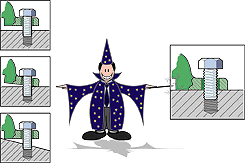
Correcting soft foot may not be easy, but it is worth every minute you spend on it because once done, the alignment of the machines becomes a much easier task. Many alignment systems available today have soft foot measuring programs, and the most advanced system even features a soft foot ‘wizard’ which analyzes the type of soft foot measured (there are a number of different soft foot conditions) and suggests how to correct it.
Conclusion: If you want to make aligning your machinery easier, quicker, and more accurate, start by correcting soft foot.
Read: Types of Soft Foot
by Ana Maria Delgado, CRL
One of the problems we can encounter while performing an alignment is the re-use of old washers. Sometimes it isn’t enough to replace all the used bolts, nuts, and shims. You need to replace old washers too.
They are just as simple to replace and as inexpensive as the bolts and nuts you are also replacing. Dished washers will try to center themselves in the bolt hole of the foot and will pull your machine out of alignment, even if you are very careful in your torquing procedure. This effect is virtually impossible to overcome and at times even to detect (unless you are using the live move function on a ROTALIGN® laser alignment system), resulting in a difficult alignment to finish properly, even if you have followed every step correctly. Make sure to discard all damaged or inappropriate washers on the movable machine and replace them with thick, good quality Grade 8 new washers.
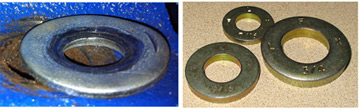
Another issue is the use of lock washers. Generally, a good flat washer under a bolt head with a good washer seat that has been correctly tightened to the proper torque does not need additional security; however, if your application requires a lock washer due to severe vibration, or because the join needs to be allowed to expand while still maintaining the required amount of axial force on the closure, then a high-quality lock washer may be the right solution. Avoid the use of cheap, one-time-use split-ring lock washers, and use a high-quality Belleville washer (a conical disc spring washer) instead. A split ring lock washer exerts 90% of its force in the first 20% of its travel range, therefore it is a very ineffective solution to the problem attempting to be solved; a Belleville washer, on the other hand, exerts 100% of its locking force over 100% of its travel range, and moreover also serves the functions of a flat washer. In addition, they can be stacked in parallel to increase the axial locking force, or in series to increase both the locking force and the travel range.
by Ana Maria Delgado, CRL
Thank you for joining us for our Webinar Detecting Misalignment through Vibration Analysis. We hope you found the presentation to be valuable and very informative. If you missed our Webinar, you can view the recorded version at any time. Watch now!
Here are the answers to your questions:
Q: How do you account for thermal growth when installing new or repaired equipment?
A: If you already know that the machines will move as you run them, you must misalignment them ‘cold’ to compensate, so they grow into alignment as you run them. The trick, of course, is to know exactly how much! There are various methods to ascertain this precisely, the best being to perform a live monitoring job with PERMALIGN® or ROTALIGN® ULTRA Live Trend. To fully answer your question, I’d suggest that you take a peek at our Webinar “Thermal Growth and Machinery Alignment”
Q: If using a dual-channel phase without tacho, do you recommend orientating accels axially for angular misalignment detection and orientating accels radially for parallel misalignment? Is this relative to using 2 channel cross-channel phase to determine angular or parallel phase?
A: Both types of phase measurements are easy to take. The relative phase is the most convenient way to measure phase on a machine because the machine does not need to be stopped to install reflective tape on the shaft. Phase can be measured at any frequency. Most single-channel vibration analyzers can measure the absolute phase. Multi-channel vibration analyzers like the VIBXPERT have standard functions for measuring both absolute and relative phase. See below section “When to use Phase Analysis”
Q: Can’t you only find imbalance from phase?
A: Phase data can be used to verify a lot of vibration issues including imbalance, but it is not only for imbalance itself. I have included a few examples of what issues can be detected below by using phase. Both types of phase measurements are easy to take. Relative phase is the most convenient way to measure phase on a machine because the machine does not need to be stopped to install reflective tape on the shaft. Phase can be measured at any frequency. Most single-channel vibration analyzers can measure absolute phase. Multi-channel vibration analyzers like the VIBXPERT have standard functions for measuring both absolute and relative phase. See below section “When to use Phase Analysis”
When to use Phase Analysis
Everyone needs phase analysis. A phase study should be made on problem machines when the source of the vibration is not clear or when it is necessary to confirm suspected sources of vibration. A phase study might include points measured only on the machine bearings or it can include points over the entire machine from the foundation up to the bearings. The following are examples of how phase can help analyze vibration.
