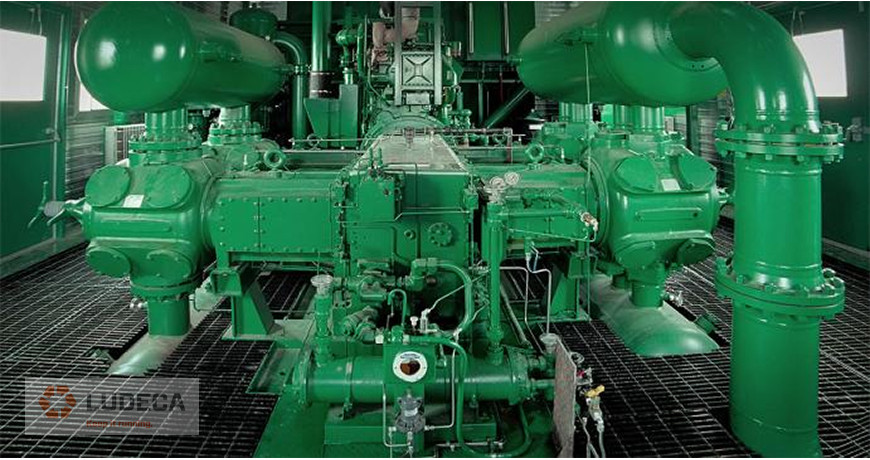
All rotating machinery is installed in trains. Trains mean there is a driver, the motor, and driven, which can be a pump, blower, compressor, or any other type of process machine. During the installation of rotating machinery, precision shaft alignment is performed. The shaft alignment will ensure that both shafts (driver and driven) are collinear. Collinear means that both rotational centerlines are positioned as if they were one.
The effect of heat on driver vs. driven
When the machines are started, the driver and driven heat up in very different ways. A compressor in a hot environment will quickly increase in temperature due to friction of its internal rotating parts, and compression of the media will generate and add more heat. Comparing to the driver, which can be an electrical motor, the situation is very different. The temperature will increase to a certain level and then remain the same — two machines with two different behaviors.
So, what happens when one of them increases its temperature relative to the other? It’s simple; the machine will start expanding. And when the machine expands, it will grow in all directions, move its rotational center out of collinearity and cause misalignment. But not only misalignment. Since there is a change in the machine geometry, pipe strain might also add more stress to the housing.
Take thermal growth into account from the start
There are so many consequences of thermal growth in rotating equipment. Misalignment will, for example, also result in a bent shaft. Bent shaft will result in improper distribution of forces in the bearing, which will lead to failure of the lubrication. Therefore, we must be able to anticipate thermal growth by using available information from the OEM, or by performing the calculation by ourselves. So how do we do that?
The key is to identify how much growth to expect. This number must be used when performing the shaft alignment to “intentionally misalign” the machines prior to start. Let us use the compressor as an example again. If we assume that the compressor will operate at a higher temperature than the motor, when aligning, we must place the compressor below the rotational centerline of the motor. How much below will be determined by the expected thermal expansion growth of the material.
Final test run
When the machine is aligned with the thermal growth considered, it must run and operate until it reaches its full operating condition. Then it must be stopped, and the shaft alignment verified. This is our test run of the machine, to confirm a proper and reliable installation, and to achieve full operational life. We want to test before we go to full production to ensure our thermal expansion calculation was correct.
Think about aircraft maintenance. When there is an aircraft engine replacement, the pilots perform test flights until it can be confirmed that everything is operating as it should. And you don’t want to be on the plane knowing nobody performed the test run, do you?
Watch our Shaft Alignment Know-How: Thermal Growth video to learn the importance of accounting for thermal growth on rotating equipment.
Thank you Roman Megela with Easy-Laser for sharing this informative article with us!
Thermal Growth in Alignment Components: Achieve Reliable Results With These 4 Tips
Filed under:
Alignment by Diana Pereda