There are a lot of numbers and stats associated with lubrication; or, with the lack of proper lubrication in this case. For instance, it is said that 60% – 80% of bearing failures are related to lubrication issues of some kind; lack of lubrication, over- or under-lubrication, mixing lubricants that are incompatible, choosing the wrong lubricant for the application (such as the wrong grease or wrong viscosity oil), and finally, simply using a lubricant that is contaminated from the start.
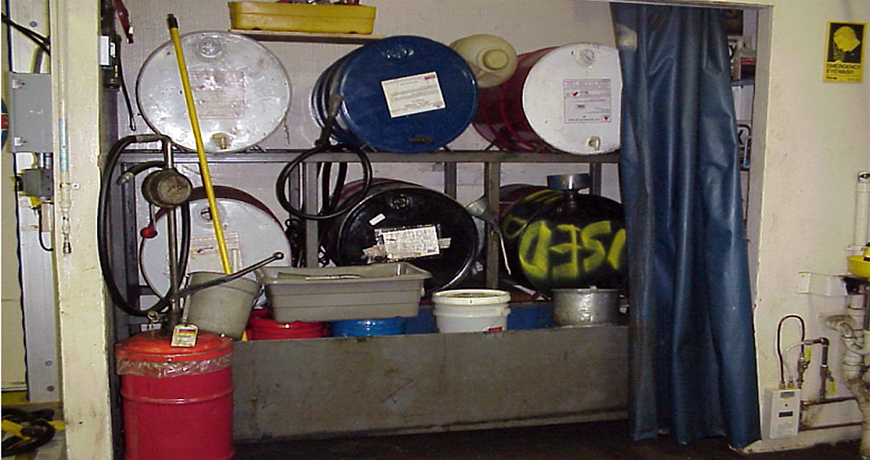
The key to proper precision lubrication starts with the right mindset. We must believe that the lubricant is an “asset” and not just an ugly necessity. If we turn our mind towards precision lubrication with the precise “asset” for the application then our success rate for uptime will skyrocket. Think of trying to use a Philips head screw driver on a slotted screw. Simply put, it is the wrong tool for the application.
If we use a lubricant that is contaminated from the start, what chance are we giving the asset for success? What can we do to make sure the lubricants used are in the best condition for optimum performance? Let’s start at the beginning when the oil or grease first arrives at the receiving dock.
1. If we are receiving an oil, take a sample of the oil to make sure it is the oil that was ordered (proper type: hydraulic, gear, turbine, etc.), and is of the proper viscosity. Then check the cleanliness (particle count/ISO Cleanliness code) in which it was received from the supplier. Set it aside and wait for the results of the analysis before using.
2. Once we get the results back and are satisfied we received what was ordered, we should filter the oil with a kidney loop filtration system of some type because we know that new oil is not clean oil: especially hydraulic standard clean. Filter the new oil before using.
3. Take extra precautionary steps when filling the asset with the now clean oil so as not to contaminate the system with debris that has surely gathered on the asset. Best practice would be to have a completely closed system which filling with oil would require quick-connect adapters so the new oil can be transferred without ever having to open the system by fill port or by removing a lid. If this is not an option, make sure the transfer containers are color coded and sealed; do not use an open container or an open galvanized container. Be very careful not to inadvertently allow debris into the system.
4. The asset itself can be adapted for better success by implementing a desiccant breather, closing fill ports with quick-connects for filling and external filtration and perhaps a bottom water and sediment bowl for water and debris detection and removal.
5. The asset should have a label that matches the label on the oil container in the store room, the oil transfer cart and/or the color coded transfer container.
6. Implement an oil analysis program and keep an eye on the oil and asset health. If the sample comes back with good viscosity and additive levels but is dirty then filter it with the kidney loop system and get the oil back to the desired cleanliness level. Investigate where the particulate is coming from and take steps to prevent future particulate intrusion.
In conclusion, while there are many more steps we can take to maintain a healthy oil and therefore a healthy asset, these are some obvious action items we can implement for better success. Imagine if we turned the negative numbers of 60% – 80% into positive numbers for the company. Clean, healthy oil is an asset for success.
Download our Oil & Grease Storage Best Practices for additional tips to help outline the best practices for proper lubrication storage.
Filed under:
Lubrication, Maintenance Tips by Paul Llewellyn CRL, CLS, MLT-II, MLA-II