Soft Foot
The term soft foot is used to describe machine frame distortion. It can be caused by a condition where the foot of a motor, pump, or other component is not flat, square and tight to its mounting, or many other things, such as machining errors, bent or twisted feet and non-flat mounting surfaces. Soft foot increases vibration and puts undue stress on bearings, seals and couplings. Soft foot on a motor distorts the stator housing creating a non-uniform rotor to stator air gap resulting in vibration at two times line frequency. A good laser shaft alignment system should be used to verify soft foot by loosening the machine feet one at a time. I’d suggest that you take a peek at our Webinar “Soft Foot”
Phase can be used to identify soft foot while the machine is in operation. Measure the vertical phase between the foot and its mounting surface. If the joint is tight, the phase angle is the same between surfaces. If the phase angle is different by more than 20 degrees, the foot is loose or the machine frame is cracked or flimsy.
Cocked Bearings and Bent Shafts
Phase is used to detect cocked bearings and bent shafts. Measure phase at four axial locations around the bearing housing. If the bearing is cocked or the shaft is bent through the bearing, the phase will be different at each location. If the shaft is straight and the bearing is not twisting, the phase will be the same at each location.
Confirm Imbalance
A once-per-revolution radial vibration usually means rotor unbalance. Use phase to prove imbalance is the problem. To confirm imbalance, measure the horizontal and vertical phase on a shaft or bearing housing. If the difference between the phase values is approximately 90 degrees, the problem is rotor unbalance. If the phase difference is closer to zero or 180 degrees, the vibration is caused by a reaction force. An eccentric pulley and shaft misalignment are examples of reaction forces.
Looseness, Bending, or Twisting
Phase is used to detect loose joints on structures and bending or twisting due to weakness or resonance. To check for looseness, measure the vertical phase at each mechanical joint. When joints are loose, there will be a phase shift of approximately 180 degrees. The phase angle will not change across a tight joint.
Shaft Misalignment
Shaft misalignment is easily verified with phase. Measure each bearing in the horizontal, vertical, and axial directions. Record the values in a table or bubble. Compare the horizontal phase from bearing to bearing on each component and across the coupling. Repeat the comparison using vertical then axial data. A good alignment will show no substantial phase shift between bearings or across the coupling.
Operational Deflection Shapes
Instead of comparing the phase and magnitude numbers from a table or bubble diagram, operational deflection shape software (ODS) can be used to animate a machine drawing. An ODS is a measurement technique used to analyze the motion of rotating equipment and structures during normal operation. An ODS is an extension of phase analysis where a computer-generated model of the machine is animated with phase and magnitude data or simultaneously measured time waveforms. The animation is visually analyzed to diagnose problems. ODS testing is able to identify a wide variety of mechanical faults and resonance issues such as looseness, soft foot, broken welds, misalignment, unbalance, bending or twisting from resonance, structural weakness, and foundation problems.
Phase and magnitude were measured from permanently mounted X and Y displacement probes on a turbine generator. The values listed in the table were used in ODS software to animate a stick figure drawing of the high- and low-pressure turbine shafts and the generator shaft. The picture to the right of the table is a capture from the ODS animation showing the vibration pattern of each shaft and the relative motion between shafts at 3,600 cycles per minute (turning speed).
Many machines vibrate due to deteriorated foundations, looseness, the resonance of the support structure, and other problems that occur below the machine bearings. A phase study might include hundreds of test points measured all over the machine and foundation. Good ODS software can make it easier to analyze phase and magnitude data from a large number of test points. Analysis of an ODS involves observation and interpretation of the machine in motion.
Q: Will coupled drive and belt drive systems show up the same on the spectra?
