Maintenance planning, scheduling, and work execution are all critical for the success of best practice returns in maintenance and reliability. Unfortunately, it is easy to confuse and merge these processes together, thereby lowering the efficiency of maintenance activities and the overall health of manufacturing assets. The reality is that each of these efforts is dependent on each other, but separate and critical functions in a well-organized maintenance process.
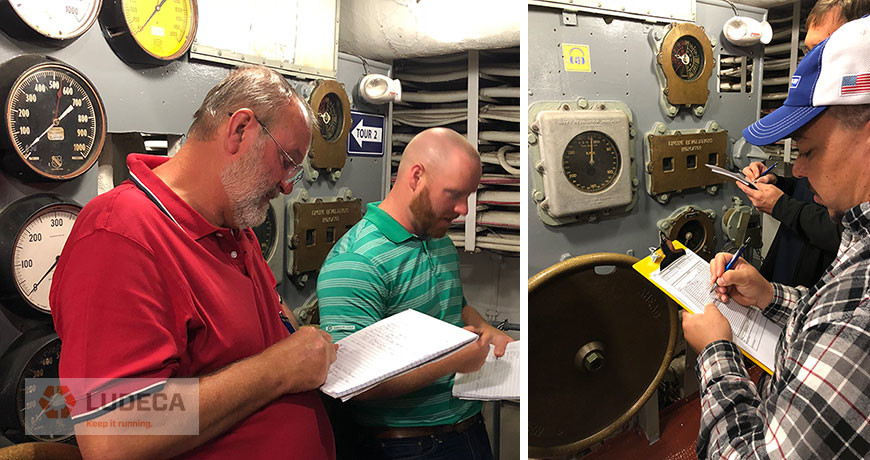
“We should always plan first, schedule those planned activities and finally ensure the work is properly executed on-time with precision”
The following are stages in creating a well-organized successful maintenance program:
- The first stage in the process is creating a “Work Order Request”. The requestor should always clearly specify “where”, “what”, “why” and “severity” of the work required and enter the work request as early as possible. Work order requests should always be reviewed, prioritized, and approved by management from both operations and maintenance. Doing this requires a valid criticality ranking of the equipment, consisting of specific maintenance, operational, and EHS considerations. This creates buy-in from everyone affected and ensures only necessary work approval and progression through the process.
- Once the work request is approved and prioritized, it becomes a “work order” entering the planning backlog and becomes the responsibility of the Maintenance Planner. The Maintenance Planner is a strategic role and should not be involved in daily maintenance work activities. The maintenance planning stage ensures accurate job/work instructions are created, labor skills and hours required are understood, parts availability is ensured or ordered (some parts may have a long lead-time), required support is identified (contract labor support, cranes, etc.) and safety permits identified. The planner should review existing work plans to see if one is already available for this task or create a new job plan if needed. The Maintenance Planner works with the MRO department and is notified when all required repair parts are available. These parts should be kitted, in a controlled area, so everyone knows they are available to complete the work when the time comes. Once the planner has assured these things are complete the work order and process moves to the next stage.
- Now the work can progress to the “schedule ready” phase and the Maintenance Scheduler takes over. At this stage, everything is in place to get the work done. Functional repair steps are correctly written, safety concerns are identified, and permits issued as needed, parts staged, and available to do the work and common and special tools available. The Maintenance Scheduler works with the maintenance and operations management, and coordinates within workforce restraints (vacations, etc.) and places the work on a schedule to be completed. This schedule is reviewed and approved by all stakeholders and posted so everyone is aware of what they will be working on in the days ahead. At this point, every effort is taken not to break the work schedule and ensure it is completed as planned.
- The Maintenance Supervisor now takes over and assigns individuals to complete the work on the scheduled day/week. The Maintenance Supervisor is responsible for ensuring the daily workflow is followed, problems addressed, the work is correctly completed on-time as scheduled. This individual is working daily in the plant with the maintenance and operational groups.
- The maintenance workers should follow the work instructions and provide feedback with missing steps, parts, tools, safety concerns, and issues and actual time to complete the work assigned to them. This feedback is critical because it allows future work to be better planned, scheduled, and executed, thereby increasing efficiency, reducing unscheduled downtime, and saving cost.
- The Reliability Engineer should use all of this information to analyze and determine routine equipment failure patterns and potential ways to eliminate this work from being required in the future through “Reliability Improvement Projects” (RIE), etc.
Within your facility, you may encounter different job titles as described in this article. However, it is extremely important that the overall roles and processes be in place and routinely followed. Not doing so will lead to dysfunctional work processes and prevent your company from achieving best practice maintenance and reliability goals.
For further reading, we refer your attention to Alan Luedeking’s excellent blog: Reliability – A Holistic Effort.
Need a platform that is going to take your planners/schedulers to the next level? Contact our colleagues at Eruditio.
Filed under:
Maintenance Tips, Reliability by Trent Phillips CRL CMRP - Novelis