A: Yes, vibration data on a belt drive system will look different from a coupled drive but not when looking at the common defects of a machine. For example, the vibration data on a belt drive motor will show additional vibration below turning speed due to the belts. The common defects such as imbalance, looseness, and misalignment (to name a few) will show up the same on a belt drive system or a coupled drive system.
Q: In the below spectrum we see a looseness, do we need to correct first the looseness before the misalignment?
A: When looking at vibration data there is always more than one issue showing within the vibration data. I suggest correcting the highest amplitude vibration issue first and the second issue will usually decrease in amplitude. For example, on this vibration spectra, I would suggest correcting the misalignment issue first. The misalignment is the root cause affect of the looseness. Once the misalignment issue is corrected the looseness issue will not be seen on the spectra data.
Q: Will this show up in both horizontal and vertical or is it predominately just one or the other?
A: The answer is that an alignment issue will show up in both the horizontal and vertical orientation when collecting vibration data. Of course, depending on the type of misalignment the horizontal or vertical orientation could be higher. Once a single orientation has a high amplitude level of misalignment it will cross over into the other orientation as well. Of course, if the alignment issue has a small amplitude level it might only be noticed in a certain orientation and again that depends on the type of misalignment that is present.
Q: How can vibration analysis instrumentation be integrated into a building’s BAS computer system?
A: There are generally two different vibration programs that exist in a plant. One would be walk around data collection. This is where a person goes out and places a sensor on a machine to collect the vibration data and then transfers that vibration data in a database. The second would be continuous monitoring where sensors are permanently mounted to a machine. Vibration data is collected every minute or less depending on the need. The walk-around vibration database does have a SAP export feature that would allow you to export certain data from the database over into your system.
In most cases continuous monitoring is best to feed data into another system. We have customers that use our continuous monitoring devices (online systems) to feed into their SCADA systems. This allows for an overall value of 4-20 MA signal to be sent across into another system. Now the other system, like the SCADA, can now alert if certain levels have been reached.
Q: What vibration is typically associated with a damaged impeller or damaged fan blade?
A: The vibration associated with a damaged impeller or fan blades is called vane pass frequency. When looking at the spectra vibration data you would be interested in the number of vanes or impellers that are on the machine. For example, if you had six vanes the vibration data would show a peak in the spectra data at 6 times turning speed, 12 times turning speed, 18 times turning speed, 24 times turning speed, and 30 times turning speed. Depending on the frequency maximum for your spectra would determine how far out the vane pass frequency would occur or be seen.
Q: When we laser align our mechanics say they can’t keep their coupling gap correct. What is a good method to laser align and maintain the coupling gap at the same time?
A: There are two kinds of coupling gaps we have to keep in mind when aligning a machine. The first is the simple gap difference between the coupling faces arising out of any angular misalignment between the shafts, and the second is the axial installation gap specification and tolerance that is demanded by the manufacturer of the coupling.
Typically, you rough align the machines and then set the installation gap of the coupling before you completely tighten it down. If the hubs are shrunk fit, then you guide yourself by the position of the hub on the shaft ends and hope your holes in the base are drilled in the right place when your machines are set down. The correction of any misalignment (angular and offset) typically will never affect the installation gap by enough to make any difference, since we are talking about changes to angularity in thousandths of an inch, whereas the installation gap may have a tolerance of as much as a quarter-inch in or out. So I’m not exactly sure what your mechanics are concerned about. With a good laser alignment system, you perform both angular and offset corrections simultaneously, and the axial gap between the couplings is not a concern.
by Mickey Harp CRL
What if you could reduce machinery alignment time from 4 hours to 2 hours? What if you could improve the average alignment from 9 mils to 3 mils? What if your Meantime Between Failure (MTBF) could be increased from 30 to 34 months, 13% (very conservative)?
Consider this: A plant with 200 machines at an average of 30 HP and a Mean Time Between Failure (MTBF) of 30 months are aligned using dial indicators. With the same conditions and a ROTALIGN® ULTRA or OPTALIGN® SMART laser alignment tool, the following savings could be expected to occur:
- Power: $7, 125
- Repair Costs: $18,823
- Labor: $15,040
A total of over $40,000 per year!!!
Contact us today to see how Laser Alignment can increase reliability and productivity at your shop or to request your Return On Investment Study.
by Ana Maria Delgado, CRL